Nowadays, there are many manufacturers producing angular contact ball bearings in China. So, how to choose an angular contact ball bearing manufacturer? Based on 35 years of industry experience, from the following three perspectives, how should we choose an angular contact ball bearing manufacturer?
1. A good manufacturer of angular contact ball bearings requires very professional equipment, using high-precision, reliable, and highly stable CNC lathes;
For example, the most crucial and final production process in the manufacturing of bearing rings is grinding. The equipment used mainly includes special CNC grinding machines and ultra deep processing CNC lathes;
Some types of bearing throwing ring geometric structures are very simple, with low precision requirements. Some angular contact ball bearing manufacturers can choose PLC economical and practical CNC machine tools; Some categories of angular contact ball bearings have higher requirements for throwing rings, such as the raceway must be produced and processed into a "convex" majority shape. So our angular contact ball bearing manufacturers should use universal or high-end CNC machine tools to meet the requirements.
2. A good manufacturer of angular contact ball bearings has very high requirements for accuracy and consistency of accuracy;
Needle to diagonal contact ball bearings, apart from differences in raw materials and heat treatment processes, face specific challenges in terms of precision and consistency in part grinding, especially in mass production processing.
For example, P4 or more bearing rings have significant differences in production and processing accuracy. The one-time compliance rate of a good angular contact ball bearing manufacturer is generally about 80%. And the matching rate is 60%. Some types of bearings, such as cone roller bearings for wind turbine shafts, are also difficult to maintain quality above P4.
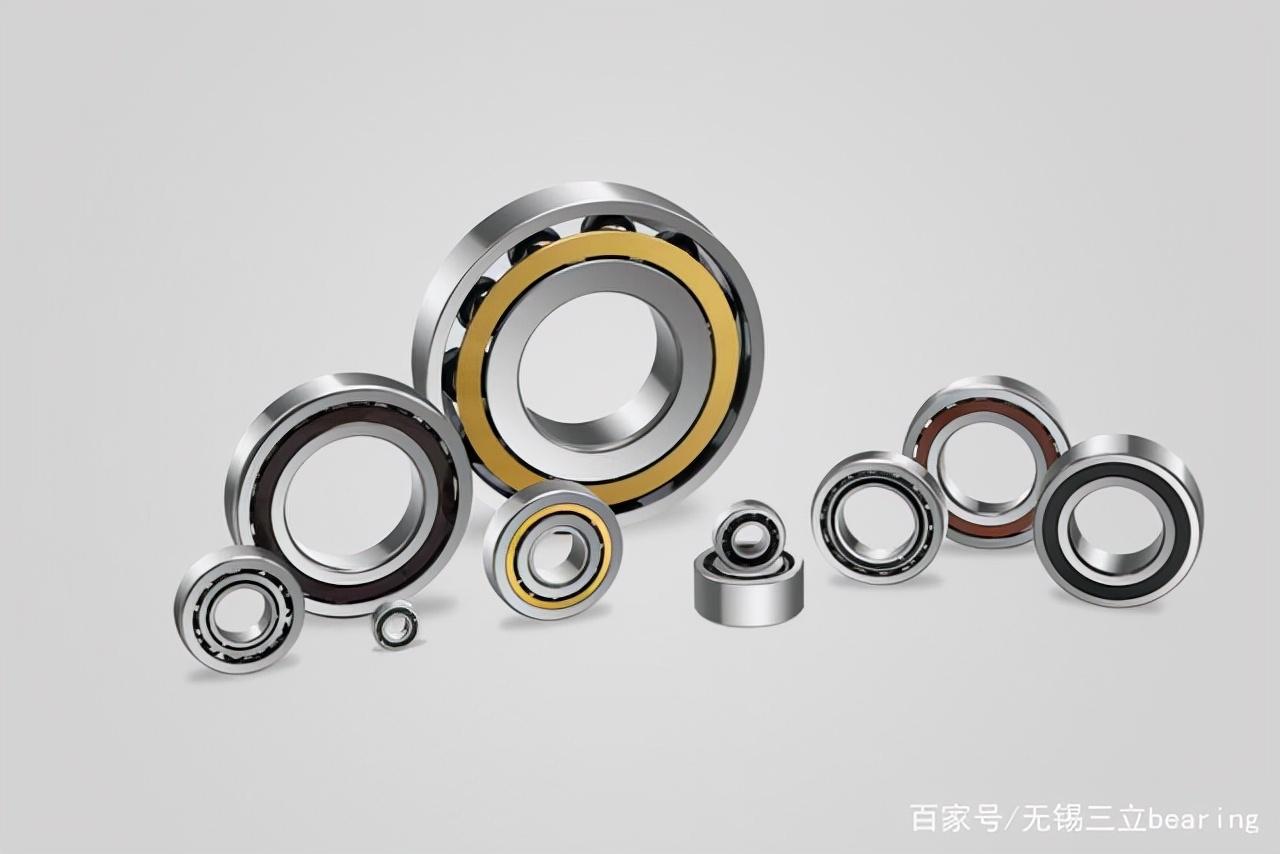
Angular contact ball bearing
3. Core technologies and strategies that a good manufacturer of angular contact ball bearings should adopt
(1) A good manufacturer of angular contact ball bearings should use CNC lathes with high precision, reliability, and high stability. For some complex bearing rings, it is necessary to use multifunctional CNC machine tools such as CNC grinders,; The inner surface grinding application uses a fast high-speed electric spindle, while the outer surface grinding application uses a high bending stiffness sound pressure sand wheel disc spindle bearing for rapid grinding;
Good angular contact ball bearing manufacturers use semi closed loop control and closed-loop control servo control systems to manipulate it, and can perform precise micro cutting and compensation. The cutting screen resolution can be imagined to be 0.25 μ m or 0.1 μ m, and the precision of repeated precise positioning can reach 1 μ m or as high as 0.5 μ m;
