Sheet Metal Processing involves various types, mainly including laser cutting, water jet cutting, plasma cutting and other processes used for material separation, as well as bending, punching, shearing and other processes used for material forming. In addition, there are other processing methods such as curling, ironing, and hydraulic forming. When selecting the type of processing, product requirements and material characteristics need to be considered. Welding, riveting and other processes can also be used during the processing to meet the structural and connection requirements, ensuring the quality and functionality of sheet metal parts. Here we mainly introduce three commonly used types
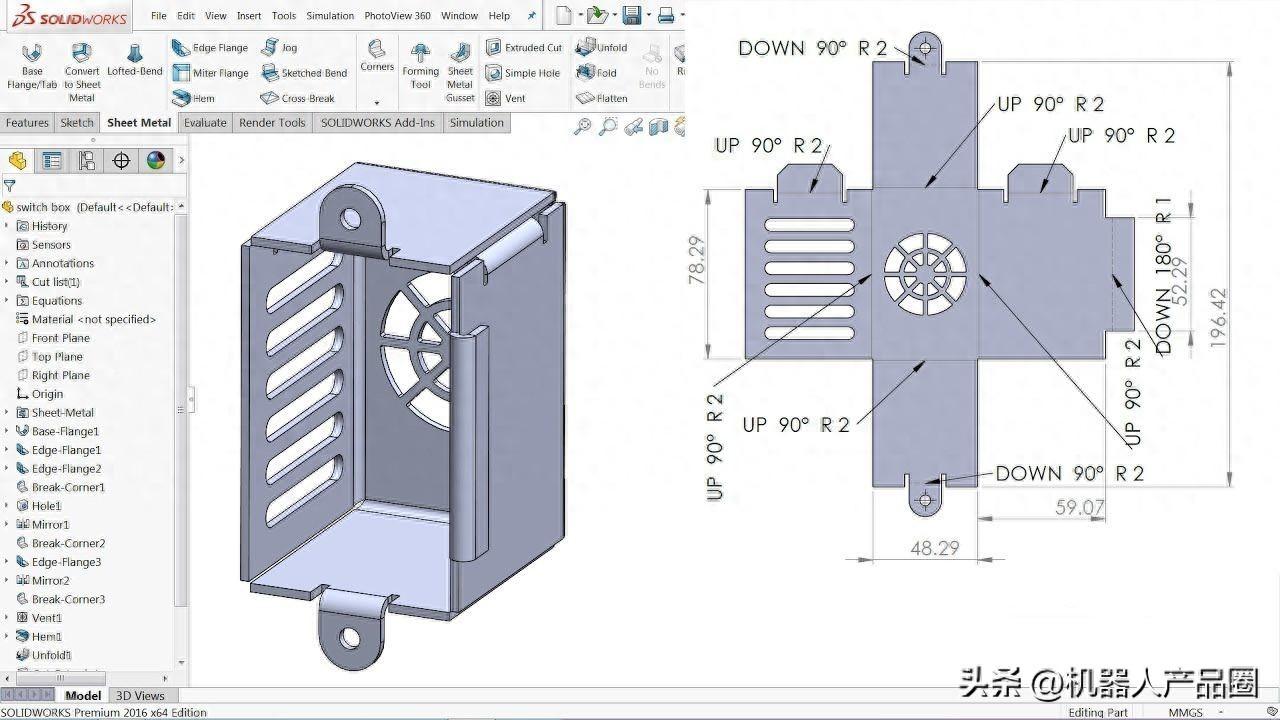
