The stamping equipment used by stamping manufacturers has its unique effects and requires daily protection to extend its service life. So, how should we operate the daily protection of high-speed stamping molds? The stamping manufacturer will show you:
1. For high-speed stamping dies with a blade clearance of less than 0.02mm or a monthly production of 50000 stamping parts exceeding 1 million stamping parts, the punch is prone to breakage and wear. We should plan a quick change structure with a punch clearance of 0.01mm on one side of the stripping plate for sliding. The cutting edge of the lower mold needs to be fitted with inserts, and the inserts and movable blocks that are prone to material blockage should be planned as screw locking types, and the mold teeth should be tapped or top holes should be added to the lower seat cushion. For high-speed stamping molds with a thickness less than (including) 0.3 or a monthly production of 50000 stamping parts and a total production exceeding 1 million stamping parts, auxiliary guide sleeves should be planned for the release plate and lower mold.
3. During high-speed stamping, reinforcement or support punches should be used for circular punches with a diameter less than 2.0 or irregular punches with an appropriate side length less than 1.5. If necessary, secondary support inserts should be made on the stripping plate.
4. During high-speed stamping, circular holes with a diameter less than 1.2 or irregular holes with a side length less than 1.2 should be embedded in the discharge plate, and punch support holes should be planned for the stop plate (straight single+0.01~0.015mm, and the discharge plate and stop plate should be positioned with cutting pins).
5. The size of the mold seat for high-speed stamping parts should adapt to parameters such as the punch table and the height of the closed mold.
This article is from EMAR Mold Co., Ltd. For more EMAR related information, please click on www.sjt-ic.com,
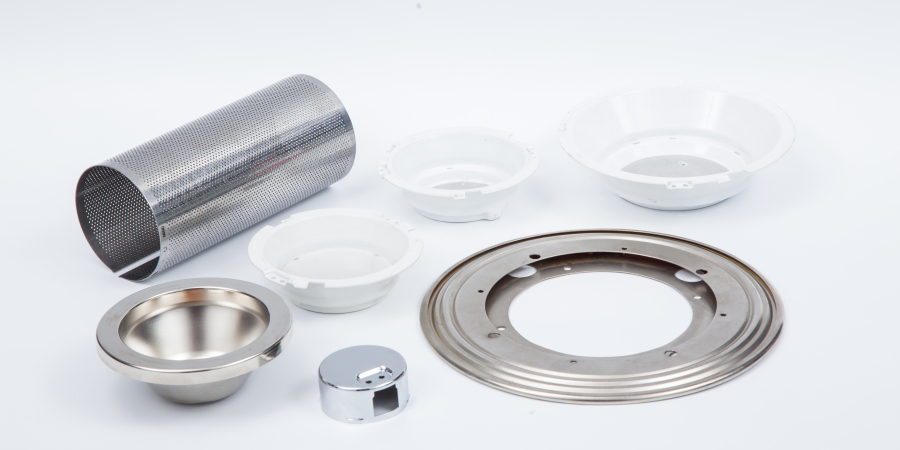