Common problems and solutions in Sheet Metal Processing bending process:
1、 The bottom of the concave part is uneven.
Possible reasons: The board is inherently uneven; There is no top material device installed inside the concave mold; The contact area between the board and the top plate is too small or the top material force is insufficient. Solution: Leveling and regulating the board; Install the top material device and adjust the size of the top material force; Add integer process.
2、 The width direction of the bent part changes, presenting an arc or bow angle.
Possible reasons include: during the stretching process, the width direction of the plate is stretched and contracted differently, resulting in changes in curvature and rotation angle. Solution: Increase the pressure of the bending equipment on the plate; Add corrective techniques; Pay attention in advance to ensure that the pattern of the board is consistent with the direction of bending.
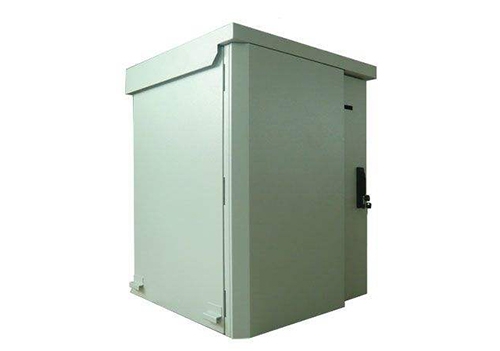
3、 Cracks occur in the curved area.
Possible reasons: The grain direction and bending direction of the board do not intersect; The inner radius of the bend is too small; The side with burrs faces outward; The plasticity of the selected board is too poor. Solution: Adjust the cutting arrangement method; Adjust the bending radius of the mold to a larger size; Change the position of burrs on the rounded corners inside the board; Use materials with strong plasticity or employ annealing processes.
4、 Bending causes deformation of the hole.
Solution: Increase the pressure on the top material plate; Usage type bending; Add grid patterns on the surface of the board to increase friction and prevent displacement during the bending process.
The above is the relevant content on common problems and solutions in the process of sheet metal processing and bending technology. We hope it can be helpful to you.
The content of the article is sourced from the internet. If you have any questions, please contact me to delete it!