Instructions for Sheet Metal Processing, Assembly, and Bending Process
It is very important to understand the entire process of bending deformation of sheet metal processing parts. When the board is bent, it mainly serves three functions: bending moment, shear force, and local pressure. Bending moment is mainly generated by the bending and deformation of sheet metal workpieces. When sheet metal processing parts deform, they are affected by external forces. Under the action of external forces, resistance will inevitably be generated inside it. At this point, external and internal forces should be equal. At this point, if the external force increases correspondingly, the internal stress will also increase, resulting in a greater degree of bending. However, all sheet metal materials have elastic limits. Before reaching the elastic limit, the sheet metal workpiece is in an elastic deformation state. If the external force disappears, the sheet metal material will return to its shape before the force is applied. However, if the external force continues to increase when the sheet metal workpiece reaches its elastic limit, its plastic deformation will become prolonged. That is to say, after removing external force, the sheet metal material will not return to its original shape and will undergo long-term deformation. This process is the deformation process of sheet metal processing parts that we mainly study. When the external force is too large, the sheet metal workpiece will break due to its long-term deformation. In this case, sheet metal materials will lose their practical value. During the bending process, there may be other factors that can affect the bending process of the board.
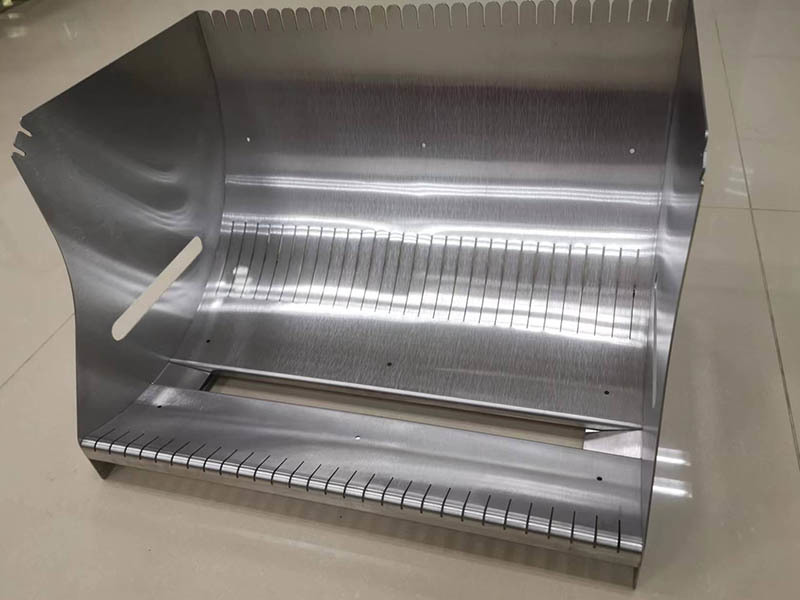
Small bending radius of sheet metal processing parts
When a sheet metal workpiece is bent, the inner layer of its rounded corner will be compressed, and the outer layer will be stretched accordingly. The smaller the bending angle, the greater the compression and stretching effects on the material when the thickness of the sheet metal workpiece remains unchanged. When the tensile force reaches its limit, the sheet metal workpiece will break or fracture. Therefore, in the design of curved parts, smaller bending radii should be avoided as much as possible. Usually, sheet metal materials use larger bending radii. If there are no special requirements for the bending radius in practical operation, the bending fillet should be smaller than the thickness of the sheet metal material.
Distance between hole edges of sheet metal bending parts
The hole should be kept at a certain distance from the bending area, because if the distance between the two is too close, the sheet metal material will stretch the hole during bending, thereby affecting the use of the part. Therefore, in the design of sheet metal processing parts, it is necessary to ensure that the distance between the edge of the bent hole and the outer side is greater than three times the thickness of the plate. If the distance cannot be controlled, a small hole should be drilled before bending, and then expanded after bending deformation to meet the requirements.
Height of straight edge of sheet metal bending parts
For sheet metal parts with a bending angle of 90 degrees, in order to facilitate forming and use, their height is usually greater than twice their thickness. If the height is less than twice the thickness due to design or other requirements, bending operation should be carried out first, and then processing should be carried out according to the requirements after bending to achieve the target size. For sheet metal parts with sloping edges, first ignore the right angled edges, perform bending operations first, and then perform cutting operations after bending to make it a sloping edge and meet the target requirements.