Shenyang Sheet Metal Processing Method
1. Cutting:
Cutting is the process of unfolding and cutting materials into the desired shape. There are many cutting methods, which can be divided into shearing, punching, and laser cutting according to the type and working principle of the machine tool.
1.1 Cutting - Use a cutting machine to cut the desired shape. The accuracy can reach 0.2mm, mainly used for cutting strips or cutting clean materials.
1.2 Punching and cutting - Use a CNC machine or a regular punch press to cut the material. Both cutting methods can achieve an accuracy of 0.1mm, but the former may have knife marks during cutting, resulting in relatively lower efficiency, while the latter is more efficient but has higher single cost, making it suitable for large-scale production.
1.3 Laser cutting - Laser cutting equipment is used for continuous cutting of sheets to achieve the desired shape of the material. Its characteristics are high precision, very complex shape, but relatively high processing cost.
Sheet metal processing technology
According to the different sheet metal structures, the process flow can vary, but overall it does not exceed the following points.
1. Cutting: There are many cutting methods, mainly including the following
① Scissor bed: It is a simple material mainly used for mold cutting and forming, with low cost and accuracy of 0.2, but can only process strip or block materials without holes or corners.
② Punch press: Using a punch press to unfold parts on a plate in one or more steps, cutting the plate into various shapes of material parts. Its advantages are short time consumption, high efficiency, high accuracy, and low cost. Suitable for large-scale production, but molds should be designed.
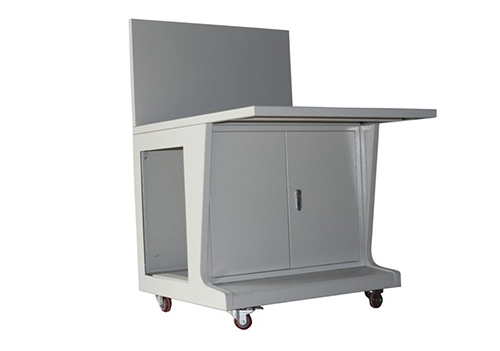
③ NC CNC cutting. When NC cutting, the first step is to write the CNC Machining project. Using programming software, the drawn unfolded diagram is written into a program recognizable by the NC numerical drawing machine, allowing it to gradually cut various shapes of flat plates on the flat plate according to these programs. However, its structure is affected by the tool structure, resulting in low cost and high accuracy of 0.15.
④ Laser cutting is the process of cutting the structural shape of a large flat plate through laser cutting. NC laser programs also need to be written, which can cut various complex shapes of flat plates with high cost and accuracy of 0.1
⑤ Sawing machine: mainly uses aluminum profiles, square tubes, drawing tubes, round bars, etc., with low cost and low precision.
The countersunk angle is generally 120 ℃, used for pulling rivets, and 90 ℃ is used for countersunk screws and tapping English bottom holes.
2. Flip: also known as hole drawing or flipping, it is to enter a slightly larger hole on a smaller base hole and then tap it. It mainly uses sheet metal processing with thinner plate thickness to increase its strength and thread ring, avoiding sliding teeth. It is generally used for thin plate thickness, normal shallow flipping around the hole, and basically no change in thickness. When the thickness is allowed to be reduced by 30-40%, a height of 40-60% higher than the normal flanging height can be obtained. When the thickness is reduced by 50%, a larger flanging height can be obtained. When the plate thickness is larger, such as 2.0, 2.5, etc., it can be directly tapped.
3. Punch press: Using mold forming processing technology, general punch press processing includes punching, corner cutting, material dropping, convex bag (convex point), punching tearing, hole drawing, forming and other processing methods. The processing requires corresponding molds to complete punching and material dropping molds, convex bag molds, tearing molds, hole drawing molds, forming molds, etc. The main attention should be paid to the position and direction.
4. Riveting: As far as the company is concerned, riveting mainly includes riveting nuts, screws, loosening, etc., which are operated by hydraulic riveting machines or punching machines to rivet to sheet metal parts, and there is a riveting method, and attention should be paid to the direction.
The content of the article is sourced from the internet. If you have any questions, please contact me to delete it!