Stability is divided into process stability and production stability. Process stability refers to a process plan that produces satisfactory and qualified products with stability; Production stability refers to the ability to produce with stability during the production process. Because most of the domestic hardware stamping parts manufacturers are small and medium-sized enterprises, and a considerable number of them are still in the traditional workshop style production management stage, often neglecting the stability of molds, resulting in long mold development cycles and high production costs, severely limiting the development pace of enterprises. So, how to improve the stability of molds has become a practical problem faced by mold making enterprises and stamping parts processing plants.
The main factors affecting the stability of stamping molds and stamping processes are: the usage method of mold materials; Strength requirements for mold structural components; Stability of stamping material functionality; The shaking characteristics of material thickness; The scale of material changes; The resistance of stretching bars is extremely fine; Edge pressure changes the scale; Selection of lubricants.
As is well known, the metal materials used in stamping molds involve many varieties, and the requirements and selection criteria for their materials are also different due to the different roles played by various parts in the mold. Therefore, how to select mold materials reasonably has become one of the very important tasks in the mold design of hardware stamping parts manufacturers.
When selecting mold materials, in addition to requiring the material to have high strength, high wear resistance, and appropriate toughness, it is also necessary to fully consider the characteristics and production requirements of the processed product material in order to achieve the stability requirements of mold forming. In practical operation, mold designers tend to choose mold materials based on personal experience, which often leads to unstable mold forming due to improper material selection of mold parts in stamping.
It is worth noting that during the stamping process, each stamping sheet has its own chemical composition, mechanical function, and characteristic values closely related to stamping function. The instability of stamping material function, the fluctuation of stamping material thickness, and the change of stamping material not only directly affect the accuracy and quality of stamping processing, but also may lead to damage to the mold.
In order to address the issue of mold stability, hardware stamping manufacturers need to strictly control from the following aspects:
1. In the process planning stage, after analyzing the product and predicting potential defects that may occur during production, a stable manufacturing process plan is developed;
2. Implement standardization of production processes and production techniques;
3. Establish a database and continuously summarize and optimize it; Using CAE analysis software system, obtain the optimal processing plan.
This article is from EMAR Mold Co., Ltd. For more EMAR related information, please click on www.sjt-ic.com,
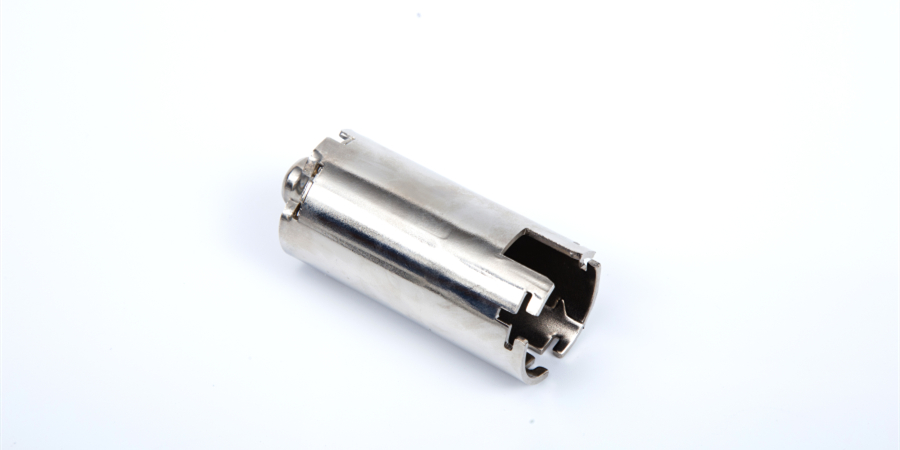