How are the micro punched hardware components produced? EMAR Hardware elaborates on the production method of micro punched hardware components. I won't go into detail about how to drill holes in relatively thin micro punched hardware parts. It's relatively simple to achieve a punch hardness higher than the material hardness. How to make micro punched hardware components with a pore depth that is more than three times the pore size? Because the law of physics states that if the depth of a hole exceeds three times the aperture, it is very easy to break the punch. Many engineers just want to produce blanks and then CNC drill holes, which is possible but slow! And it's not easy to locate, maybe the holes will be punched out of center! And the smaller the hole, the easier it is for the knife to break. If encountering products with hundreds of thousands of micro punched hardware components every month, it is almost impossible to mass produce them. Is there a fast and efficient processing method for producing micro punched hardware components? The answer is yes! The working principle of the continuous die cold extrusion production method invented by EMAR Hardware is to punch the product blank with a coarse punch in the initial stage, and then shrink it to the specified pore diameter by continuous die cold extrusion. The speed of producing micro punched hardware parts in this way can reach over 160 pieces per minute, and the product tolerance can be controlled within 0.02mm, with an efficiency more than 50 times that of CNC Machining. The production method of micro punched hardware components is not a simple process, but requires long-term research and development and technical investment. Many production details need to be coordinated in order to produce high-end products, such as annealing, lubrication, punch surface treatment for different materials, etc. Almost every detail is an engineering discipline, and continuous research and development investment is necessary to find the best solution!
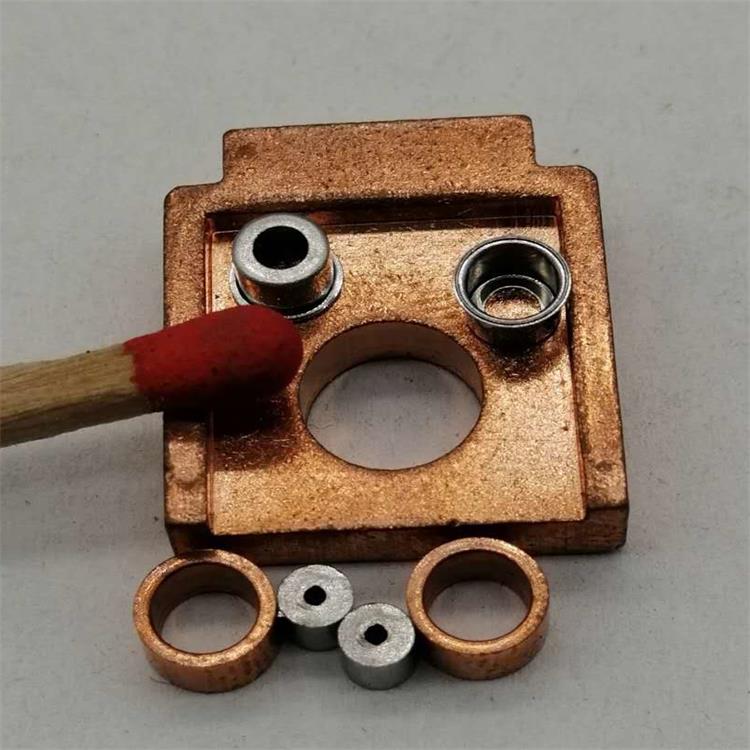
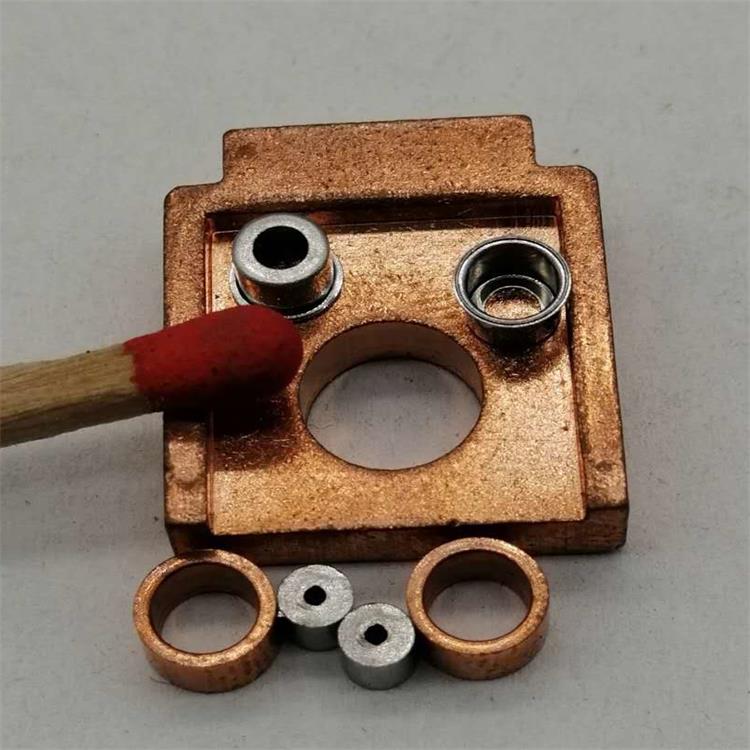