Sheet Metal Processing is a process of manufacturing various shapes and sizes of metal components by cutting, bending, stamping, and other methods on metal sheets. In the process of sheet metal processing, the selection and proportioning of materials are crucial. They not only directly affect the performance and quality of the processed products, but also affect the efficiency and cost of processing. Therefore, in order to ensure the quality and efficiency of sheet metal processing, there are some standards and techniques that need to be followed.
Firstly, the selection of materials for sheet metal processing should take into account the required physical and chemical properties. Common sheet metal materials include steel plates, aluminum plates, stainless steel plates, etc. Steel plate is one of the commonly used sheet metal processing materials, with high strength and hardness, suitable for products that require high strength and stiffness. Aluminum plates have low density and good corrosion resistance, making them suitable for products that require lighter weight and corrosion resistance. Stainless steel plates have excellent corrosion resistance and high strength, making them suitable for products such as food and medical devices that require hygiene performance. When selecting materials, the machinability of the material should also be considered, such as weldability, machinability, stamping ability, etc.
Secondly, the material selection for sheet metal processing also needs to consider the product's usage environment and requirements. Different environmental conditions have different requirements for materials, such as high temperature resistance, corrosion resistance, wear resistance, etc. When selecting materials, it is necessary to comprehensively consider factors such as temperature, humidity, and corrosiveness of the usage environment, and choose materials with corresponding properties to ensure the durability of the product in specific environments.
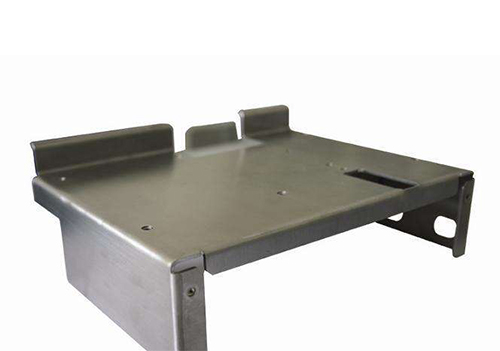
In addition, the material ratio of sheet metal processing is also an important part. Reasonable material ratio can improve product performance and yield, and reduce production costs. Generally speaking, a reasonable material ratio requires comprehensive consideration of the physical and mechanical properties, process performance, and economic performance of the material. In practical operation, adjustments can be made based on factors such as the shape, size, and requirements of the product. For example, in the bending process of sheet metal, the bending angle and radius can be controlled by adjusting parameters such as the thickness and strength of the sheet metal to meet the design requirements of the product.
When carrying out material proportioning, it is also necessary to pay attention to cost control of materials. The prices of different materials vary, and there are many factors that affect material costs, such as the origin, specifications, and processing difficulty of the materials. For some products with low requirements, ordinary materials with lower prices can be used to reduce production costs. However, for some products with high requirements, such as those that require high strength and high corrosion resistance, high-performance special materials can be used, but the cost will also increase accordingly. Therefore, in the material ratio, it is necessary to balance the performance requirements of the product and cost control in order to achieve the goal of economic rationality.
The content of the article is sourced from the internet. If you have any questions, please contact me to delete it!