Precision aviation parts machining refers to a machining technology that achieves precision requirements in terms of dimensions, shape, surface roughness, and contour accuracy of the machined parts. This processing technology has gradually developed and grown with the development of modern high-tech, mainly including various technical means such as milling, turning, polishing, electrochemical machining, etc. The commonly used heat treatment methods in the processing of precision aviation parts include the following: ⑴ Quenching and tempering: This is a preparatory heat treatment process, usually arranged before or after rough machining. By adjusting the hardness and toughness of the material, the cutting performance of the material can be improved. The quenched and tempered parts are not easily deformed during cutting, which can improve machining accuracy Annealing: Annealing is also a preparatory heat treatment process that reduces the hardness of materials, improves cutting performance, reduces cutting force and cutting heat, and thus extends tool life. Annealing treatment is usually arranged before rough machining Normalization: Normalization is a heat treatment process in which the workpiece is heated to a critical point AC3 or above 30 ℃~50 ℃, held for an appropriate period of time, and then uniformly cooled in free flowing air. Normalization can improve the machinability of materials, enhance the strength and toughness of parts Carburizing and quenching: This is a heat treatment process with significant deformation, usually arranged before precision machining. Carburizing and quenching can increase the carbon content on the surface of parts, improve surface hardness and wear resistance, while maintaining the toughness and strength of the core Nitriding: Nitriding is a heat treatment process with minimal deformation, usually arranged after precision machining. By infiltrating nitrogen atoms into the surface of the parts, the hardness and wear resistance of the surface are improved, and the service life of the parts is extended Time treatment: The purpose of time treatment is to remove internal stress and reduce workpiece deformation. Time treatment can be divided into three categories: natural time treatment, artificial time treatment, and cold treatment. Timeliness processing is generally arranged after rough machining and before precision machining; For parts with high precision requirements, another aging treatment can be arranged after semi precision machining.
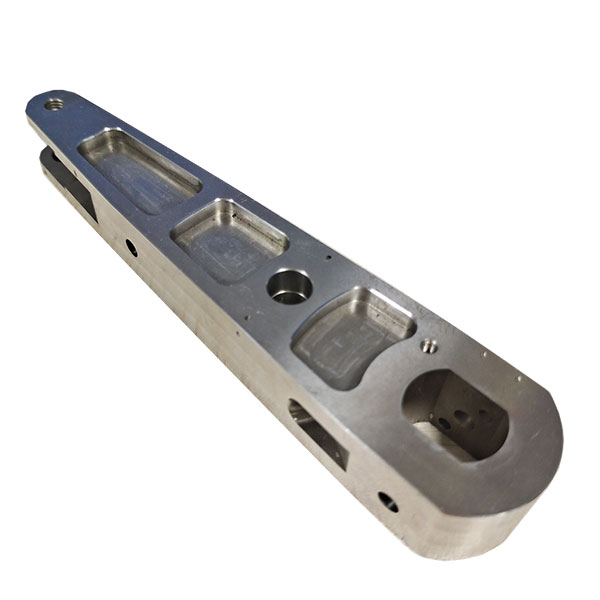