1、 What are the techniques for creating metal logo signs with textured graphics and text
1. Thick metal panels are extruded with convex characters using concave molds and punching machines;
2. It is to use a thin metal panel with convex and concave molds and stamping to draw convex characters;
3. It is to use etching method to etch convex characters on stainless steel, aluminum plate or copper plate.
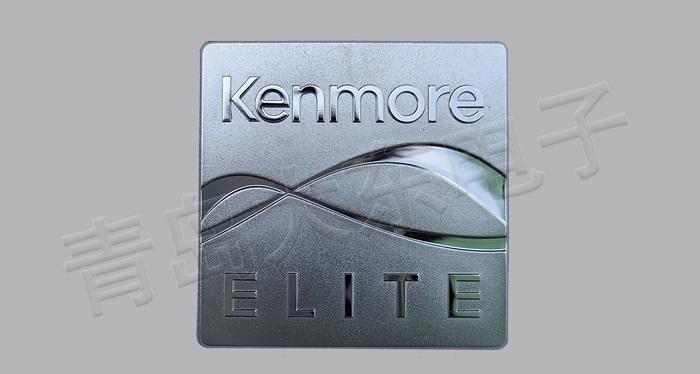
2、 Label hot stamping equipment and process:
Flat hot stamping, as the name suggests, refers to the use of a flat mold as the reference surface, which is hot stamped onto a flat workpiece or a part of the workpiece's flat surface (flat hot stamping). This type of impression can be a protruding graphic and text, hot stamped on a flat surface; It can also be a flat silicone plate, hot stamped on raised graphics and text.
The hot stamping and embossing part is a heated silicone rubber roller that can be hot rolled on a flat surface (round hot stamping) or on a curved surface (round hot stamping). If equipped with a dedicated servo mechanism, it can also be hot rolled around the edges of TV housings and other casings. There is also a type of scalding equipment. It is different from the former in that it still uses flat plate hot stamping, and the workpiece is cylindrical. When it is hot pressed, it rolls and advances while hot stamping, achieving the purpose of hot stamping on the circumferential surface, which is called "flat hot stamping circle". Before the 1980s, hot stamping equipment in China was mostly homemade by hot stamping users. In the early 1980s, most of the imported hot stamping machines were flat and rolling machines from Japan's Taiping (Navidas), West Germany's Kurz, and Hong Kong. After the 1980s, there were gradually more domestic production factories, which have now become a major category of special printing equipment, not only meeting the needs of the domestic market, but also for export.
3、 What are the oxidation processes for signs
There are methods such as rapid oxidation, electrolytic coloring, soaking and trekking printing and dyeing, low-temperature sealing, electrophoretic paint replacement for the second oxidation, and different oxidation power sources.
4、 Printing process for metal logo signs:
1. Screen printing: The text, scale, graphics, positioning holes, and colors of the screen printed label should meet the requirements of the drawing. The appearance of the metal logo label product should have no significant scratches or stains, and the adhesion of the ink film should meet the requirements;
2. Machine printing: It is metal color printing, using offset printing machines, with bright colors and excessive gradient effects, making graphics and text vivid and compelling.
5、 Precautions for baking paint on metal logo signs:
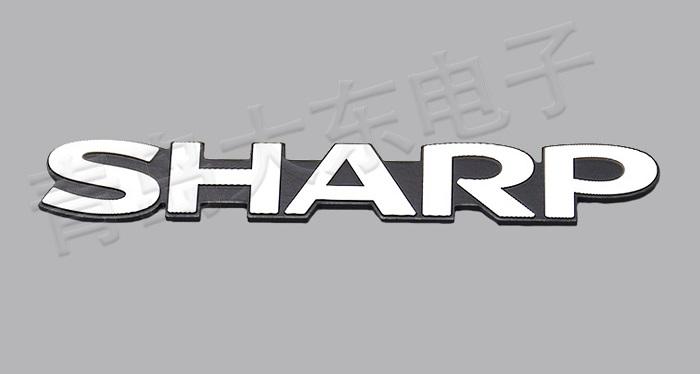
The paint baking room and environment should be clean, avoiding dust and even paint dilution, and the baking time should be controlled.
6、 The process of cutting metal logo signs and nameplates:
1. Bottom processing stamping forming high gloss cutting (deep drawing)
2. Stamping forming bottom layer treatment, high gloss cutting (cold extrusion)
3. Etching convex lettering bottom layer treatment, high gloss cutting (etching), high gloss signage
7、 There are several electroplating processes for metal logo signs:
Electroplating generally includes gold plating, silver plating, bronze plating, antique copper plating, nickel plating, sand nickel plating, and two-color gold plating.
Remind everyone to pay attention to the coating time and thickness during electroplating. If the label is too thin, it will directly affect the drawing process. The coating is easily worn off during drawing, which cannot achieve the desired effect and is prone to breakage. There are too many defective products. Control the processing time of plastic parts to avoid corrosion under bubbles in the coating.