In the CNC Machining industry, everyone will encounter a situation where large quantities of products are produced. In order to save costs and reduce user expenses, aluminum alloy products are molded and then precision processed. After precision processing, many profiles made of aluminum alloy require further processing, such as wire drawing, anodizing, and so on. During processing, it is also easy to cause damage, such as top injuries and scratches. How can we effectively avoid such situations from happening? Shenzhen EMAR Precision Technology, with years of experience in precision machining of aluminum profiles, has compiled and summarized some relevant methods for your reference. Let's take a look together.
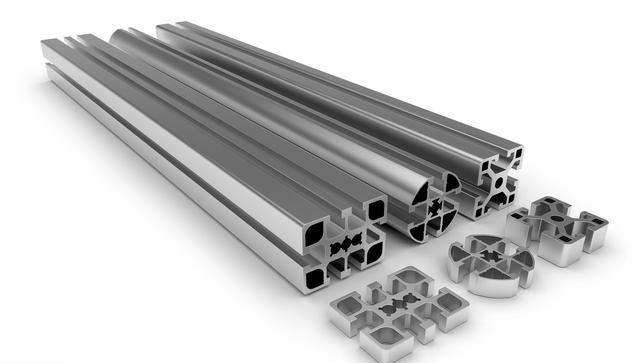
1、 The following points should be achieved during production and processing:
To ensure the quality of aluminum parts and reduce the defect rate, the first step is to implement 5S, especially cleaning. This includes ensuring that molds, workbenches, assembly lines, and packaging materials are free of sharp debris and dirt. Regular and clear cleaning is required, and molds must be cleaned and free of debris;
2. Aluminum parts are prone to heat up and accumulate together to become hard, so when cutting, it is necessary to apply some pressure wrench oil on the material (which can dissipate heat and smoothly clear the material) before processing;
3. If significant burrs are found on the product, they must be promptly sent to the mold for repair and followed up on until the results are achieved;
4. Pushing the flat mold block will produce aluminum shavings, so the aluminum shavings under the block must be cleaned every day after production;
5. For products with a large number of holes, it is necessary to clean the surface of the cutting tool or mold, ensuring that the mold, cutting tool, and product are always clean and free of debris, reducing top damage. If top damage is found, the problem point of the mold or cutting tool top damage must be identified and resolved before continuing with production;
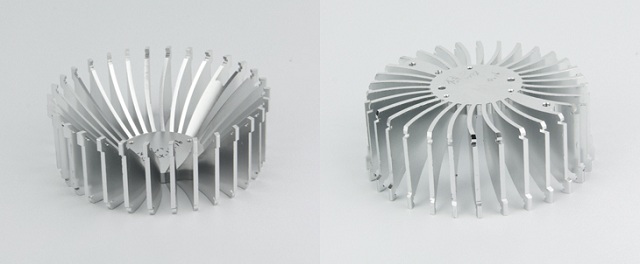
2、 Special attention should be paid to the following points in mold or tool manufacturing:
1. For products with a large number of holes to be processed, it is recommended to prioritize hole processing at the back as much as possible, even if it does not affect the number of projects;
2. When processing and bending aluminum profiles, aluminum chips are easily generated during bending, which can cause point damage and indentation. The aluminum raw material needs to be coated with PE film. In the case of rollers and electroplating, it is better to polish and coat the formed block with hard chromium;
3. Aluminum is relatively soft and the mold is prone to material blockage or tool entanglement. Therefore, when designing the gap between the mold and the tool, it is advisable to place a gap of 10% thickness on both sides of the material. A straight depth of 2MM is more suitable for the cutting edge, and a taper of 0.8-1 is appropriate;
4. Due to the brittleness of aluminum materials and their tendency to crack, especially in the case of reverse folding, it is advisable not to do wire pressing. Even if it is necessary, the wire pressing should be made wider and shallower;
5. For precision machined aluminum profiles that require anodizing, if there is a flattening or pushing process of 180 degrees, the product cannot be completely pressed together. Complete pressing will result in acid discharge, and a gap of 0.2-0.3mm should be left to allow the acid solution to flow out smoothly and in a timely manner. Therefore, a limit block must be made in this process and the mold must be calibrated to be higher than the mold;
6. All aluminum cutting edges are required to be cut with slow wire to prevent burrs and uneven material dropping. Aluminum parts are prone to high temperatures, so the hardness of the cutting tools or molds should be above 60, at least SKD11 material should be used, and there should be no inferior materials such as D2;
EMAR Precision Technology has 18 years of product experience in the field of precision processing of aluminum profiles, involving not only the processing of aluminum alloy profiles, but also various materials such as copper, stainless steel, carbon steel, plate, pipe, and bar. The company has introduced more than 100 advanced precision CNC machining equipment to support incoming material processing and product design and development services, serving users with complete product solutions, and has successfully passed multiple quality management certifications such as ISO9001, ISO14001, IATF16949, making it your first choice for precision processing needs.