CNC milling machine is an automatic processing equipment developed on the basis of general milling machines. Although different types of CNC milling machines have differences in composition, they have many similarities. The design of the processing route for CNC milling machines must comprehensively consider various factors, pay attention to the correct division and sequence of processes, and arrange the connection between CNC milling processes and ordinary processes reasonably. In the division of processes, it is necessary to flexibly grasp factors such as the structural requirements of the workpiece, the installation method of the workpiece, the processing technology of the workpiece, the performance of CNC milling, and the production organization and management of the factory. Below, Emma Technology Co., Ltd. briefly introduces the selection of CNC milling machines and the method of process division:
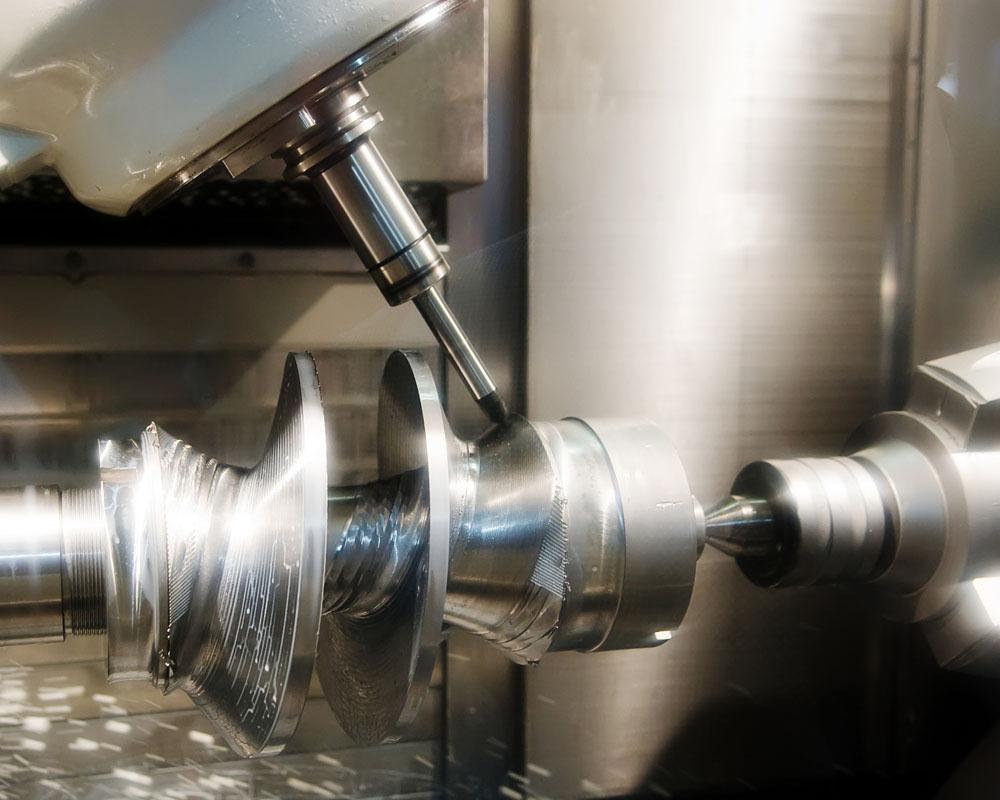
1、 The selection principles of CNC milling machines
(1) Select according to the size of the processed parts
A small-sized lifting table CNC milling machine is most suitable for machining small and medium-sized parts and complex surface contour milling tasks on its workbench. Larger specifications such as gantry milling machines are used to solve the machining needs of large-sized complex parts.
(2) Select according to the precision requirements of the processed parts
China has established precision standards for CNC milling machines, among which there are professional standards for CNC vertical milling machines, lifting table milling machines. A typical CNC milling machine can meet the machining needs of most parts. For parts with high precision requirements, precision CNC milling machines should be considered.
(3) Select according to the processing characteristics of the processed parts
For machining parts with frame shaped planes or unequal heights of various levels of steps, a CNC milling machine with a point position linear system can be selected.
If the processing part is a curved surface contour, the selection of a two coordinate linkage and a three coordinate linkage system should be based on the geometric shape of the surface.
According to the machining requirements of the parts, a CNC indexing head or CNC rotary worktable can also be added to the general CNC milling machine. At this time, the machine tool system is a four coordinate CNC system, which can process spiral grooves, blade parts, etc.
(4) Select according to the batch size or other requirements of the parts
For large quantities, users can use specialized milling machines. If it is a small to medium batch production with frequent periodic repetition, then using a CNC milling machine is very suitable because many fixtures, programs, etc. are prepared in the first batch to be stored and reused.
In the long run, it is inevitable that milling machines with high levels of automation will replace ordinary milling machines, reducing the workload of workers and improving productivity.
