In the process of CNC Machining, technical requirements mainly focus on ensuring machining accuracy, surface quality, dimensional stability, and proficiency in machine operation. The following are some main technical requirements: ① Accuracy requirements: Dimensional accuracy: CNC machining can achieve high dimensional accuracy, usually reaching tolerance requirements of 0.01mm or less. Shape accuracy: In addition to dimensional accuracy, CNC machining also needs to ensure the shape accuracy of the parts and ensure that each part of the parts meets the design requirements. Position accuracy: Position accuracy refers to whether the relative position relationship between each point on the part meets the requirements, which is also an important technical indicator of CNC machining. Surface quality requirements: Surface roughness: CNC machining should be able to control the surface roughness of the part to meet specific requirements. Usually, the surface roughness can reach Ra 0.8 μ m or less, and sometimes even Ra 0.4 μ m or less, to ensure the smoothness and quality of the part surface. Surface smoothness: smoothness is the smoothness of the surface of a component and an important indicator of surface quality. CNC machining can ensure the surface smoothness of parts by selecting appropriate cutting parameters and coolant Dimensional stability requirements: Dimensional stability is an important guarantee for the long-term use of parts, which involves multiple aspects such as thermal stability and mechanical stability of parts. CNC machining requires reasonable process design and process control to ensure the dimensional stability of parts. Proficient in operating CNC machine tools: ④ Operators need to be proficient in various operations of CNC machine tools, including startup, shutdown, manual operation, program editing, error handling, etc., and understand the basic principles and operating procedures of CNC machining. Operators also need to master basic mathematical knowledge, such as trigonometric functions, vector operations, coordinate systems, etc., in order to perform related mathematical calculations and image drawing Process control: In CNC machining, strict monitoring and control of the machining process are required to avoid the occurrence of machining errors. This includes selecting appropriate machining equipment, cutting tools, cutting parameters, etc., as well as real-time monitoring and adjustment of the machining process Digital Design and Programming: CNC machining typically requires the use of CAD (Computer Aided Design) software for 3D model design of workpieces, and CAM (Computer Aided Manufacturing) software for machining path planning and CNC programming. Operators need to be proficient in using these software and be able to develop high-quality CNC programs according to design requirements Quality control and testing: In the CNC machining process, strict control and testing of machining quality are required. This includes using various measuring tools and equipment to inspect the size, shape, positional accuracy, and other aspects of the processed parts to ensure that the processing quality meets the design requirements.
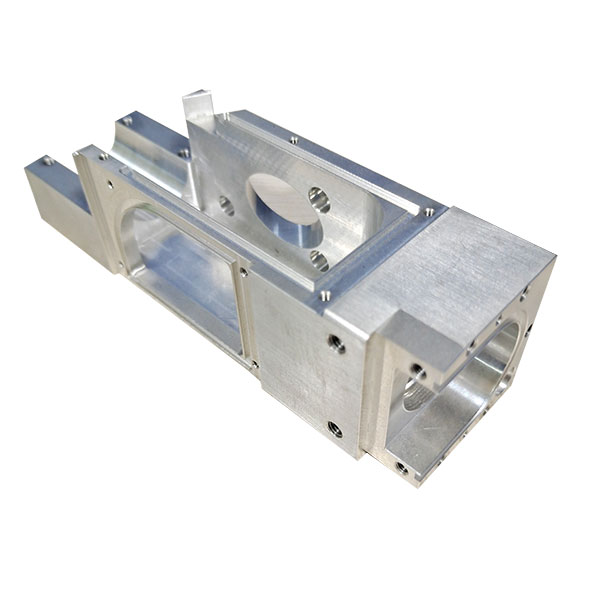