Good angular contact ball bearing manufacturers use high-precision and bending stiffness, as well as wear-resistant ball screws and sliding rails and other movable components;
A good manufacturer of angular contact ball bearings should use a bed that has undergone sufficient aging, is stable, and has good vibration absorption performance compared to the actual effect. High precision CNC grinding machines must use granite beds with strong vibration attenuation coefficient and relatively low linear expansion coefficient.
(2) A good manufacturer of angular contact ball bearings should actively measure and manipulate the grinding specifications with a precision of 3 μ m or higher up to 1 μ m. The communication servo motor is used to drive and operate the grinding wheel dresser, reduce the distance between sand wheel repairs, and improve the quality of sand wheel repairs; Use high-quality diamond saw blades and CBN sand wheels to ensure consistency in machining accuracy for large-scale production.
(3) A good manufacturer of angular contact ball bearings should reduce grinding capacity by forging, deep processing or high-precision cold rolling, and carry out additional quenching and cold pressing in the middle of each process flow to remove grinding stress and prevent disadvantages such as grinding burns and cracks caused by excessive cutting speed, thus improving production and processing accuracy and surface quality.
(4) Good manufacturers of angular contact ball bearings should pay attention to improving the production and manufacturing level of important components such as flip bodies and ball bearings. Especially for high-precision cylindrical rollers and conical rollers, automatic production lines should be applied. High precision rollers must be thoroughly smooth and brittle.
(5) Good manufacturers of angular contact ball bearings should pay attention to the machining process. According to strict regulations on temperature control, constant humidity, vibration reduction, and cleaning, basic construction or renovation of production and processing space environment equipment should be carried out.
(6) A good manufacturer of angular contact ball bearings should fully embody the characteristic of "grasping and inheriting" in the production and manufacturing of high-precision components, improve the technical training and practical experience accumulation of the staff, strictly organize the production process and processing technology, strengthen the quality assurance management system, and make the "mobile software" and "hardware configuration" consistent, so that excellent hardware configuration mainly demonstrates stronger efficiency.