Electric spindle is a new technology that has emerged in the field of CNC Machining in recent years, integrating machine tool spindle and spindle motor. Along with linear motor technology and high-speed tool technology, it will push high-speed machining into a new era. The CNC machining electric spindle is a set of components, which includes the electric spindle itself and its accessories: electric spindle, high-frequency frequency converter, oil mist lubricator, cooling device, built-in encoder, and tool changer.
High speed spindle is the most important key technology in high-speed cutting technology and also the most important component of high-speed cutting machine tools. High dynamic balance, good rigidity, high rotational accuracy, good thermal stability, sufficient torque and power transmission, high centrifugal force tolerance, accurate temperature measurement device and efficient cooling device are required. High speed cutting generally requires a spindle speed capability of not less than 40000 r/min and a spindle power greater than 15 kW. Usually, electric spindle components with integrated spindle motors are used to achieve direct transmission without intermediate links. Induction integrated spindle motors are mostly used for motors. Currently, hot pressed silicon nitride (Si3N4) ceramic bearings, liquid dynamic and static pressure bearings, and air bearings are commonly used. Lubrication often uses techniques such as oil air lubrication and jet lubrication. The spindle cooling is generally achieved through internal water cooling or air cooling of the spindle.
1. Working principle diagram of ceramic bearing high-speed spindle
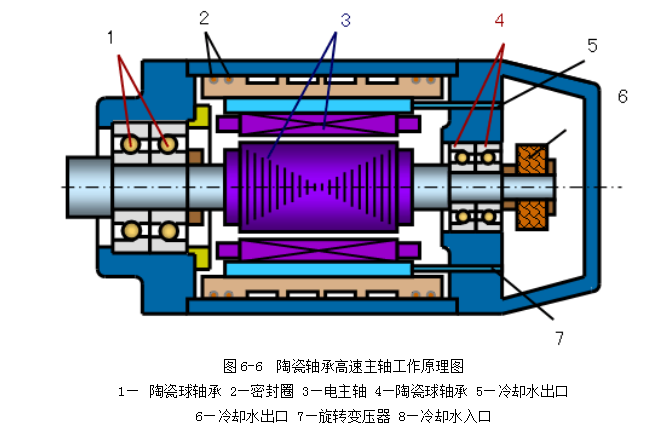
The above diagram shows the working principle of a ceramic bearing high-speed spindle, using C or B-grade precision angular contact ball bearings. The bearing arrangement is similar to the traditional grinder spindle structure; Adopting a "small bead dense ball" structure, the ball material is Si3N4; Adopting electric spindle (motor and spindle integrated); The characteristic value of bearing speed (=? Shaft diameter (mm), speed (r/min)) is increased by 1.2 ° C compared to ordinary steel bearings Twice, it can reach 0.5-1106. High rotational accuracy, with a rotational error of less than 0.2 μ m for liquid hydrostatic bearings and less than 0.05 μ m for air hydrostatic bearings; Low power loss; The characteristic speed of liquid hydrostatic bearings can reach 1106, and the characteristic speed of air hydrostatic bearings can reach 3106. The load-bearing capacity of air static pressure bearings is relatively small.
Compared with steel balls, the advantages of ceramic bearings are:
(1) The density of ceramic balls is reduced by 60%, which can greatly reduce centrifugal force;
(2) The elastic modulus of ceramics is 50% higher than that of steel, which gives bearings higher stiffness;
(3) Ceramic has a low coefficient of friction, which can reduce bearing heating, wear, and power loss;
(4) Ceramics have good wear resistance and long bearing life.
2. Maglev bearing high-speed spindle
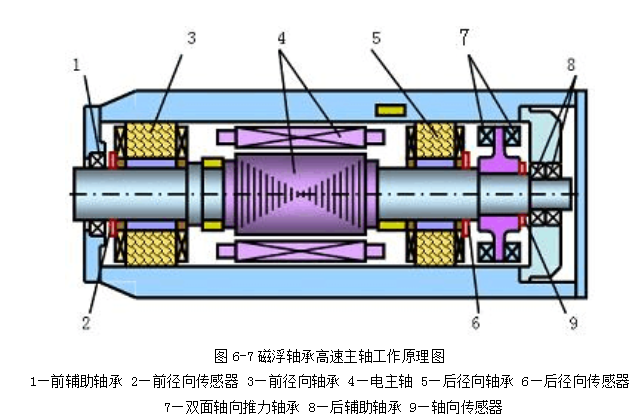
The above diagram shows the working principle of the high-speed spindle with magnetic levitation bearings. The spindle is supported by two radial and two axial magnetic levitation bearings, and the gap between the stator and rotor of the magnetic levitation bearings is about 0.1mm.? High stiffness, about 10 times the stiffness of a ball bearing spindle.? The characteristic value of rotational speed can reach 4106.? The rotation accuracy mainly depends on the accuracy and sensitivity of the sensor, as well as the performance of the control circuit, and can currently reach 0.2 μ m.? The mechanical structure and circuit system are both relatively complex; Due to the high heat generation, there is a high demand for the performance of the cooling system.