After the CNC parts are processed, a series of processing work needs to be done to ensure the quality, performance, and service life of the parts. These processing tasks can be summarized into the following aspects: 1. Cleaning of machine tools and environment, removal of waste materials, and cleaning of machine tools: After CNC parts are processed, the waste materials on the machine tool should be removed first, and the machine tool should be cleaned to maintain the cleanliness of the machine tool and its internal environment. Pay special attention to checking the oil wiping plate on the machine tool guide rail, and replace it promptly if it is damaged. Cleaning the environment around the machine tool: In addition to the machine tool itself, it is also necessary to clean the environment around the machine tool to maintain the cleanliness of the entire work area. 2、 Maintenance and upkeep of machine tools: Check the lubricating oil and condensate: After CNC parts are processed, check the condition of the lubricating oil and condensate, add them in a timely manner, and ensure that the lubricating oil and condensate are sufficient. Turn off power: Turn off the power and main power on the control panel to ensure that the machine is in a safe state. Storage of cutting tools and fixtures: Machine tool spare parts, cutting tools, and fixtures should be properly stored and kept in good condition. For abandoned or damaged items, they should be replenished in a timely manner. 3、 Verification and Adjustment of Tools and Workpieces: After the entire batch of workpieces is processed, the tool number, tool compensation value, and other information should be checked to ensure that the tool information on the program offset information page, adjustment card, and process card is completely consistent. When selecting tools for repeated use, they should be re aligned on the tool setter to reduce the impact of tool material wear on the processed workpiece. Remove the fixture: Remove the fixture and record its installation position and orientation for future use. 4、 Heat treatment and surface treatment of parts: Depending on the material and performance requirements of the parts, heat treatment may be necessary. The heat treatment process generally includes three processes: heating, insulation, and cooling (sometimes only two processes are heating and cooling). By controlling parameters such as heating temperature, insulation time, and cooling rate, the purpose of improving part performance is achieved. Surface treatment: In order to enhance the appearance, strength, and conductivity of the parts, surface treatment may be necessary. Common surface treatment methods include anodizing, powder coating, and pearl sandblasting. These methods can be selected based on the specific requirements and environmental conditions of the parts. 5、 Quality inspection and record quality inspection: Conduct quality inspection on the processed parts to ensure that their dimensional accuracy, surface roughness, etc. meet the design requirements. Record and archive: Record and archive relevant information during the machining process, such as tool usage, machine status, machining parameters, etc., for subsequent traceability and analysis.
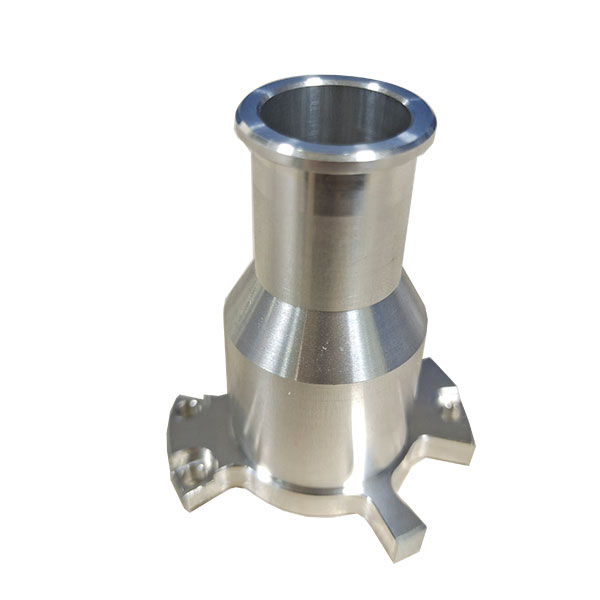