Shenzhen EMAR Precision Technology is a professional manufacturer dedicated to high-precision flange precision parts processing, providing customized and batch manufacturing of flange parts. It is one of the strong precision mechanical processing manufacturers in Shenzhen, commonly known as French flanges, also known as flange flanges or flanges. A flange is a component that connects shafts to each other and is used for connecting pipe ends; Also used for flanges on equipment imports and exports, used for connecting two devices, such as gearbox flanges. Flange connection or flange joint refers to a detachable connection in which a flange, gasket, and bolt are connected to each other as a combined sealing structure. Pipeline flange refers to the flange used for piping in pipeline installations, and when used on equipment, it refers to the inlet and outlet flanges of the equipment. There are holes on the flange, and bolts tightly connect the two flanges. Seal the flanges with gaskets. Flanges are divided into threaded connections (threaded connections), welded flanges, and clamp flanges. Many flange manufacturers overlook the three important factors of flange solution treatment. Next, EMAR Precision Technology will elaborate on the three elements of flange solution treatment, namely temperature, insulation time, and cooling speed. Let's take a look together.
1. Eliminate work hardening to facilitate continued cold working.
Through solid solution treatment, the twisted lattice is restored, the elongated and broken grains are recrystallized, the internal stress is eliminated, the tensile strength of the flange decreases, and the elongation rate increases.
2. Making the flange structure and composition uniform is particularly important for raw materials, as the rolling temperature and cooling rate of each section of hot-rolled wire rod are different, resulting in inconsistent organizational structure.
At high temperatures, atomic activity intensifies and dissolves with each other, resulting in a more uniform chemical composition. After rapid cooling, a uniform single-phase structure is obtained.
3. Restore the inherent corrosion resistance of the flange.
Due to the precipitation of carbides and lattice defects caused by cold processing, the corrosion resistance of stainless steel decreases. After solution treatment, the corrosion resistance of the flange is restored to its optimal state.
The solid solution temperature is mainly determined by the chemical composition.
Generally speaking, for grades with a wide variety and high content of alloying elements, the solution temperature should be correspondingly increased. Especially for steels with high manganese, molybdenum, nickel, and silicon content, the softening effect can only be achieved by increasing the solid solution temperature to fully dissolve them.
But for stabilized steels such as 1Cr18Ni9Ti, when the solution temperature is high, the carbides of the stabilizing elements are fully dissolved in the austenite, and during subsequent cooling, they will precipitate in the form of Cr23C6 at the grain boundaries, causing intergranular corrosion. In order to prevent the decomposition and solid solution of carbides (TiC and Nbc) of stabilizing elements, a lower limit solid solution temperature is generally used.
As the saying goes, flanges are steel that is not easily rusted. In fact, some flanges contain both rust resistance and acid resistance (corrosion resistance). The rust resistance and corrosion resistance of flanges are due to the formation of a chromium rich oxide film (passivation film) on their surface. Rust resistance and corrosion resistance are relative.
Experimental results have shown that the corrosion resistance of steel increases proportionally with the increase of chromium content in weak media such as atmosphere, water, and oxidizing media such as nitric acid When the chromium content reaches a certain percentage, the corrosion resistance of steel undergoes a sudden change, from easy rusting to less rusting, and from non corrosion resistance to corrosion resistance.
The production process is mainly divided into four types: forging, casting, cutting, and rolling. Some special industries have higher requirements for flange parts, so forging, casting, cutting, and rolling processes cannot meet the needs of users. Therefore, CNC is needed to achieve precision machining. EMAR Precision Technology is a manufacturer of flange precision parts, mainly for precision secondary machining of rough machined flange parts. Our CNC Machining center can process flange parts with a diameter of less than 850. Welcome to inquire.
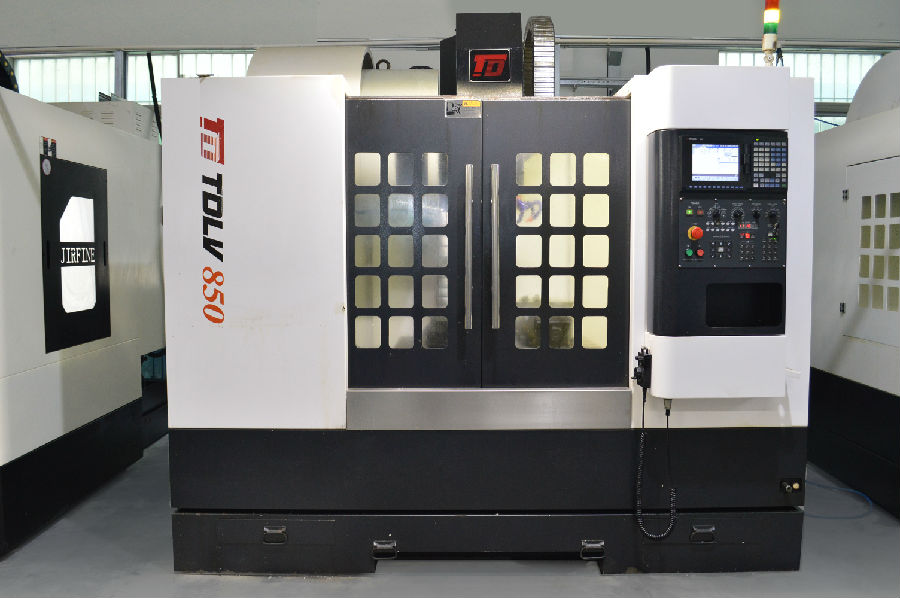