It is said that molds are the mother of industry, but what exactly is a continuous stamping mold?
In general, the so-called continuous stamping die is the process structure of combining multiple projects in the same die, threading the material belt into the die and stamping one step at a time to create a complete hardware.
Stamping Forming: Among various types of stamping molds, continuous stamping molds are most suitable for mass production due to their high production efficiency. Moreover, continuous stamping molds have a wide range of applications and can be used for various hardware parts.

The main advantages of continuous stamping molds are:
1. Producing with coil materials results in lower material utilization and saves the disadvantage of continuous feeding.
2. Engineering and structural design are more flexible.
3. One punch can produce multiple PCS, with fast production speed and high efficiency.
4. The same set of molds can produce multiple products simultaneously.
5. Easy to achieve automated production, saving a lot of manpower and material resources.
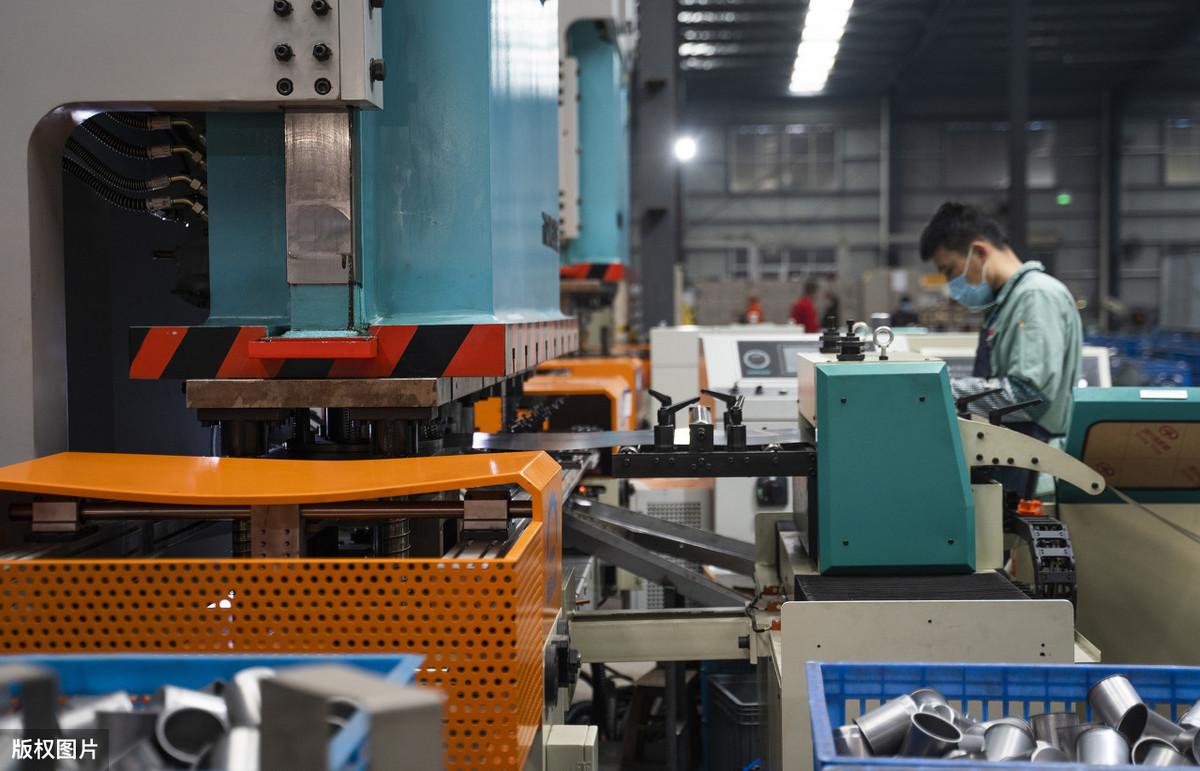
Confirmation items for the review of finished product drawings before mold design and opening:
1. Edge and rolling direction, finished product material and thickness.
2. The winding direction of the continuous strip (pay attention to whether electroplating is required).
3. Annotations must be clear, and non local languages must be translated and annotated.
4. Whether the dimensions and tolerances of the finished product drawing are fully marked.
5. What is the angle method for the view, and are the dimensions indicated in metric or imperial.
6. Does the position of the cutting edge affect the functionality or assembly of the finished product.
7. Whether the two sides of the bent part at the root of the finished product are symmetrical, asymmetry may cause deviation after bending, and must be negotiated with the customer.
