What are the manufacturing process steps for precision metal stamping parts? Yiwei Precision Editor will introduce you from the following aspects.
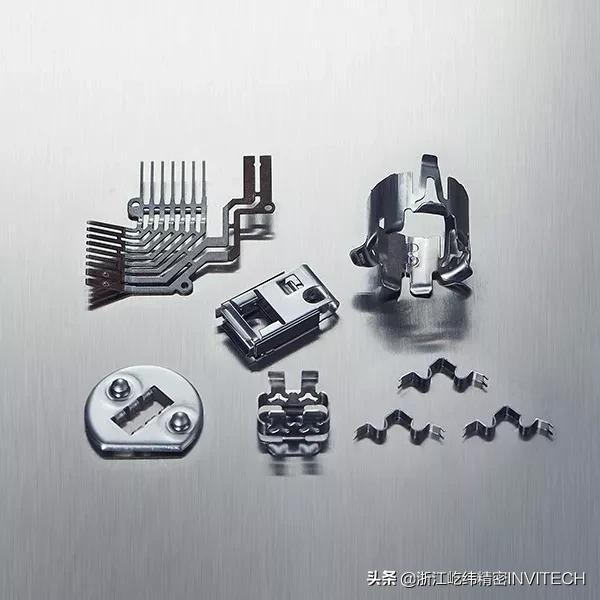
1. Stamping part design
(1) The result of stamping design and implementation is a three-dimensional entity with relevant concepts, such as color, material, hardness, shape, size, position, related parts, and manufacturing process. (2) The emergence of computer technology directly stems from the concept of three-dimensional design, which can more intuitively and accurately express all geometric parameters of design ideas, and can fully discuss the entire design process on a three-dimensional model. (3) Computer technology can help stamping engineers rationalize the design process from a design perspective and gradually create stamping parts from the production of sheet metal and the completion of each process. (4) It can be regarded as a virtual environment for stamping parts. Engineers can directly design and assemble parts on computer screens.
2. Stamping parts development
After the design of stamped parts is completed, it is necessary to convert them into unfolded drawings to determine the size and shape of the required sheet metal. (1) The operation of CAD is small, and the development process is fully controlled. (2) Computer aided design has high efficiency and avoids errors that engineers are prone to make during the development process. (3) Computer aided design has high accuracy, and the extended data is completely calculated by the computer; This avoids the significant food cost of materials.
3. Choose stamping oil
Stamping oil plays a crucial role in the stamping process. Good cooling performance and extreme pressure wear resistance have made a qualitative leap in the service life of molds and the improvement of workpiece accuracy. The selection should be based on the raw materials of the workpiece to match: (1) The selection of stamping oil for carbon steel plates should be determined based on the process and degreasing conditions to determine the optimal viscosity. (2) Due to the chemical reaction with chlorine additives, galvanized steel plates should pay attention to the possible white rust caused by chlorine type stamping oil when selecting stamping oil. Using Yida Borun sulfur stamping oil can avoid the problem of rust, but it should be degreased as soon as possible after stamping. (3) Stainless steel is a material that is prone to hardening and requires the use of oil film strength,
4. Punching board cutting (1) The cutting machine uses scissors to cut the shape of the shape into length and width. If there is punching, corner cutting is performed, and then the punch press combined with the die is rotated to form corner cutting. Its advantage is high time efficiency and it is often used in mass production. (3) Firstly, CNC programming is used for CNC punching. By writing the map into the content of the CNC machine tool, it can be recognized and the shape of the flat part can be molded out step by step according to the content. (4) Laser cutting is the process of cutting flat structures off a board using laser cutting.
5. The general punching process for machine tool boards includes punching angle cutting, punching material dropping, convex bag punching, punching tearing, hole extraction, etc. In order to meet the requirements of each process, corresponding molds are needed to complete the operation, such as convex molds and tearing forming molds.
6. Flat tapping and riveting
Flanging is to draw a slightly larger hole on a smaller bottom hole and then tap it to increase its strength and avoid slipping teeth. Riveting usually uses rivet bolts, rivet nuts, and rivet bolts. The riveting method is usually operated by a stamping machine or hydraulic riveting machine, which can rivet it to the stamped part.
7. Three dimensional bending of flat plates
Bending is the process of cutting flat pieces into three-dimensional parts, which requires a folding bed and corresponding bending molds to complete the operation. It also has a certain bending sequence, and the principle of cutting will not interfere with the initial bending, resulting in eight. The surface treatment of the workpiece is generally phosphating, zinc plating, chromate, painting, oxidation, etc. Phosphating film is generally used for cold-rolled plates and electrolytic plates, and its main function is to prevent oxidation on a protective film on the material on the workbench; Electroplating multi-color zinc is commonly used for surface treatment of cold-rolled plates; Chromate and oxidation are generally used for surface treatment of aluminum plates and profiles.
Aima Technology Co., Ltd. is one of the leading professional manufacturers of precision metal parts in China, established in 2006. It mainly undertakes businesses such as CNC Machining parts, metal stamping parts, and sheet metal processing.