The processing of optical communication components requires very strict dimensional accuracy to ensure that the components can be assembled correctly and meet the high-performance requirements of optical communication systems. Specifically, these requirements can be summarized as follows: 1. Processing accuracy at the micrometer or even nanometer level. The dimensional accuracy of optical communication components usually needs to reach the micrometer or even nanometer level. This high-precision requirement is to ensure that the components can be accurately aligned, connected, and transmit optical signals in the optical communication system. For example, the aperture of fiber optic connectors may only be a few micrometers, and the requirements for their processing accuracy are higher to ensure efficient and lossless transmission of optical signals. In order to achieve such high processing accuracy, high-precision measuring equipment is required for inspection during the processing of optical communication parts. These devices are capable of accurately measuring parameters such as size, shape, and position of parts, ensuring that they meet design requirements. Common high-precision measuring equipment includes coordinate measuring machines, laser interferometers, etc. 3、 Numerical control programming and precise control of numerical control machine tools are key to achieving high-precision machining in the processing of optical communication parts. Numerical control programming requires determining the optimal machining path, cutting parameters, etc. based on the shape, size, material, and other characteristics of the parts to ensure machining accuracy. Numerical control machine tools achieve precise control of the machining process through high-precision servo and control systems, ensuring that the dimensional accuracy of the parts meets the design requirements. 4、 The selection and evaluation of cutting tools directly affect the machining accuracy in terms of their quality and performance. In the processing of optical communication components, it is necessary to choose suitable cutting tools and comprehensively consider factors such as the material, shape, and size of the components. At the same time, it is necessary to carefully evaluate the tool life to prevent a decrease in machining accuracy caused by rapid tool wear. 5、 Strict control during the machining process requires strict control of various factors such as cutting force, cutting temperature, machine tool vibration, etc., to avoid their impact on machining accuracy. In addition, it is necessary to strictly monitor and inspect each link in the machining process to ensure that the dimensional accuracy of the parts meets the design requirements. 6、 The case supports the use of fiber optic connector molds as an example, which require drilling micro holes with a diameter of only 0.12mm and a tolerance requirement of 0.005mm. This high-precision machining requires the use of high-precision machining equipment such as high-frequency milling, and is achieved through precise CNC programming and machine tool control.
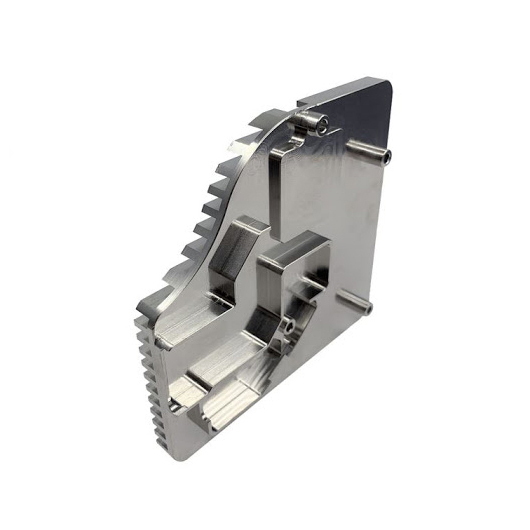