2、 The division of machining processes in CNC milling
(1) Divide the process based on clamping positioning. This method is generally applicable to workpieces with limited processing content, mainly dividing the processing part into several parts, such as clamping the inner cavity during numerical control milling and clamping the outer cavity during machining.
(2) Divide the process into rough and fine machining. For CNC milling parts that are prone to machining deformation, considering factors such as machining accuracy deformation of the workpiece, the process can be divided according to the principle of separating rough and fine machining, that is, rough first and then fine.
(3) In order to reduce the number of tool changes, the principle of tool concentration can be adopted to divide the process. Prioritizing the use of centralized cutting tools can reduce the frequency of frequent tool changes, shorten the tool path, and thus improve machining efficiency.
3、 Selection of specialized cutting oil
Special cutting oil is a medium that must be used in CNC cutting technology, which mainly plays a role in lubrication, cooling, cleaning, and other functions during the machining process.
(1) The specialized cutting oil contains sulfurized extreme pressure and anti-wear additives, which can effectively protect the cutting tools and improve process accuracy.
(2) Compared with rapeseed oil, mechanical oil, and recycled oil, specialized cutting oil has good stability and will not cause harm to equipment, human health, or the environment.
(3) The specialized cutting oil has passed strict tests in viscosity, flash point, pour point, thermal conductivity, and other aspects to meet various cutting process requirements.
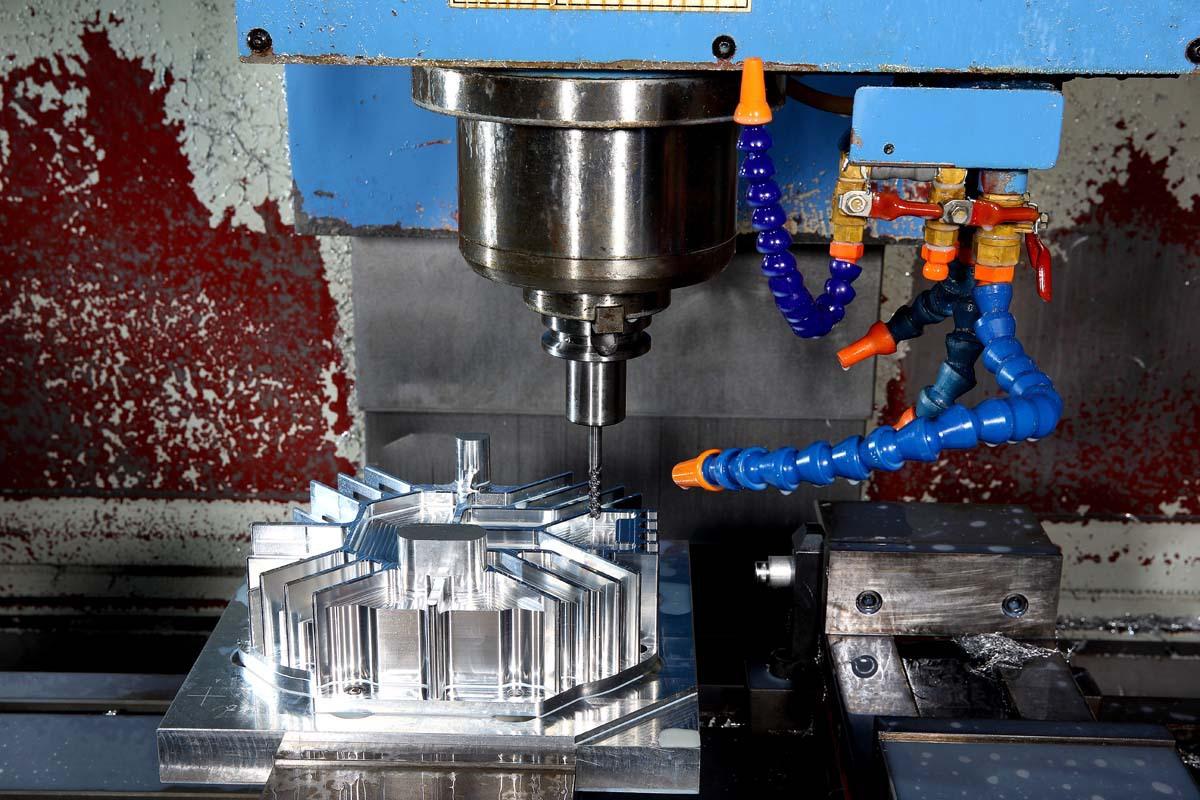
CNC milling machine processing has achieved standardization of processing information and is currently organically integrated with computer-aided manufacturing, which is the foundation of modern integrated manufacturing technology.
Emma Technology Co., Ltd. is one of the leading professional manufacturers of precision metal parts in China, established in 2006. It mainly undertakes business such as CNC Machining parts, metal stamping parts, and sheet metal processing.