The Sheet Metal Processing industry has brought a lot of convenience to people's lives, so the rapid increase in demand for sheet metal processing has also enabled sheet metal processing manufacturers to achieve rapid development. Different industries have different requirements for sheet metal processing components, so more and more consumers choose to customize sheet metal. So how much does sheet metal processing cost? How to calculate the price? Do you know what expenses are mainly included? Below, the editor of Emma Technology Co., Ltd. will introduce to you:
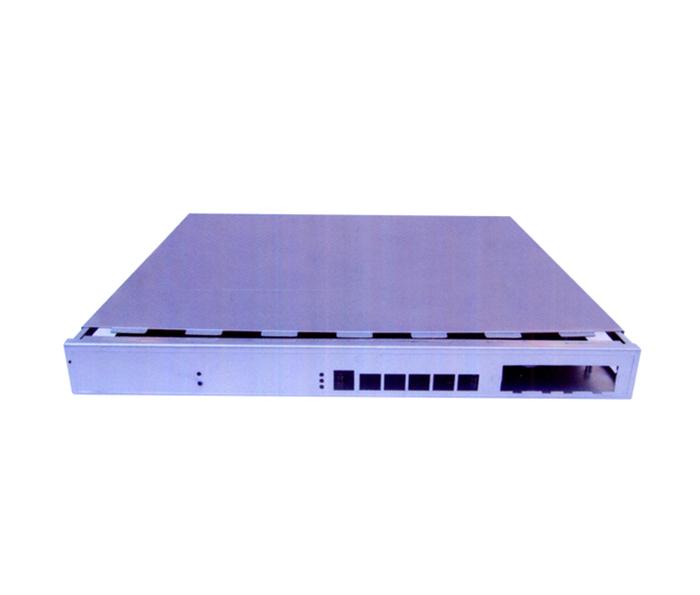
1. Raw material cost: usually refers to the net material cost of the metal sheet required for sheet metal parts, based on the maximum length, width, dimension, thickness density of the part drawing, material cost=material weight, material unit price.
2. Hardware accessory cost: refers to the procurement cost of complete sets of accessories such as locks, hinges, handles, nameplates, rivets, or fastening standard parts according to the requirements of the product drawings.
3. Processing cost: refers to the cost required for the product processing process. The processing cost usually consists of the depreciation and amortization of equipment used at each workstation, the cost of labor hours, and the necessary auxiliary materials for processing.
Cutting: Cutting machines, CNC punching machines, laser cutting, plasma, specialized mold punching machines, etc. These cutting equipment have different depreciation and amortization costs, processing quality and accuracy, and production efficiency. Forming: For bending machines, rounding machines, riveting or welding equipment, etc., the number of bending blades, number of welds, welding requirements, welding skills, etc. are calculated separately for equipment depreciation and amortization, labor costs, and auxiliary consumables. Surface treatment: refers to the costs of electroplating, oxidation, drawing, polishing, spraying, screen printing, etc.
4. Packaging cost: The cost of purchasing packaging materials required based on the transportation method and packaging requirements of the product. Transportation cost: The transportation cost required for each delivery batch is allocated to the cost of each product.
5. Management expenses: Various expenses incurred for organizing and managing production and business activities.
6. Profit: It is a powerful support for the survival, stable development, and better customer service of enterprises.