Sheet metal is a comprehensive cold working process for metal sheets, including cutting, punching/cutting/composite, folding, welding, riveting, splicing, forming (such as automotive body), etc. Its prominent feature is that the thickness of the same component is consistent.
What is Shenyang Sheet Metal Processing?
Sheet metal is generally made by manually or die stamping some metal sheets to produce plastic deformation, forming the desired shape and size, and can be further welded or processed with a small amount of mechanical processing to form more complex parts. Sheet metal processing is called sheet metal processing, and the main processes include cutting, bending, shaping, welding, riveting, etc., which require a certain amount of geometric knowledge. Sheet metal parts are thin metal parts that can be processed through stamping, bending, stretching, and other methods. For example, the outer iron shell of a car is a sheet metal part.
Common problems in sheet metal processing and stamping parts processing?
Burr: During the punching or edge cutting process, incomplete excess material is left, and burrs are generated at the lower part of the steel plate section. Based on the section, when the height of the burrs is 0.2mm or more, the iron powder generated will damage the mold and produce protrusions and depressions.
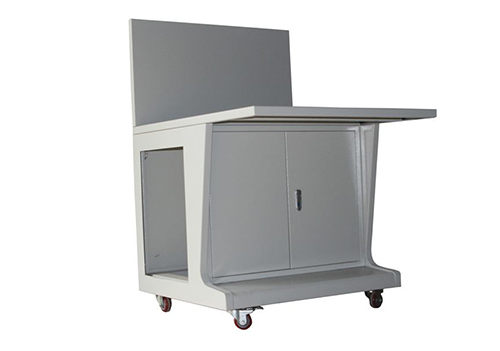
Convex concave: Abnormal protrusion or depression on the surface of the material, caused by the mixing of foreign objects (iron filings, dust) in the unwinding line.
Roller printing: caused by foreign objects adhering to the cleaning or feeding rollers (occurring at a fixed pitch), in general, the roller printing foreign objects on the sheet can be removed.
Sliding print: It occurs when the roller slides and suddenly stops or accelerates.
Roll crushing and edge wrinkling: The wrinkling scene caused by the small gap between the guide rollers on the unwinding line or the guide rollers on the mold, due to the feeding of the roll into the non yielding balance.
Scratches: The main reason for scratches on parts is sharp scratches on the mold or metal dust falling into the mold. Preventive measures include grinding the scratches on the mold and removing metal dust.
Bottom cracking: The main reason for the bottom cracking of parts is poor plasticity of the material or excessive compression of the mold edge ring. Preventive measures include replacing the material with better plasticity or loosening the edge ring.
Wrinkles on the side wall: The main reason for wrinkles on the side wall of parts is insufficient material thickness or deviation during the installation of upper and lower molds, resulting in a large gap on one side and a small gap on the other side. Preventive measures include timely replacement of materials and readjustment of molds.
The content of the article is sourced from the internet. If you have any questions, please contact me to delete it!