Today, let's briefly talk about how hardware stamping factories protect and repair the discharge plate in stamping molds:
1. The disassembly of the unloading plate in the Metal Stamping mold can be balanced and lifted with two screwdrivers first, and then balanced with both hands to remove the force. When encountering difficulties in disassembly, it is necessary to check whether the inside of the mold is clean, whether all the locking screws are disassembled, and whether there is any mold damage caused by material jamming. The cause should be identified as soon as possible;
2. When unloading the metal stamping die, the punch and unloading plate should be cleaned first, lubricating oil should be added to the guide column and punch inlet, and they should be placed smoothly. Then, press them in place with both hands and repeat several times; If it is too tight, the cause should be identified; If there are pressure blocks on the fixed plate, it is necessary to check whether the material theft on the discharge back plate meets the requirements. The material contact surface between the discharge plate and the concave mold will be pressed for a long time to produce pressure marks (the gap between the discharge plate and the concave mold is generally 0.03-0.05mm less than the material thickness). When the pressure marks are severe, it will affect the material's limiting accuracy, causing abnormal product size, instability, etc. Hardware stamping factories need to repair or grind the discharge inserts and discharge plates from scratch.
4. The precision of the medium height sleeve in the metal stamping mold should be checked. Its uneven height can cause the discharge plate to tilt, and its fine guidance and smooth spring pressing function will be damaged. It should also be protected.
This article is from EMAR Mold Co., Ltd. For more EMAR related information, please click on www.sjt-ic.com,
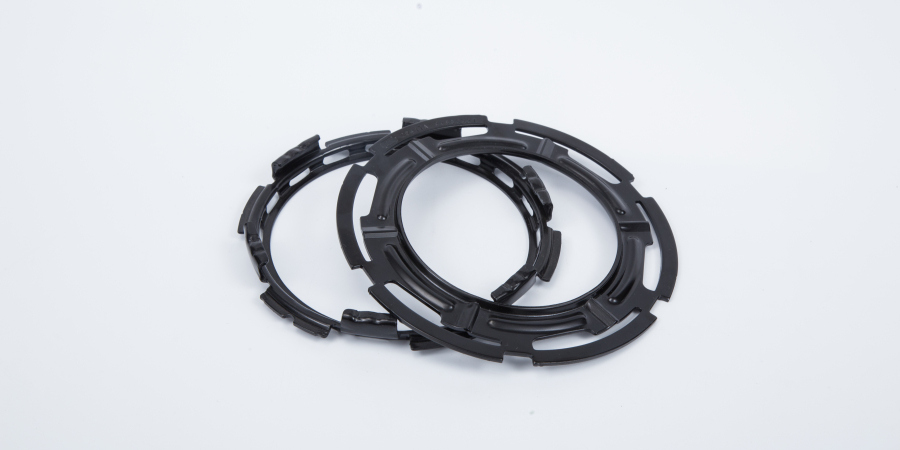