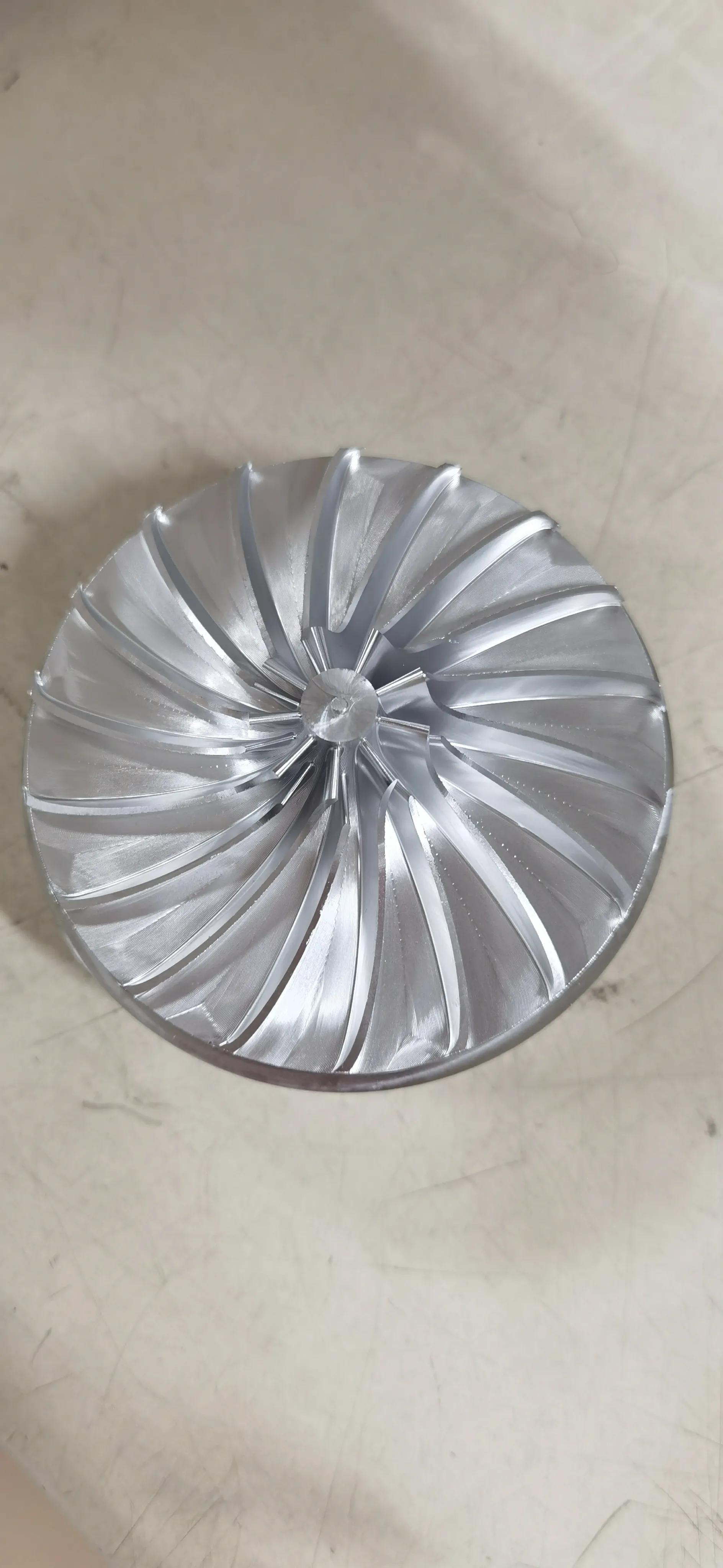
1、 Difficulties in machining the overall impeller
1. The shape of the ternary integral impeller is complex, and its blades are mostly non extensible twisted straight surfaces, which can only be processed by machine tools with five or more coordinates;
2. The space between adjacent blades of the overall impeller is relatively small, and the channel becomes narrower in the radial direction as the radius decreases. Therefore, when machining the curved surface of the impeller blade, in addition to interference between the tool and the processed blade, the tool is prone to interfere with adjacent blades;
3. Due to the thin thickness of the overall impeller blades, there is significant elastic-plastic deformation during the machining process;
4. There are many constraints in tool planning, making it difficult to automatically generate interference free tool paths.
2、 Selection of impeller machining tools and tool holders
1. Selection of Cutting Tools
To improve processing efficiency, it is advisable to use larger ball end cutters for rough machining of blades and use multi blade milling cutters, which can improve processing efficiency;
In the selection of tool structure types, in order to improve tool rigidity, in addition to using large-diameter tools as much as possible, it is also advisable to use tapered ball end tools as much as possible;
The selection of tool materials needs to be based on different workpiece materials to determine the material of the machining tool, whether coated tools are needed, and so on.
2. Selection of knife handle
The structural forms of tool holders for five axis machining center CNC machine tools are divided into integral and modular types. The working part of the integral tool holder that holds the tool is integrated with the handle used for installation and positioning on the machine tool. This type of tool holder has poor adaptability to changes between machine tools and parts. To adapt to the changes between parts and machine tools, users reserve various specifications of tool holders, so the utilization rate of tool holders is relatively low. Modular tool system is a relatively advanced tool system, in which each tool holder can be assembled through various series of modules. By adopting different assembly schemes for different processed parts and machine tools, multiple series of tool holders can be obtained, thereby improving the adaptability and utilization rate of tool holders.
The selection of tool holder structure should take into account both technical and economic rationality. The selection of impeller machining tool holders can be divided into spring-loaded chuck tool holders and side fixed tool holders. The clamping force of spring-loaded chuck tool holders is generated by the increasing force of the nut sleeve, which generates sufficient axial pushing force on the spring to achieve the clamping of the tool. This may cause the spring to loosen and lead to tool dropping under high chip force. Side fixed tool holders generate lateral locking force and do not experience overcutting caused by tool looseness during the machining process.
3、 Process flow of impeller machining
The impeller machining process is divided into several machining strategies, including rough machining of the impeller, intermediate machining of the blade surface, precision machining of the blade surface, and precision machining of the runner surface. The purpose of rough machining is to quickly remove the blank allowance, which is also a strategy to reflect the efficiency of impeller machining. The purpose of semi precision machining is to make the allowance on the blade surface uniform, in preparation for the subsequent precision machining. The purpose of precision machining is to achieve good surface quality, which is closely related to the selection of cutting tools, the matching of machine speed and feed rate.
The improvement of impeller machining efficiency mainly lies in the improvement of rough machining efficiency. By using the five axis impeller rough machining mode, the five axis rough machining of the impeller can be achieved, which can achieve uniform material retention, smoother machining trajectory, and improve machining efficiency.
4、 Process flow of impeller machining
The impeller machining process is divided into several machining strategies, including rough machining of the impeller, intermediate machining of the blade surface, precision machining of the blade surface, and precision machining of the runner surface. The purpose of rough machining is to quickly remove the blank allowance, which is also a strategy to reflect the efficiency of impeller machining. The purpose of semi precision machining is to make the allowance on the blade surface uniform, in preparation for the subsequent precision machining. The purpose of precision machining is to achieve good surface quality, which is closely related to the selection of cutting tools, the matching of machine speed and feed rate.
The improvement of impeller machining efficiency mainly lies in the improvement of rough machining efficiency. By using the five axis impeller rough machining mode, the five axis rough machining of the impeller can be achieved, which can achieve uniform material retention, smoother machining trajectory, and improve machining efficiency.