1、 Cutting
a. Cutting: Cutting operation along the straight line between two cutting edges
b. Punching: A one-step cutting operation along a closed contour to produce the required parts
c. Stamping: Cutting operation along a closed contour, where the remaining inventory is parts
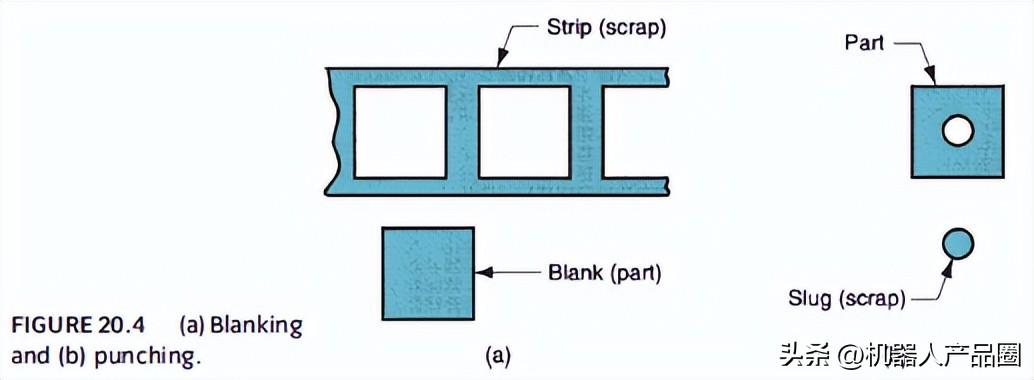
2、 Bending
The thickness of a metal sheet that undergoes plastic deformation by deforming around a straight axis remains almost unchanged or unchanged
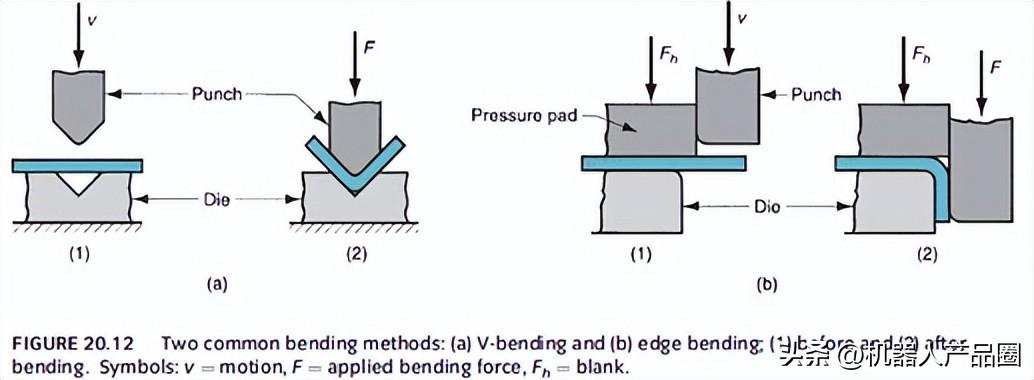
Other bending/forming operations
1. Flanging: straight, stretch, shrink
2. Curling: By multiple bending steps, the edges of the sheet are bent to increase rigidity and improve appearance
3. Seam: Similar to rolled edges, but assembled with two metal plate edges
