Nowadays, the use of sheet metal is very common, as it is thin steel and therefore lighter in quality. Sheet metal is processed by cold working technology, so its compressive strength is relatively high and a bit hard. In addition, sheet metal belongs to stainless steel plate, which can pass current and has good conductivity. And compared with other stainless steel sheet processing methods, it has a very good cost-effectiveness. In the future, let's introduce the main uses of sheet metal products. Shenyang Sheet Metal Processing has a widespread application. Sheet metal processing is used to produce high-quality electronic and electrical components, boost the communication industry, and manufacture automotive shells and integral bodies for vehicle manufacturing processes. In addition, it is also used for the production and manufacturing of medical machinery. In summary, sheet metal processing has a very common application, bringing us a lot of convenience in production, manufacturing, and daily life.
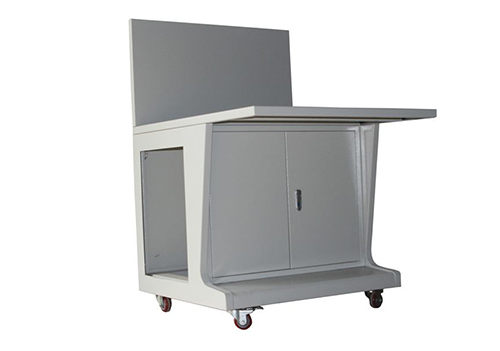
In the process of sheet metal processing, a lot of heat is generated, just like fiber laser cutting, which uses continuous high temperature to achieve the processing goal. Therefore, in this process, attention should be paid to the problem of metal material edge burning. This type of sheet metal processing method can process holes in 1/6 thick steel plates. Single pulse laser cutting conditions with low frequency and high output power can reduce heat output and improve laser cutting conditions. Setting the conditions as pulsed laser, high-efficiency energy compression strength, and high-frequency output can effectively reduce the deposition of molten metal material on the material surface during hole breaking, and reasonably suppress the sensible heat output, thereby solving difficulties.
Overheating can also occur in the processing of thick metal sheets. In this type of processing, the auxiliary vapor used is N2, which is not easily burned during segmentation. However, due to the relatively high temperature environment inside the small circular hole, the internal structure often experiences slag accumulation. The solution is to increase the working pressure of the assisting vapor and set the conditions to high peak output and low-frequency pulse conditions. When using auxiliary vapor in the air, it is not easy to ignite, just like when using N2, but slag will appear at the bottom. It is necessary to set the conditions as high assist air pressure, high peak output, and low-frequency pulse conditions to achieve better solution results.
The content of the article is sourced from the internet. If you have any questions, please contact me to delete it!