1、 The welding process for frame processing should ensure symmetry, balance, and verticality, and be made according to the size requirements of the drawing
1. When welding the frame, there should be no defects such as virtual welding, porosity, slag inclusion, cracks, welding edges, burn through, arc pits, undercutting, welding marks, or insufficient welding on the welding surface. Welding should be uniform and aesthetically pleasing;
2. The surface of the frame after welding shall not be uneven;
3. The surface of the aircraft should be smooth and the welding slag should be cleaned;
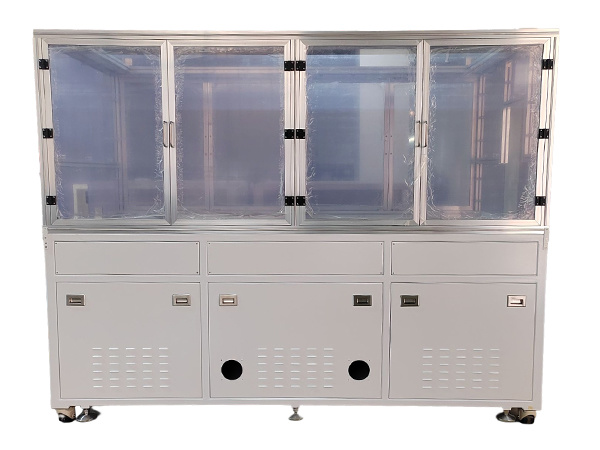
4. After welding the frame, the welding slag should be cleaned and the surface should be polished smooth;
5. The production of the tape guide groove should be consistent with the opening and closing of the page, with a smooth surface and no high or low opening or closing phenomenon.
6. The bending of sheet metal parts should be carried out according to the requirements of the drawing. The arc should be smooth, the bending surface should be flat, and there should be no unevenness. The size symmetry, parallelism, and perpendicularity should be ensured.
2、 Post welding treatment of frame
1. After the completion of the frame welding process, the slag splashing on the surface of the weld bead should be cleaned, and the size and appearance quality of the weld bead should be checked. If the weld seam is uneven, it should be repaired.
2. The shape of the weld seam should be smooth and uniform, and the transition between weld beads and between weld beads and base metal should be smooth.
3. For some components with closed structures, multiple welds, and long welds, residual stresses should be removed by hammering, vibration, and other methods after welding. If the parts require heat treatment, heat treatment should be used to remove stress.
3、 Characteristics of equipment rack processing
Firstly, customized equipment rack processing has strong extensibility. Aluminum profiles come in a complete range of specifications and are processed in various ways, all using CNC Machining for high precision. The surface of aluminum profiles has undergone anodizing treatment, making them corrosion-resistant, wear-resistant, moisture-proof, and fire-resistant. They can be used in most environments and have a long service life.
Secondly, choosing a customized equipment rack for rack processing has the following advantages: simple and fast assembly, no need for welding, environmental protection, and time-saving and labor-saving. These advantages are irreplaceable by other materials, whether they are expensive or environmentally friendly,
Taking the sheet metal chassis frame as an example: ensuring that the surface coating of the cabinet is firm and reliable, and has strong resistance to acid and alkali corrosion. The fan adopts a separate power circuit, which facilitates our maintenance. The shell of the fan unit adopts a one-time molding process, which can effectively reduce fan vibration and extend the service life of the fan unit. All angle gauges are galvanized to ensure safe grounding of the equipment. The installation and movement of the beam body are convenient and flexible. The optional accessories are complete, fully meeting the needs of various applications. Due to the use of imported specialized adhesives, tempered glass has a long service life. Bottom reinforcement bars, capable of bearing a weight of over 100kg. Choose mesh high-density front and rear doors to fully ensure shielding inside the cabinet. The connection method is simple, safe and reliable.
The sheet metal frame series products are widely used in mechanical equipment skeletons, bases, and other occasions that require high structural strength.