4. Curling: Forming the edges of a part into a rolled or curled shape is done for safety, strength, and aesthetics
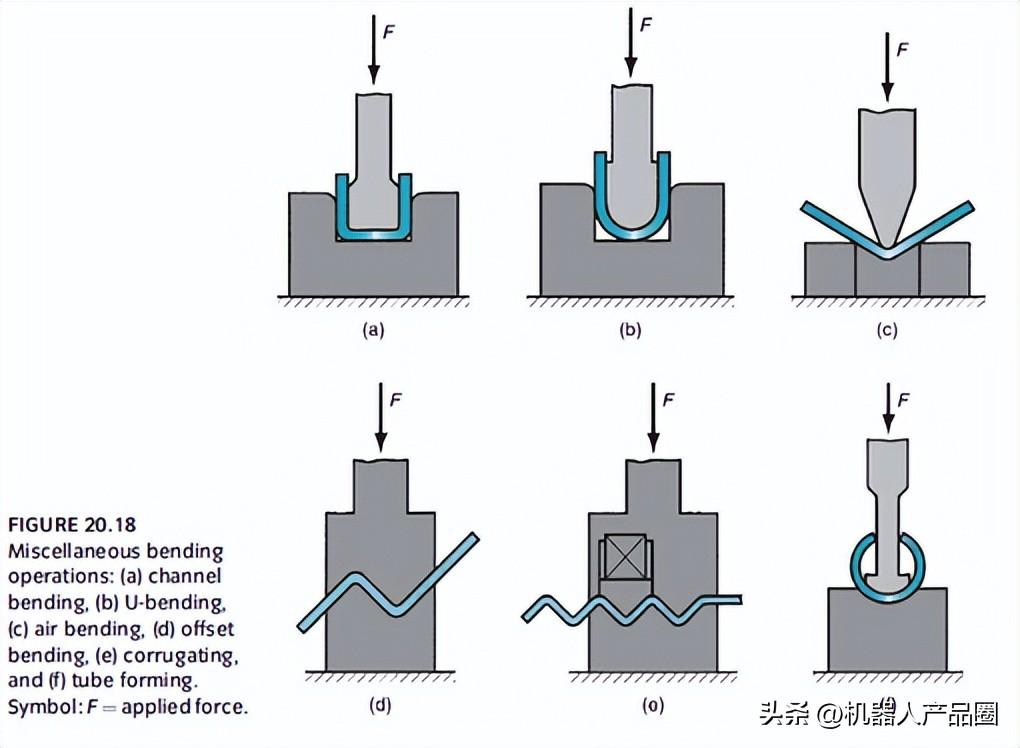
3、 Stretching
Metal sheet forming process used for manufacturing cup-shaped, box shaped, or other complex curved and concave parts, commonly used parts: beverage cans, ammunition shells, sinks, cookware, automotive body panels
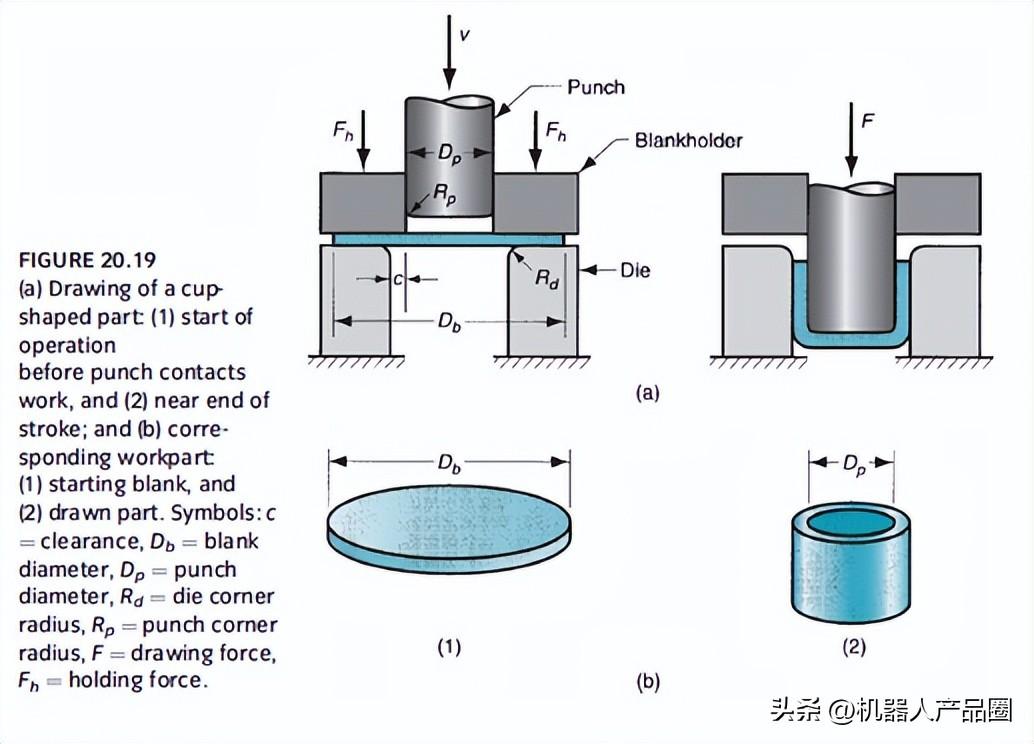
If the shape change required for part design is too severe, the complete forming of the part may require multiple stretching steps, known as additional stretching steps. The purpose of the edge pressing ring is to prevent flange wrinkling, tearing, ear and surface scratches during cup pulling