CNC Machining and ultrasonic machining of quartz glass
Our cutting-edge capabilities include precision glass CNC machining services and ultrasonic machining.
Although they use similar computer technologies, glass CNC machining and ultrasonic machining have different characteristics, making them ideal choices for different applications. Below, we will discuss the subtle differences between glass CNC machining and ultrasonic machining to help you choose the process that suits your needs.
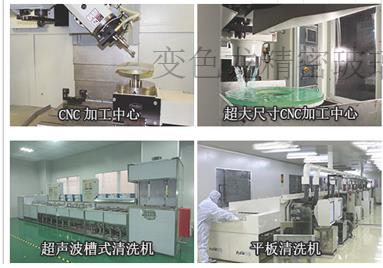
What is glass CNC machining?
Glass CNC machining, also known as glass milling, uses computer-controlled tools to accurately remove materials from glass workpieces. CNC machining allows operators to cut and shape workpieces on multiple axes, and can be used to create various sizes, shapes, and features, such as grooves, grooves, and holes.
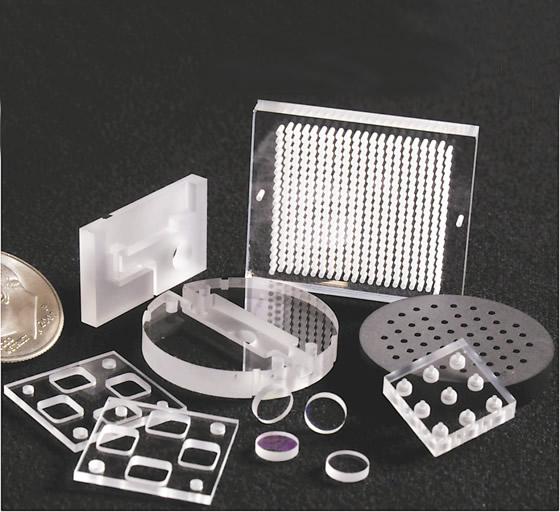
The precision and versatility of glass CNC machining make it highly suitable for a wider range of applications and industries, including:
Aerospace/Defense: CNC machining is used to manufacture instruments, instruments, and other components with complex shapes.
Biotechnology: Biotechnology companies use CNC processing components such as flow pools to promote material flow through precision channels and cavities.
Semiconductor: The semiconductor industry uses precision CNC processed glass for wafer stages, reference frames, windows, and lenses.
Telescopes: Telescopes and microscopes require highly precise and stable mirrors and lenses, which can only be produced using precision CNC machining.
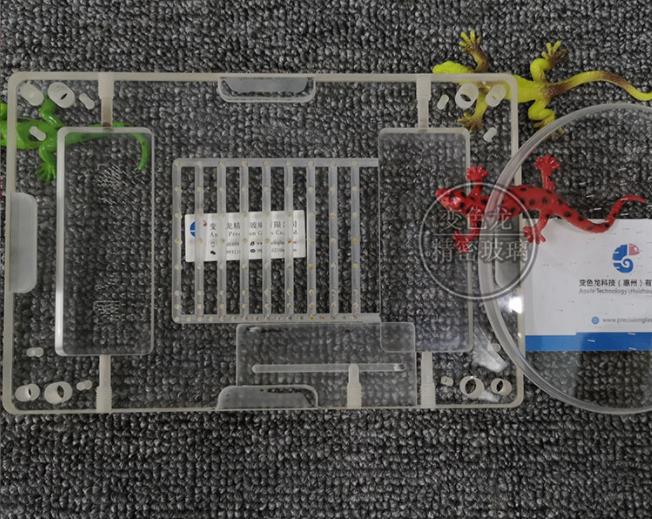
What is ultrasonic machining?
Ultrasonic machining, sometimes referred to as ultrasonic drilling, uses abrasive slurry and ultrasonic vibration to remove material from glass workpieces. Unlike cutting and grinding, the slurry removes trace amounts at once and finely grinds the desired shape into glass. Slow wear eliminates the possibility of stress accumulation in the workpiece, thereby maintaining the zero crystal structure and strength of the glass.
Ultrasonic machining has a wide range of applications and can be used to create cavities and holes of different shapes, sizes, and depths, including height specific outer diameter (OD) and inner diameter (ID) features. The industries that benefit from ultrasonic processing of glass components include:
Aerospace: Ultrasonic processing is used to manufacture pressure sensors, flight instruments, and other sensitive glass components in aircraft and aerospace equipment.
Automotive: Ultrasonic processed glass forms advanced sensors for proximity detectors, backup applications, and other safety functions.
Medical: Various medical devices include glass components processed using ultrasonic methods.
Semiconductor: The semiconductor industry often uses ultrasonic processed glass for chips, electrodes, distribution boards, lenses, and mirrors.
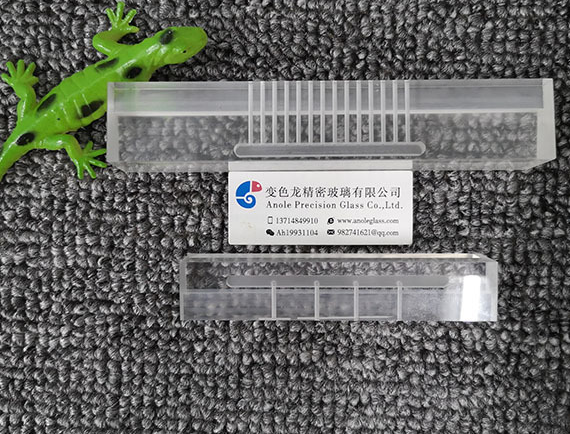
CNC machining and ultrasonic machining
Although both glass CNC machining and ultrasonic machining are used to manufacture precision glass components, each method provides unique advantages for specific applications.
Glass CNC machining has a wide range of applications and can be used to manufacture complex components with extremely small tolerances. Another benefit of CNC quartz glass processing is the ability to produce precise components with minimal manual supervision.
Ultrasonic machining can produce precise shapes, holes, and cavities on extremely hard glass that is difficult to mill. Due to the fact that it does not require direct pressure, heat, chemicals, or electricity, ultrasonic processing imposes less stress on glass materials, promoting stronger components, making it highly suitable for critical applications and high-pressure operations.
Due to the fact that ultrasonic processing does not deform or compress glass, it is the perfect choice for components that require multiple holes and cavities. The gradual removal of a very small amount of surface material allows ultrasonic machining to drill to very precise depths. Unlike CNC milling, ultrasonic machining can drill multiple holes at high speed and accuracy without affecting the integrity of the workpiece. For complex glass components with many holes, this may be a very effective and cost-effective large-scale production method.