8. Try to obtain product usage functions and related content from customers as much as possible.
9. When the dimensions or tolerances are unreasonable, missing or unclear, the customer must be notified in writing and requested to provide a written response, which should be fully retained for future reference.
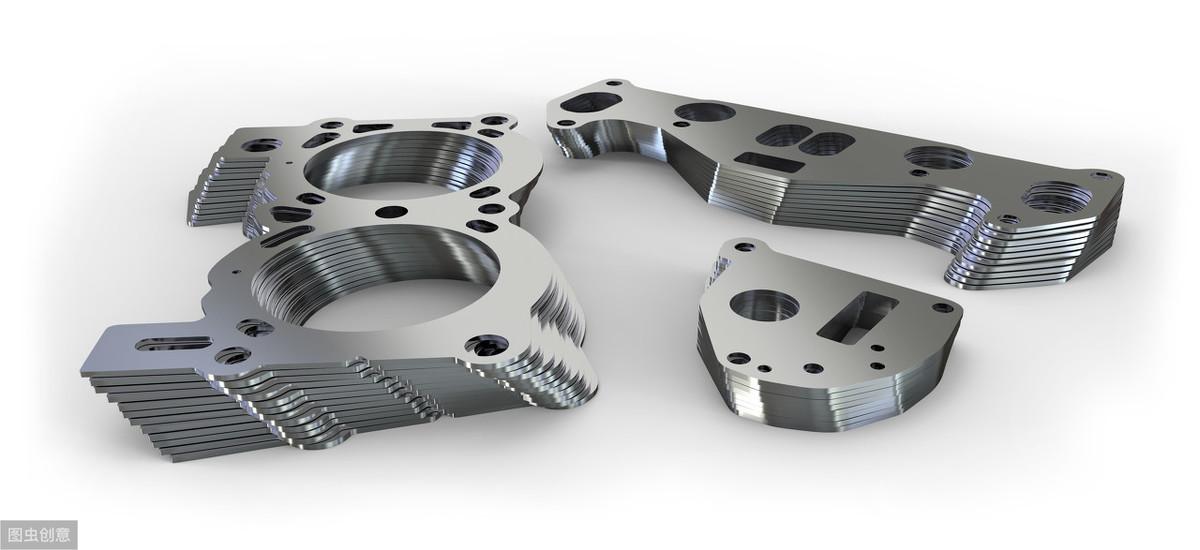
Precautions for unfolding settings:
1. The size setting should be logical, for example, the hole and contact bending height should be set with upper limits.
2. The lower limit should be set for the unfolded size of the curved shape and the root size of the folded inner diameter.
3. When there is a requirement for CPK value, the tolerance range must be multiplied when CPK is 1.33, and multiplied when CPK is 1.67
Set it later.
4. When there are electroplating requirements, the dimensional changes before and after electroplating should be considered.
5. SUS (stainless steel) O material is relatively soft, and there will be a stretching amount when bent above 80 degrees
Attention must be paid when unfolding at around 0.10-0.12.
6. When bending and forming in a zigzag shape, there will be a stretching amount, and attention must be paid when unfolding.
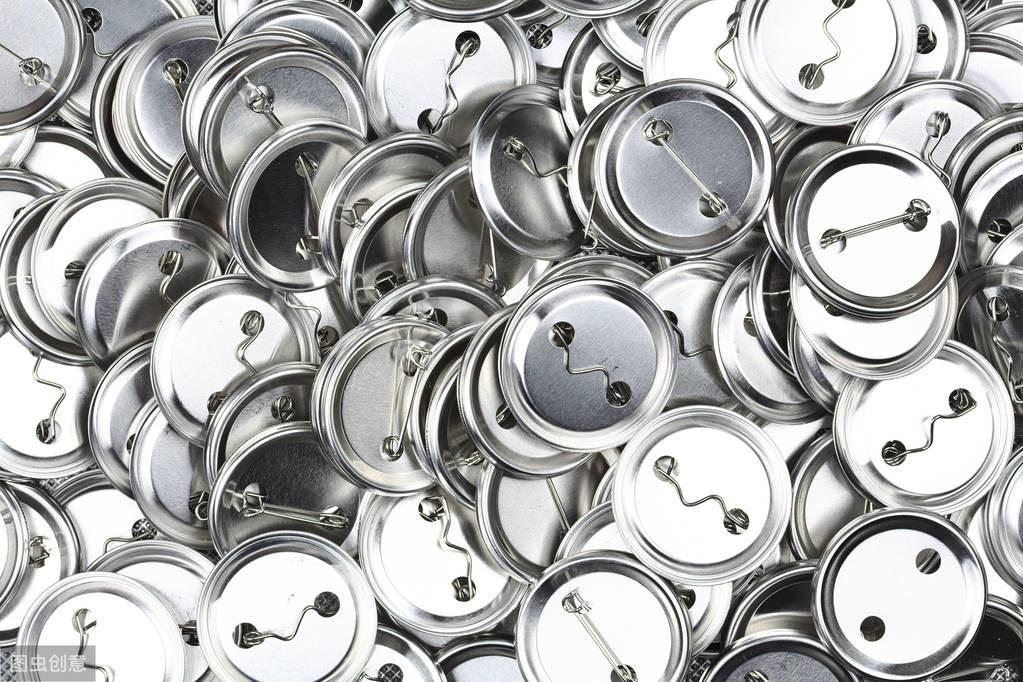
Continuous stamping die design process:
