Choosing the appropriate machining technology is crucial in the precision machining process, as it directly affects machining efficiency, quality, and cost. Therefore, the following are some guiding principles for selecting appropriate processing techniques.
The first factor to consider is the material of the parts. Different materials have different requirements for processing technology. For example, metal materials can usually be processed through common mechanical processing techniques such as milling, turning, and drilling. Non metallic materials such as plastics and ceramics usually require special processing techniques such as cutting and cutting. In addition, the hardness, toughness, thermal sensitivity and other characteristics of the material should also be considered, and these factors should be fully taken into account when selecting processing techniques.
Secondly, it is necessary to consider the geometric shape and dimensions of the parts. Different geometric shapes have different requirements for processing techniques. For example, complex shapes typically require CNC Machining techniques, while simple shapes can be processed using conventional mechanical machining techniques. In addition, consideration should be given to whether the dimensions of the parts can meet the requirements of the selected machining technology, as different machining technologies have different limitations on the dimensions of the parts.
Thirdly, the factors to be considered are the requirements for machining accuracy and surface quality. Different processing techniques have different requirements for processing accuracy and surface quality. For example, non mechanical machining techniques such as precision cutting and electrical discharge machining can achieve higher machining accuracy and better surface quality, while mechanical machining techniques often cannot meet such requirements. Therefore, when choosing processing technology, it is necessary to make judgments based on specific requirements.
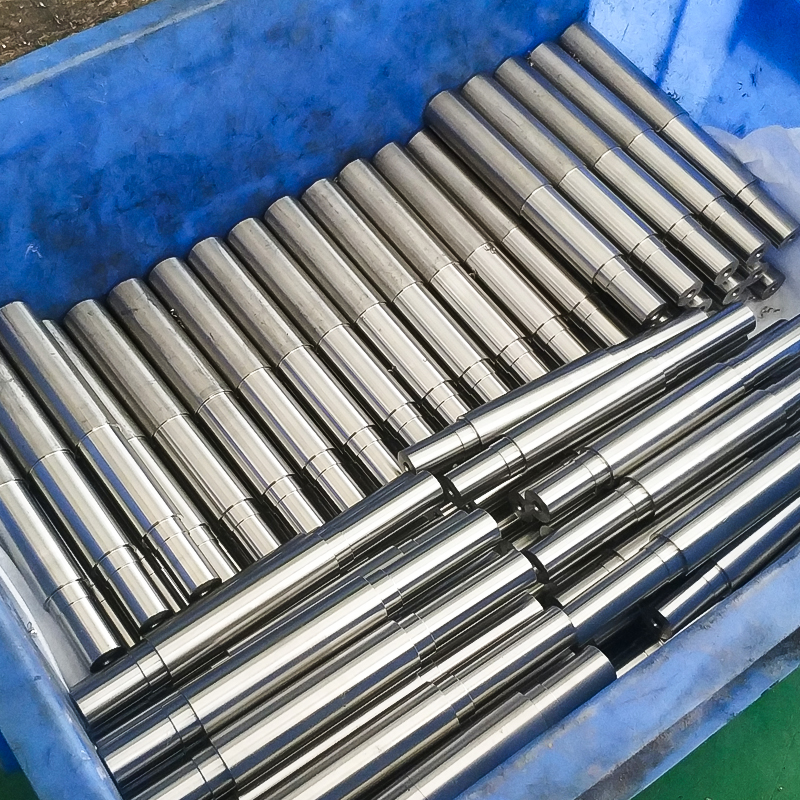
Fourthly, factors that need to be considered are processing efficiency and cost. Different processing techniques have varying impacts on processing efficiency and cost. For example, CNC machining technology usually has high machining efficiency, but the corresponding equipment and tool costs are relatively high. Although conventional machining techniques have lower efficiency, their cost is relatively low. Therefore, when choosing processing technology, it is necessary to comprehensively consider the efficiency and cost of processing.
Finally, factors that need to be considered are the conditions and equipment of the processing site. Different processing techniques have different requirements for the conditions and equipment of the processing site. For example, using CNC machining technology requires corresponding CNC machine tools and programming personnel, while using cutting technology requires special cutting equipment and operators. Therefore, when choosing processing technology, it is necessary to ensure that the processing site has the corresponding conditions and equipment.
In summary, selecting the appropriate processing technology requires consideration of the material, geometric shape, and size of the parts, the requirements for processing accuracy and surface quality, processing efficiency and cost, as well as the conditions and equipment on the processing site. Only by considering these factors comprehensively can the most suitable processing technology be selected to ensure the effectiveness and efficiency of the processing process.