In a multi station progressive continuous stamping die in a hardware stamping factory, the workpiece of the nail arranging machine is stamped to complete the rolling forming and welding processes. But it still has a small part connected to the stamped sheet metal, which enters the ultrasonic surface treatment equipment together with the stamped and welded workpiece to remove anti rust grease and welding slag. Complete the removal of welding beads and burrs in the shot blasting room.
This is very necessary to avoid short circuits and electrical shorts during the use of stamped parts. In the second shorter ultrasonic surface treatment, before the quality inspection of the stamped parts, ultrasonic surface cleaning technology is used again to remove the residue left by shot peening treatment. After completing all the above operations, the stamped parts are completely separated from the blank sheet and stored separately together. The stamping parts with poor quality of the nail arranging machine are placed in the waste bin, while the qualified stamping parts are directly sent to the packaging workshop. During the production of Metal Stamping parts, damage may occur due to factors such as the lifespan of the metal mold, mold structure planning, selection of mold steel, heat treatment, surface treatment, mechanical processing and grinding, wire cutting technology, stamping equipment and process, mold smoothness, and maintenance and repair level.
How to avoid damage to stamped parts during the production process in a metal stamping factory? The following three are for our reference:
1. Revamp stamping equipment to improve production safety and reliability. There are many unsafe factors in the control systems and electrical control systems of many outdated stamping equipment nowadays. If they continue to be used, corresponding technical modifications should be carried out. Stamping equipment manufacturers should improve product design to ensure the safety and reliability of stamping equipment.
2. Install protective equipment. Due to the small production volume, it is necessary for hardware stamping factories to install safety protection equipment in stamping operations that cannot be automated or used for safe stamping to avoid injury accidents caused by operational errors. Various protective devices have their own unique characteristics and application scope, and improper use can still lead to injury accidents. Therefore, it is necessary to clarify the effectiveness of various protective equipment to ensure correct use and safe operation.
3. Transform processes, molds, and operating methods to complete manual mold work. For large-scale production operations, mechanization and automation can be achieved by starting with changing processes and molds. For example, using automation and multi station stamping machinery equipment, using multi cutting tools and mechanized production equipment, and adopting combined process measures such as continuous molds and composite molds. All of these not only ensure the safety of stamping operations, but also greatly improve production power.
This article is from EMAR Mold Co., Ltd. For more EMAR related information, please click on www.sjt-ic.com,
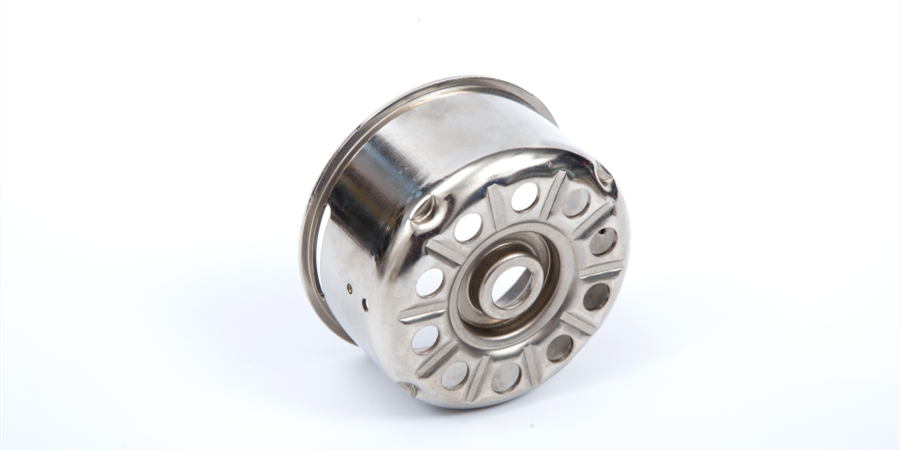