Several Process Instructions for Sheet Metal Processing
Sheet metal processing welding process: For the welding of sheet metal processing parts, commonly used welding methods include argon arc welding, resistance spot welding, carbon dioxide gas shielded welding, manual arc welding, etc. The overall welding method should be considered based on the structural characteristics of sheet metal processing parts. When selecting welding process methods, the technical requirements should be met first. Under this premise, try to choose methods with high economic benefits and low labor costs. For most structures, CO gas shielded welding and argon arc welding should be selected. Some machine tools have excessive external protection for sheet metal. The width of the base metal plate is limited, and splicing is required during cutting to meet the requirements. These sheet metal parts are usually thin sheets with a thickness of less than 2mm. Welding deformation and stress should be considered during splicing.
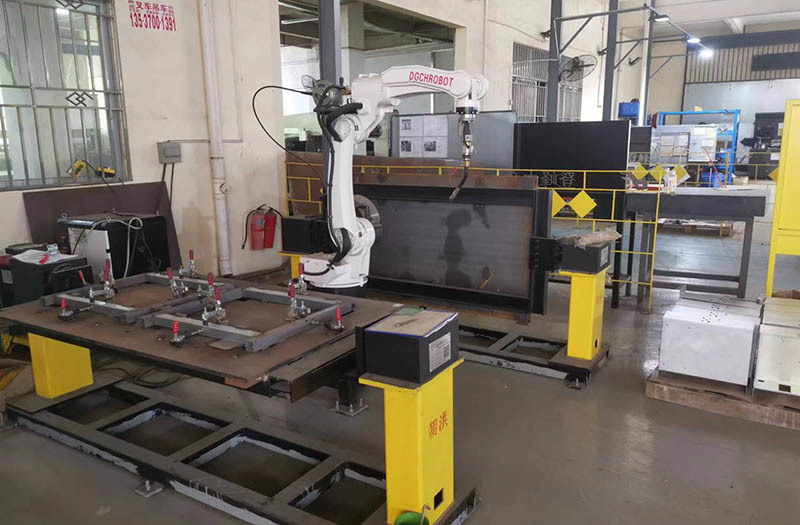
For example, when welding the splicing joints of key components of machine tools, such as the front cover, water guide plate, and other joints that require waterproof treatment, it is necessary to align the two plates completely to ensure there is no gap, and then use continuous spot welding. After welding, a special metal plate adhesive should be applied to the joint for waterproof treatment; When it is necessary to weld medium thick plates and full welding processes, reasonable current and voltage should be adjusted, segmented full welding and reasonable welding sequence should be adopted to ensure structural strength and reduce welding deformation; When welding parts with high sealing requirements such as fuel tanks and water tanks, in order to avoid welding defects and ensure aesthetics, the flat welding parts should be fully welded with grooves, polished flat after welding, and subjected to kerosene testing to detect leaks; When welding large plates that are prone to deformation, reinforcing ribs should be installed on the inside and plug welding connections should be used as much as possible; When the thickness of the plate is greater than 3mm and there is no excessive requirement for structural strength, segmented welding should be used as much as possible to reduce welding deformation; Nut welding machine can be used to weld nuts to improve production efficiency. After welding, the surface of the parts should be polished to remove welding slag and solder balls. Sometimes, it is necessary to polish the weld seam. At the connection of the circular arc plate, the rounded corners should be polished uniformly. At the same time, polish the burrs and burrs to prevent paint from peeling off, check whether the welding parts are firm and beautiful, whether there is distortion or deformation, whether the external dimensions meet the tolerance requirements, and make adjustments.
Sheet metal processing spraying process: The appearance of metal plates often reflects the quality of later products, so spraying process is particularly important. The commonly used sheet metal spraying process is plastic spraying. The processing method is that the assembled and welded metal plates need to undergo acid pickling and rust removal first. After pickling, use a wire brush to polish the floating rust. For some locations with surface defects or joints, putty should be applied. After the putty solidifies, polish it with a polishing machine and then spray powder. Place the sprayed workpiece in a high-temperature furnace, heat it to 200 ℃, then take it out and leave it at room temperature until it cools down.
Through certain scientific experiments, combined with actual processing methods and production conditions, explore the corresponding sheet metal processing part bending coefficient compensation table. Related research has accelerated the development of sheet metal parts to a certain extent and is also beneficial for their accurate processing. In this way, the machining accuracy of the parts has been improved, and the machining efficiency of sheet metal parts has also been enhanced. By effectively controlling welding deformation and post weld surface treatment, the quality and aesthetics of the product are ensured, thereby meeting the objective needs and long-term development of sheet metal technology, adapting to the needs of national economic construction, and participating in international competition.