1. Finished product unfolding setting values and bending setting values.
2. Set the direction of finished product burrs and rolling direction.
3. Set the unfolded diagram (three views).
4. Set up the engineering structure diagram.
5. Discussion meeting on new mold engineering structure.
6. Disassemble parts and draw.
7. Proofreading and drawing.
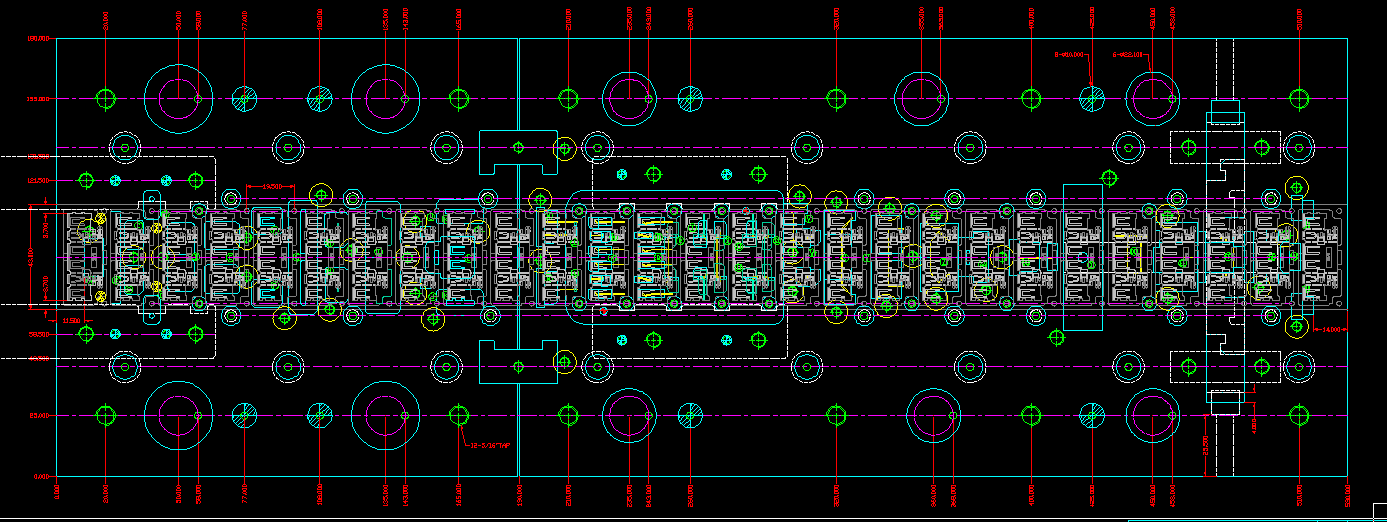
Setting of gaps between various materials:
1. The shear gap of brass (C2680) is 4% (material thickness 0.04=unilateral gap size).
2. The shear gap of phosphor copper (C5191/C5210) is 5% (material thickness 0.05=unilateral gap size).
3. The shear gap of the Western whiteboard (C7701/C7521) is 5% (material thickness 0.05=unilateral gap size).
4. The shear gap of SPCC/SPCE is 4% (material thickness 0.04=unilateral gap size).
5. The shear gap of stainless steel (SUS) is 4% (material thickness 0.04=unilateral gap size).
6. The shear gap of aluminum is 2% (material thickness 0.02=unilateral gap size).