The key to avoiding wear and damage in CNC five axis machining lies in proper operation and maintenance. Here are some suggestions: Choose cutting parameters reasonably: Cutting parameters are a key factor affecting machining efficiency. By optimizing cutting parameters such as cutting speed, feed rate, and cutting depth, friction and wear between the tool and the workpiece can be reduced, thermal deformation and vibration during the machining process can be reduced, thereby avoiding wear and damage. Optimize tool selection and use: Choose tools that are suitable for machining needs and ensure their sharpness and rigidity. At the same time, it is necessary to use cutting tools reasonably to avoid excessive wear and chipping. Regularly checking the wear of cutting tools and replacing them in a timely manner can improve machining efficiency and reduce production costs. Attention to detail handling: When clamping workpieces, ensure accurate positioning and firm clamping to prevent wear and damage caused by workpiece loosening or vibration during the machining process. During the grinding process, it is important to constantly monitor changes in grinding force, temperature, and quality, adjust grinding parameters in a timely manner, and avoid wear and damage caused by improper grinding conditions. Strengthen equipment maintenance and upkeep: Develop regular maintenance plans and perform cleaning, lubrication, fastening, and other operations on equipment according to the plan. This helps reduce equipment wear and maintain stable equipment performance. For vulnerable parts and critical components, regular inspections and replacements should be carried out to ensure processing quality and equipment safety. Strengthening the lubrication management of equipment is also an important part of maintenance and upkeep. Suitable lubricants and lubrication methods should be selected to ensure effective lubrication of the friction between various components of the equipment, reducing wear and heat generation. Follow safety operating procedures: During the operation process, it is necessary to follow safety operating procedures to ensure personal and equipment safety. Avoid overloading the equipment to prevent damage to it. Pay attention to safety protection, such as wearing protective goggles, work clothes, etc., to reduce damage caused by improper operation. Strengthen equipment troubleshooting and maintenance capabilities: promptly handle any faults that occur to prevent them from escalating. Strengthening equipment troubleshooting and maintenance capabilities can help identify and solve problems in a timely manner, avoiding further deterioration of wear and damage.
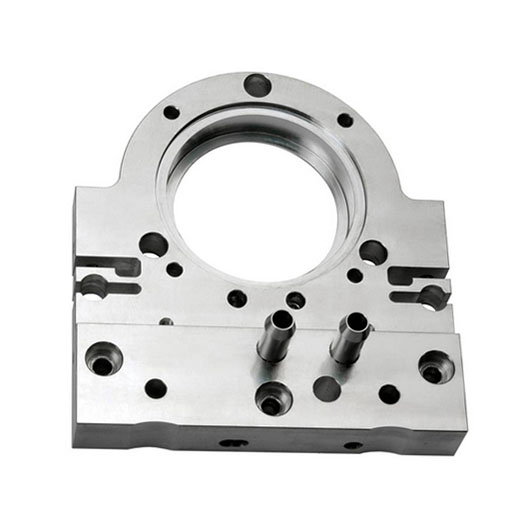