Materials to be selected for Sheet Metal Processing:
Sheet metal processing parts are common structural components that can be widely used in many fields. The primary processing methods for sheet metal parts are welding and laser cutting, which have the advantages of light weight, good rigidity, and high precision. The thickness of general sheet metal parts is less than 6mm, and various shapes of parts can be made through diverse cold processing techniques. After sheet metal cold processing, the thickness of sheet metal parts can be changed to a more fixed thickness. However, due to the different uses of sheet metal, different sheet metal materials need to be selected.
Generally, sheet metal processing materials are mainly divided into the following types: stainless steel, copper, aluminum, and other materials. Different types of sheet metal materials require different processing methods and approaches.
1.1 Stainless steel plate.
(1) Cold rolled steel plate. Cold rolled steel plate is a type of steel plate that is controlled at room temperature below the recrystallization temperature and then rolled to become thinner. In cold-rolled steel plates. It has a smooth appearance, uniform thickness, does not incur significant costs, and is easy to shape. Can be painted or electroplated to expand the application scale of steel plates.
(2) Hot rolled steel plate: This steel plate processing method mainly involves treating the initial rolled plate or casting blank, heating it, and then dephosphorizing it to form a rough rolled steel plate. Generally, the thickness of hot-rolled steel plates may have slight deviations, and folding problems may occur during actual processing. The processing skills of hot-rolled steel plates are primarily used to produce components for equipment such as cars, bridges, and ships.
1.2 Galvanized sheet.
Galvanized sheet is primarily galvanized on the surface of the steel plate. In general, it is necessary to control the thickness of the galvanized layer on the steel plate to be at least 10m to prevent corrosion and other damage to the surface of the steel plate. This is mainly due to the high requirements for anti-corrosion when used in parts.
Regarding copper plates, sheet metal processing enterprises require the use of electrical materials in the actual processing process, such as chrome plating and nickel plating on the surface of the copper plate. In addition, spraying treatment can also be carried out, but the cost of such materials is relatively high. Generally, aluminum plates are treated with chromate on the surface and can also be oxidized through chemical and conductive methods. They are primarily used to make boxes.
Rules and matters for sheet metal processing
There are clear rules for the division of labor and operational requirements in sheet metal processing. On the basis of drawings and batches, different cutting methods such as laser, sheet metal processing, CNC punching, cutting, and molds are not selected. Today, we will introduce the specific rules for manufacturing sheet metal processing.
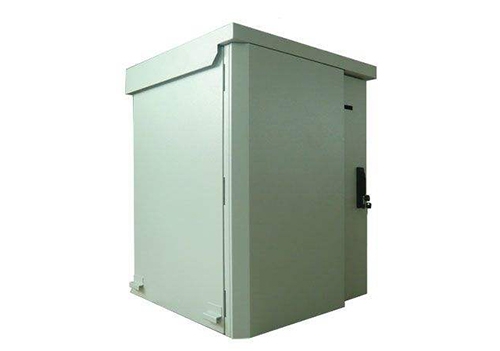
1. Select the cutting material, proceed to the next process after completion, and process different stainless steel workpieces into corresponding processes according to requirements;
When the elbow is made of stainless steel according to the dimensions and thickness on the drawing, the key to selecting the form to avoid product collision deformation (different types of upper and lower molds can be used for the same product) is to confirm the thickness of the plate;
3. When we press the rivet, we should consider the same height of the stud, select the same mold, and then adjust the pressure of the press to ensure that the stud and the surface of the workpiece are neat, so as to prevent the stud from pressing into or over the surface of the workpiece and forming the workpiece. Welding includes argon arc welding, spot welding, carbon dioxide repair welding, technical welding, etc. Spot welding primarily considers the welding direction of the workpiece and the position of the stainless steel plate in mass production to ensure the accuracy of spot welding
4. In order to weld firmly, when welding convex workpieces, the convex points can be made uniform with the plane before welding to ensure heating of the common contact points and confirm the welding direction. Welding should also be carried out, adjusting the preloading time, persistence time, maintenance time, and rest time to ensure that the workpiece can be set on site;
The quality of stainless steel plates is not only strictly required by the production process, but also unrelated to the strict production quality. One is to strictly inspect according to the drawings, and the other is to strictly control the appearance quality. This kind of sheet metal processing is not very important, otherwise the effect of the process would be difficult, and it can be discovered during this processing.
The content of the article is sourced from the internet. If you have any questions, please contact me to delete it!