Many industries require Sheet Metal Processing operations, which involve various processes such as punching and material bending. During these processing procedures, operators must pay attention to whether the parameters are accurate and whether the application methods meet the standard requirements. Currently, the workplace also attaches great importance to the quality of material processing. Therefore, in the process of performing this processing operation, attention should also be paid to the application of technical skills and knowledge, in order to meet the development needs of the industry. Below is a brief introduction to the precautions for this processing work.
When performing sheet metal processing on materials, attention should be paid to minimizing energy consumption as much as possible. Although reducing the amount of material input does not have a significant impact on cost recovery for a single operation task, for long-term large processing volumes, if shortening input and loss can be the main goal, it can reduce more expenses for manufacturers and bring more economic benefits to them.
During sheet metal processing, in order to achieve the goal of reducing investment, staff need to strictly follow production standards to complete the workflow. Before each processing, the application of materials needs to be reviewed first. Without approval, processing cannot be carried out arbitrarily. Many processing industries generate waste because the materials are not determined before processing. Therefore, staff must first clarify the type of processing materials and check the specifications and models of the materials. Making good preparations in the early stage can avoid errors during processing and reduce the amount of waste. Staff should pay attention to these issues when processing.
To avoid injury caused by broken chips, a clear baffle should be installed in the appropriate position.
When using gauze to polish the surface of the workpiece, the cutting tool should be moved to a safe position and care should be taken not to let hands and clothing touch the surface of the workpiece. When grinding the inner hole, do not use fingers to support the gauze. Instead, use a wooden stick instead, and do not drive too fast.
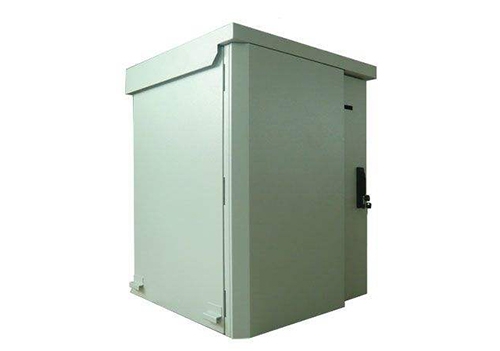
3. Stop placing objects, fixtures, or workpieces on the lathe bed and spindle gearbox. When doing homework, one should gather their thoughts. Stop tired operations, chat operations, group operations, drunk operations, and smoking operations.
4. Adhere to the cleanliness of machine tools, things, and work areas, and do a good job of handover. When cleaning the work site after work, the power should be turned off and various knife handles should be placed in a safe place.
When turning irregularly shaped workpieces, a balance block should be installed and the cutting should be carried out after trial turning and balancing.
6. The tool clamping should be reliable, and the protruding part of the tool head should not exceed 1.5 times the height of the tool body. The shape and scale of the gasket under the tool should be consistent with the shape and scale of the tool body, and the gasket should be as few and flat as possible.
7. Except for measuring tools installed on the lathe that can automatically measure during operation, the lathe should be parked and the tool holder should be moved to a safe position before measuring the workpiece.
8. The strip-shaped chips and spiral shaped long chips generated during cutting should be promptly eliminated using hooks and stopped from being pulled by hand.
9. Before starting work, put on work clothes, tie up the cuffs, wear protective goggles, and female workers should wear work hats, which should be distributed inside the hair care hat. It is forbidden to operate with gloves.
10. When loading and unloading the chuck on the lathe spindle, it must be done after stopping the machine, and the chuck cannot be removed using the force of the electric motor.
11. It is recommended to use protective covers for the protruding parts of the chuck, dial, and chicken heart clamp that hold the workpiece to avoid twisting clothes and other parts of the body. If there is no protective cover, attention should be paid to maintaining a certain interval during operation.
12. When clamping workpieces with a tip, it is important to ensure that the center of the tip is completely aligned with the center hole of the spindle. Damaged or skewed tips should not be used. Before use, the tip and center hole should be wiped clean, and the tip of the tailstock should be firmly pressed.
When turning slender workpieces, in order to ensure operational safety and machining quality, a follower or center frame should be used. For machining parts beyond the size of the lathe, mobile protective covers and safety signs should be installed.
The content of the article is sourced from the internet. If you have any questions, please contact me to delete it!