How to determine the process parameters of laser cutting in Shenyang?
Working principle of laser cutting
Laser cutting processing replaces traditional mechanical knives with invisible beams, and has the characteristics of high precision, fast cutting, not limited to cutting patterns, automatic typesetting to save materials, smooth cutting, and low processing costs. It will gradually improve or replace traditional metal cutting equipment. The mechanical part of the laser blade has no contact with the workpiece and will not cause scratches on the surface of the workpiece during operation; Laser cutting speed is fast, the incision is smooth and flat, and generally does not require further processing; The cutting heat affected zone is small, the deformation of the board is small, and the cutting seam is (0.1mm~0.3mm); The incision has no mechanical stress and no shear burrs; High processing accuracy, good repeatability, and no damage to the material surface; Numerical control programming, capable of processing any flat plan, can cut large entire boards without the need for molds, saving time and economy.
Composition of laser cutting equipment
Laser cutting equipment mainly consists of laser, light guide system, CNC motion system, automatic height adjustment cutting head, work platform, and high-pressure gas blowing system. Many parameters can affect the laser cutting process, some of which depend on the technical performance of the laser and machine tool, while others are variable. The main parameters of laser cutting are:
Main parameters of laser cutting
1 Beam Mode
The fundamental mode, also known as Gaussian mode, is the ideal mode for cutting, mainly appearing in low-power lasers with a power of less than 1kW. Multimode is a mixture of higher-order modes, with poor focusing and low cutting ability at the same power. Single mode lasers have better cutting ability and quality than multimode lasers.
2 laser power
The laser power required for laser cutting mainly depends on the cutting material, material thickness, and cutting speed requirements. Laser power has a significant impact on cutting thickness, cutting speed, and incision width. Generally, as the laser power increases, the thickness of the material that can be cut also increases, the cutting speed accelerates, and the incision width also increases.
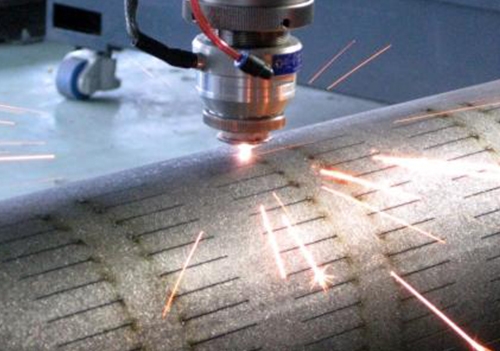
3 Focus positions
The focal position has a significant impact on the width of the incision. Generally, the focus is chosen to be located about one-third of the thickness below the material surface, with a larger cutting depth and a smaller mouth width.
4 focal moments
When cutting thicker steel plates, a beam with a longer focal length should be used to obtain a cutting surface with good verticality. The depth of focus increases, the diameter of the light spot also increases, and the power density decreases accordingly, resulting in a decrease in cutting speed. To maintain a certain cutting speed, it is necessary to increase the laser power. It is advisable to use a beam with a smaller focal length for cutting thin plates, which results in a smaller spot diameter, higher power density, and faster cutting speed.
5 Auxiliary gases
Cutting low carbon steel often uses oxygen as the cutting gas to promote the cutting process by utilizing the heat of iron oxygen combustion reaction. Moreover, the cutting speed is fast, the cutting quality is good, and a slag free cutting can be obtained. The pressure increases, the kinetic energy increases, and the slag discharge capacity is enhanced; The cutting pressure is determined based on factors such as material, plate thickness, cutting speed, and cutting surface quality.
6 nozzle structure
The structure and shape of the nozzle, as well as the size of the light outlet, also affect the quality and efficiency of laser cutting. Different cutting requirements require the use of different nozzles. The commonly used nozzle shapes include cylindrical, conical, square, and other shapes. Laser cutting generally uses coaxial (air flow concentric with the optical axis) blowing method. If the air flow is not aligned with the optical axis, a large amount of splashing is easily generated during cutting. To ensure the stability of the cutting process, it is usually necessary to control the distance between the nozzle end face and the workpiece surface, which is generally 0.5-2.0mm, in order to facilitate smooth cutting.
The content of the article is sourced from the internet. If you have any questions, please contact me to delete it!