Hardware stamping is a process that uses punching machines and molds to deform or crack stainless steel, iron, aluminum, copper and other sheet materials and foreign materials, achieving precision stamping parts with a certain shape and size. Metal Stamping is sometimes referred to as sheet metal forming, but with slight differences. The so-called sheet metal forming refers to using sheet metal, thin-walled tubes, thin materials, etc. as raw materials. The forming method of plastic processing is collectively referred to as sheet metal forming.
Precision stamping parts are widely used in aerospace, cars, ships, machinery, chemical industry and other fields, gradually becoming a major component in the current parts manufacturing industry. Sometimes there may be tearing, tilting, and other issues when making metal stamping parts. So, what should stamping manufacturers pay attention to when selecting raw materials for metal stamping parts?
1. In the standard types of steel plates, whether it is fixed length plates or rolled plates, materials of the same material and thickness have different sales prices depending on the roll width. So, in order to reduce costs, we need to put effort into the planning of purchasing roll widths, and try to select roll width ranges that do not increase prices while ensuring material utilization. Regarding the selection of suitable standard sizes for the fixed length plate, it is recommended to avoid secondary cutting after cutting from the steel mill to reduce cutting costs; Regarding coil forming, it is advisable to select coil materials and processes that are formed by unwinding, in order to reduce the workload of secondary shearing and improve work efficiency.
2. The thickness of the board has error requirements, and within the allowable error range, the board with the error should be selected first. Determining the shape and dimensions of the sheet metal for precision stamping parts is a prerequisite for analyzing the degree of deformation of the stamping parts, envisioning the processability, and establishing process specifications. If the shape of the sheet metal is suitable, not only can the uneven distribution of deformation along the sheet metal be improved, but also the number of trial mold adjustments can be reduced, thereby shortening the production cycle and improving productivity.
4. When selecting materials for product planning, it is important to prevent the use of high-grade raw materials that may result in excessive product performance. At the same time, while satisfying product and process requirements, it is advisable to select raw materials and thicknesses that are already used in existing mass-produced vehicle models to form material channels and facilitate subsequent acquisitions and inventory management. The key performance requirement for ordinary cold-rolled plates is their stretchability, so it is advisable to choose lower grade materials as much as possible while meeting the requirements of product quality. As for the selection of material thickness, in addition to considering the strength and weight of the formed body, attention should also be paid to the popularization of expected thickness. Due to the special thickness of the material, it is difficult for suppliers to supply and the price is also high.
This article is from EMAR Mold Co., Ltd. For more EMAR related information, please click on www.sjt-ic.com,
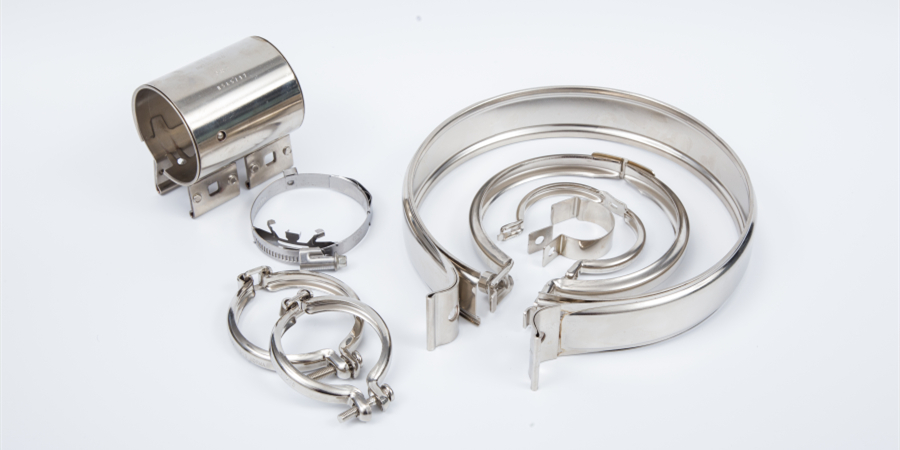