Recently, the Chinese Academy of Sciences held a press conference. It was announced at the meeting that the Xi'an Institute of Optics and Precision Machinery, Chinese Academy of Sciences, had developed a 26 watt industrial femtosecond fiber laser with the highest single pulse energy in China, developed a series of ultra fast laser extreme manufacturing equipment, achieved a breakthrough in "cold processing" of air film holes in aeroengine turbine blades, filled the domestic gap, and reached the international advanced level.
This is undoubtedly a significant breakthrough! In the aviation field, aircraft engines have always been hailed as the "pearl on the crown of modern industry", and their manufacturing level represents a country's technological, industrial, and defense strength. The engine blades are the first key component of the aircraft engine, located in the hottest, most complex, and most harsh environment of the aircraft engine. Their casting process directly determines the performance of the aircraft engine.
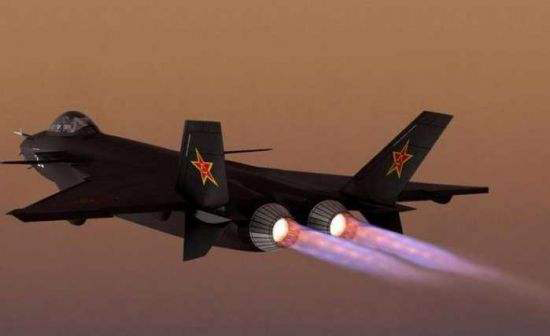
Previously, due to the significant gap in aircraft engine manufacturing technology between China and developed Western countries, the turbine blades of the engines were unable to withstand higher temperatures, resulting in a severe lack of thrust for the engines. Now. The emergence of "cold processing" ultra fast laser extreme manufacturing technology has greatly filled the gaps, strengthened the performance, lifespan, and reliability of space engines.
According to researchers from the research institute, the use of ultrafast laser microfabrication technology to drill holes on the surface of blades can effectively solve the cooling problem of aircraft engines under ultra-high temperature (1700 ℃) and ultra-high pressure conditions. Moreover, ultrafast laser microfabrication technology also breaks through the defects of recast layer, microcracks, recrystallization, etc. in the traditional manufacturing method of processing blade film holes.
Simply put, this technology is similar to laser surgery performed on myopic patients, which can focus on a spatial area thinner than hair. This ensures that the cutting surface is neat, there is no thermal diffusion, no microcracks, and does not affect the materials adjacent to the affected area during processing. This technology has become the best choice for ultra-fine and low damage in fields such as aerospace and electronics.
It is worth mentioning that this technological breakthrough is not only applicable to high-end aerospace fields, but we will also see its application in future life, such as automotive engines. According to experts, some of the core indicators of this technology have reached the international advanced level, and can provide comprehensive solutions for ultra fine and "cold processing" of many difficult to process materials and components.