What are the classifications of Metal Stamping molds? EMAR Precision will give you a brief introduction. For metal stamping molds, we can simply divide them into three types: engineering molds, conformity molds, and continuous molds. These are several commonly used molds in metal stamping factories. Below, we will briefly introduce these three types of molds:
Metal stamping parts
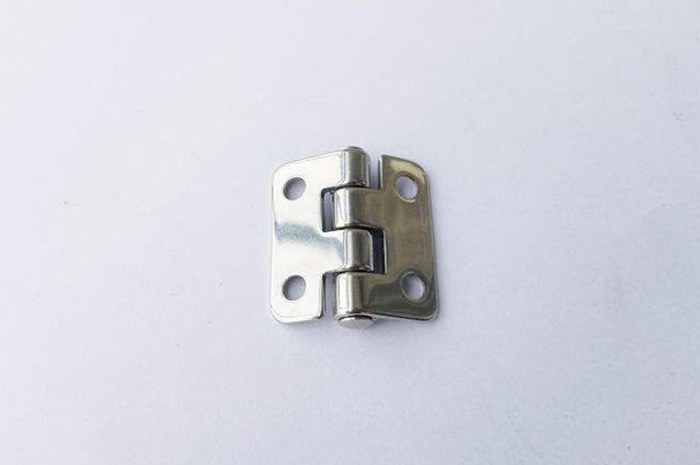
Engineering mold: This type of metal stamping mold requires manual or robotic labor to remove the product from the mold and place it in the next mold to continue production until one process of the mold is completed, and the entire product is considered complete. Maintenance is relatively simple, but manufacturing is time-consuming and labor-intensive, requiring a lot of labor and time costs, and the product scrap rate is high.
Composite mold: This type of metal stamping mold has a different structure from other engineering molds. Its punch is designed in the lower mold, and the other templates are the lower clamping plate (fixed convex mold), lower blocking plate, and lower stripping plate (stripping) in sequence. The upper mold is composed of a mother mold (or cutting edge), an inner stripping plate, and an upper backing plate in sequence. The stripping is hung on the upper backing plate with an equal height sleeve, and then supported by a rod or spring. For example, in the composite mold used for punching, the inner stripping is generally 0.50mm away from the mother mold and cannot be lower than the mother mold, otherwise the edge of the mother mold is prone to chipping or cannot be detached.
Metal stamping parts
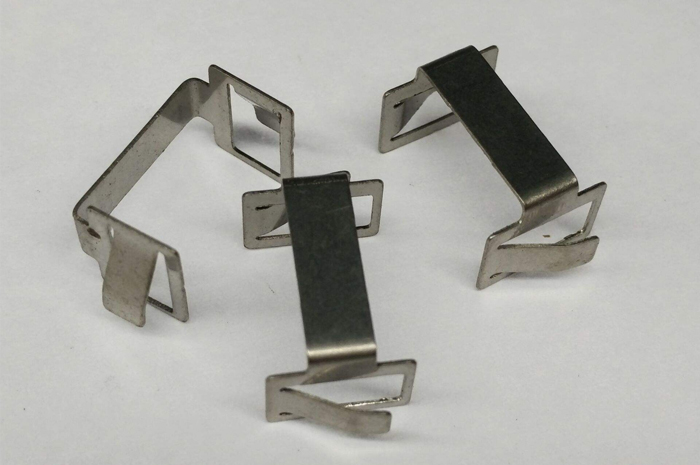
Continuous mold: This type of metal stamping mold is difficult to maintain and requires experienced assembly workers to operate, but it has high production efficiency. If the punching is fast, thousands of metal stamping products can be produced in an hour, saving labor and time costs, and the product scrap rate is low.