I want to make the cold extrusion process more perfect, not just because I understand molds! The design of cold extrusion processing molds is only the first step, but of course, this step is also particularly important! If the mold structure design is unreasonable, not only will it be difficult to achieve the desired product effect, but the speed of damage to the mold punch will also be very fast. EMAR metal continuous die cold extrusion generally simulates the process from blank to finished product. If ten steps are determined to be completed (excluding cutting and edge cutting), the deformation of the simulated blank forming process in each step will not exceed 10%, and the bending R angle cannot be too large, otherwise it will seriously affect the life of the punch. If a punch in the cold extrusion processing die is damaged too quickly, the punch structure must be redesigned, otherwise it will not only affect efficiency but also profitability. After all, damaging a tungsten steel punch can cost hundreds of dollars, and repairing a continuous die also takes at least two days! Under strong extrusion pressure, the smoothness of the mold cavity has an impact on the lifespan of the mold and the flow of materials, and special attention should be paid to it. There are many techniques in the design of cold extrusion processing molds that will not be elaborated here. Now, let's talk about the issue of annealing of cold extrusion processing materials. Continuous die cold extrusion does not require annealing at every step, because basically a product is completed in 0.3 seconds from blank to finished product, and the product is almost finished without cooling during the production process. But at the beginning, the raw materials must be fired properly before production, otherwise it is common for the molds to dry out. We need experts who understand materials here, because different materials have different ways of annealing, and it is very important to achieve the best plasticity state of the material through annealing! The lubrication treatment of the third cold extrusion processing is also a crucial factor in whether the products produced by cold extrusion processing can be done well. Ordinary low-carbon steel is treated with phosphating and saponification, which has a very good effect. For nickel based alloys, another formula of oxalic acid treatment is needed. The processing methods for materials such as oxygen free copper and aluminum are quite different, with sulfurized animal oil being the best, followed by vegetable oil. Some soap and water can also be used as needed. There is a lot of knowledge here, and there are also many experts in material lubrication who are true or false. The most important thing is to have accumulated experience! In one sentence, the three key points of cold extrusion processing are: mold structure design, materials, heat treatment, materials, lubrication. You must be an expert to be able to do this job well! EMAR Hardware has been researching cold extrusion processing for decades. I would like to share my experience and insights on cold extrusion processing, hoping to be helpful to friends in the cold extrusion processing industry!
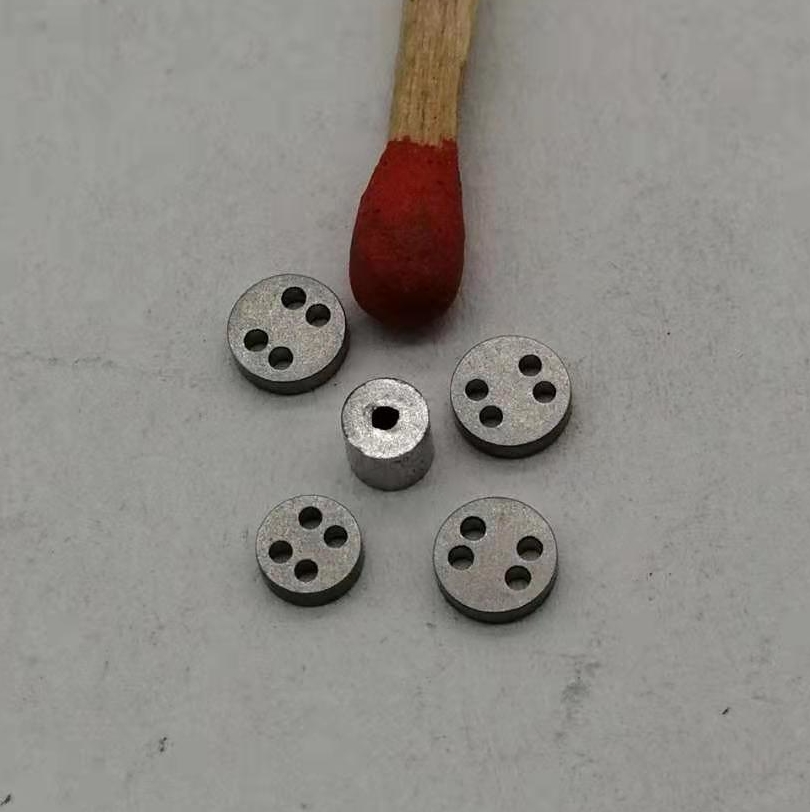