Punch heads are also called punch heads, upper dies, male dies, punch needles, etc., and punch heads are divided into A-type punch heads, T-type punch heads, and special-shaped punch heads. A punch is a metal part installed on a stamping die in a Metal Stamping factory, used for direct contact with materials to cause deformation and cutting of materials.
The effect of a punch is to determine the shape of the product that is punched by the punch. The standard for planning a punch is to consider the shape of the product and the gap between the upper and lower molds. The gap consideration mainly depends on the thickness of the punched product, raw materials, etc. In addition, when planning automatic molds, it is necessary to be able to calculate the steps, and when making stamping dies, precision and accuracy must be achieved. There is no detailed standard for the effect of the punch on the material, and the mold punch is determined based on factors such as the shape, size, and material thickness of the product. In the metal stamping factory, sometimes the punch in the metal stamping mold may be bitten by the material and cannot be removed. For stamping parts processing factories, please check the following items:
1. Re grinding of punch and lower die. Molds with sharp cutting edges can produce beautiful cutting surfaces. If the cutting edge is blunt, additional punching force is required, and the workpiece cross-section is rough, resulting in significant resistance and causing the punch to be bitten by the material.
2. The gaps in the mold. If the gap in the mold is not selected appropriately with respect to the thickness of the plate, a large demolding force is required for the punch to detach from the material. If the punch is bitten by the material due to this reason, please replace the lower die with a reasonable gap.
3. The condition of the processed materials. When the material is dirty or there may be dirt, the dirt adheres to the mold, causing the punch to be bitten by the material and unable to be processed.
4. Materials with deformation. The warped material will clamp the punch after punching the hole, causing the punch to be bitten. Materials with warping, please flatten them before processing.
5. Excessive use of tension springs. It will make the spring exhausted. Please regularly check the performance of the tension spring.
This article is from EMAR Mold Co., Ltd. For more EMAR related information, please click on www.sjt-ic.com,
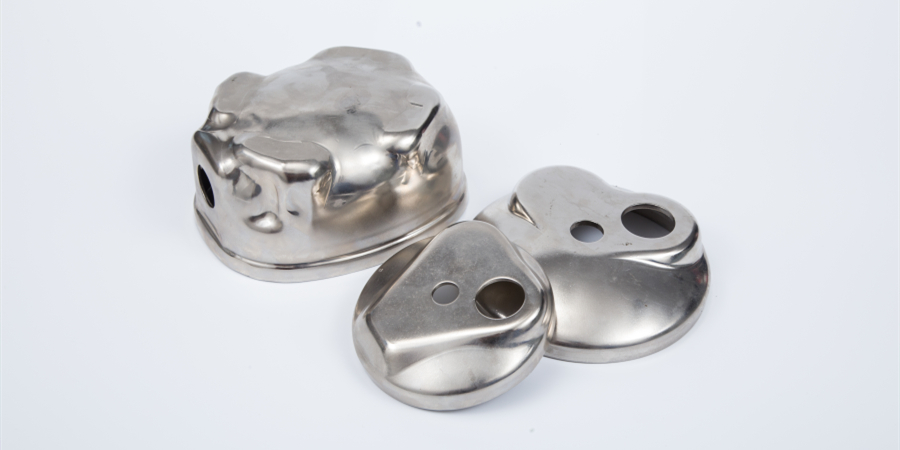