Analysis of Sheet Metal Processing, Assembly, and Welding Processes
Sheet metal processing is very common in the production of the mechanical industry and is an important component of mechanical production. It has a wide range of applications in fields such as automotive and aerospace. It directly determines the appearance of the machine and reflects its maturity. With the rapid development of the mechanical manufacturing industry, the shape of sheet metal parts has become increasingly complex. The calculation, bending, welding, spraying and other processing processes in the development of metal materials directly determine whether sheet metal parts can have good appearance, sufficient strength and necessary accuracy. Therefore, accurately calculating its unfolded size has become the primary task in sheet metal design, and sheet metal bending is a very important process in sheet metal processing. The quality of bending process directly affects the size and appearance of parts, especially the quality of subsequent assembly and welding processes. This article analyzes the sheet metal unfolding calculation, bending process, welding, spraying and other processes from the perspective of technology, combined with the actual production process, and proposes solutions to the problems.
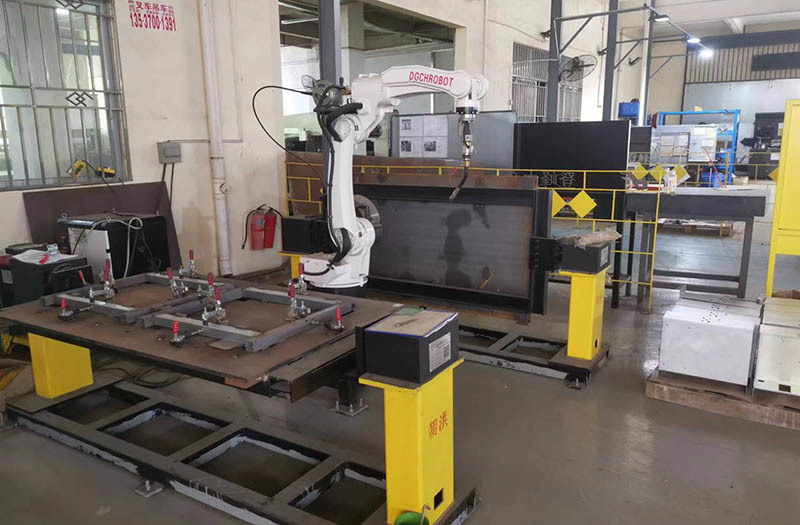
Before starting the bending work, it is necessary to accurately calculate the dimensions of each part after unfolding, as well as the position of its slots or holes on the drawing. This is to solve the problem of the difference between the hole position and the overall size caused by laser cutting exceeding the tolerance. The external material will elongate under the bending moment of the internal metal plate, but the length of the neutral layer will not change between tension and compression. Therefore, generally speaking, calculating the unfolded length of sheet metal parts is equivalent to calculating the length of the neutral layer. The actual length of sheet metal components is the sum of their straight length and neutral layer length. The length of the characteristic layer is closely related to the type, thickness, and mold of the material used. However, in actual processing, due to the fact that the mold and bending radius of sheet metal parts are the same, the calculation of bending radius is a simple algorithm without special requirements, and the actual size of bending radius is basically ignored. Below is 90. Simplified calculation method for curved parts. The simple calculation formula is as follows: L=d1+d2-a
Among them, L is the unfolded length, and d1 and d2 are 90. When bending, the two right angled edges of the part are its overall size, and a is its bending compensation value. This algorithm is suitable for most sheet metal bending parts in sheet metal processing, especially when the bending radius is between 0.5mm and 2mm and the sheet thickness is less than 2.5mm, the calculation is very convenient.
However, in actual production and life, in most cases, the bending compensation value of sheet metal parts is unknown. At this point, it is necessary to use“ Test bending; Method to obtain its bending compensation value. The specific operation is as follows: First, use a machine tool to cut two square materials of equal size from the supplier of the material to be tested, then accurately measure the dimensions in both directions, and then bend them in parallel and perpendicular directions. After bending, measure the length of the two straight edges. At this point, the bending compensation value is equal to the length of two right angles and the length of the original square material, which can obtain the compensation values of the raw material in all directions.