Numerical control milling is a precision machining method controlled by computers, mainly used for processing materials such as metals, plastics, and wood. The process and technology of CNC milling involve multiple aspects of knowledge, including CNC programming, operation and maintenance of CNC milling machines, tool selection, and cutting parameters. The following will provide a detailed introduction to the process and technology of CNC milling.
1. Numerical Control Programming
The CNC program is the core of CNC milling, consisting of a series of instructions used to control the CNC milling machine for machining operations. Writing CNC programs requires mastery of CNC programming languages such as G code, M code, etc., as well as knowledge of the shape, size, and surface requirements of the processed workpiece. When writing numerical control programs, it is necessary to consider parameters such as tool path, cutting depth, and feed rate to achieve efficient and accurate machining.
2. Operation and maintenance of CNC milling machines
A CNC milling machine is a device used for CNC milling processing. Operators need to understand the structure and principles of CNC milling machines and master their operating methods. When operating a CNC milling machine, it is necessary to set the machining parameters to ensure machining quality and efficiency. In addition, regular maintenance and upkeep of CNC milling machines are also very important, which can extend the service life of the equipment and ensure normal production.
3. Tool selection and cutting parameters
Cutting tools are one of the key factors in CNC milling, and the selection of cutting tools directly affects machining efficiency and quality. Choose the appropriate tool type and material based on the hardness, viscosity, and surface requirements of the processing material. At the same time, the cutting parameters of the tool, such as feed rate, rotational speed, cutting depth, etc., also need to be adjusted according to specific situations to ensure the service life and machining quality of the tool during the machining process.
4. Optimization of processing technology
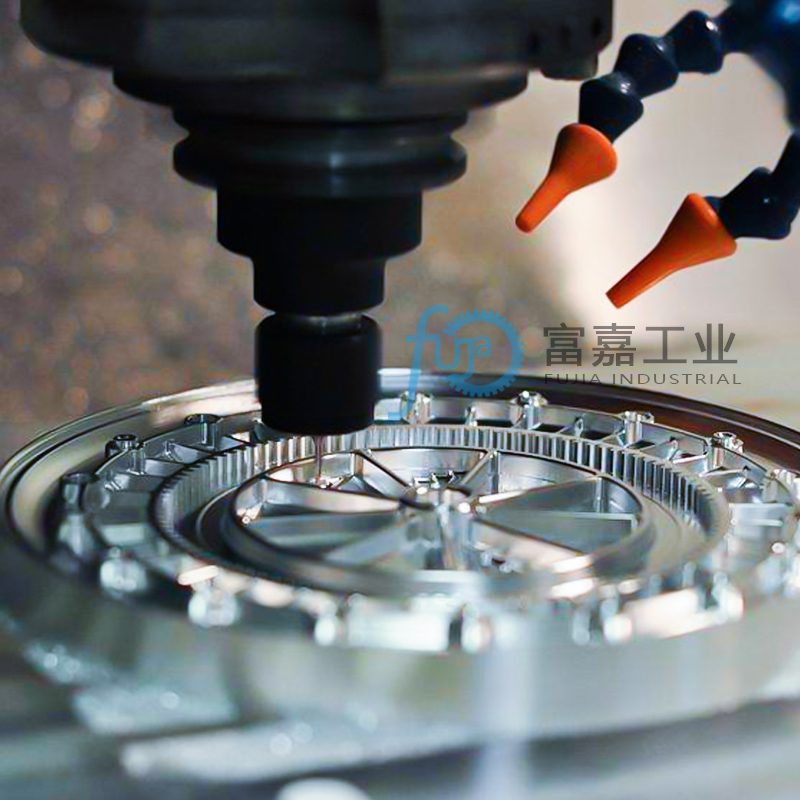
For the processing of complex components, it is necessary to optimize the processing technology to improve processing efficiency and reduce costs. By optimizing the machining path, selecting appropriate cutting tools and cutting parameters, machining time and tool wear can be reduced, and machining accuracy and surface quality can be improved. At the same time, the processing technology can be optimized through methods such as process simulation and experimental verification to ensure the stability and consistency of the processing process.
5. Quality control and testing
In the process of CNC milling, it is necessary to control and inspect the quality of the machined parts to ensure that the dimensional accuracy and surface quality of the parts meet the requirements. Processing parts can be inspected using equipment such as coordinate measuring machines and optical microscopes to promptly detect and correct problems during processing, thereby improving the reliability and stability of the parts. In addition, a comprehensive quality management system can be established to monitor various indicators during the processing and achieve an increase in the qualified product rate.
In summary, the process and technology of CNC milling involve aspects such as CNC programming, operation and maintenance of CNC milling machines, tool selection and cutting parameters, optimization of machining processes, and quality control and testing. Only by considering these factors comprehensively can efficient and precise CNC milling be achieved to meet the processing needs of different fields. I hope the above content is helpful to you.