Analysis of Design Principles for Mechanical Processing Technology of Parts
Principles for selecting positioning benchmarks. The positioning reference refers to the surface where the part is in the relative position between the machine tool and the tool during mechanical processing. On the other hand, the parts use the most primitive unprocessed surface during the first machining. This is a rough standard. What are the principles for selecting rough and fine machining benchmarks when using precision machining benchmarks for positioning after original machining.
When selecting rough reference machining parts, it is necessary to ensure sufficient material and sufficient margin on the machined surface. In addition, the dimensions and positions of the machined surfaces of unprocessed parts must comply with the requirements of the machining drawings. Ensure that the surface of the parts is easy to locate, clamp, and process, and the selected clamping should be as simple as possible. The machining surface and machining surface must be determined, and the correct position selection should generally be based on the machining surface as a rough reference.
The principle to follow when choosing a precision base is to first observe whether the precision reference surface is easy to position and clamp for processing, and select one as the precision base. The timing of selecting other surfaces and unifying the positioning method of the selected surface can improve processing efficiency, so careful consideration must be given when positioning the precise surface. The precision machining benchmark adopts the correct coincidence principle of using a unified positioning principle to position and precision machine other surfaces.
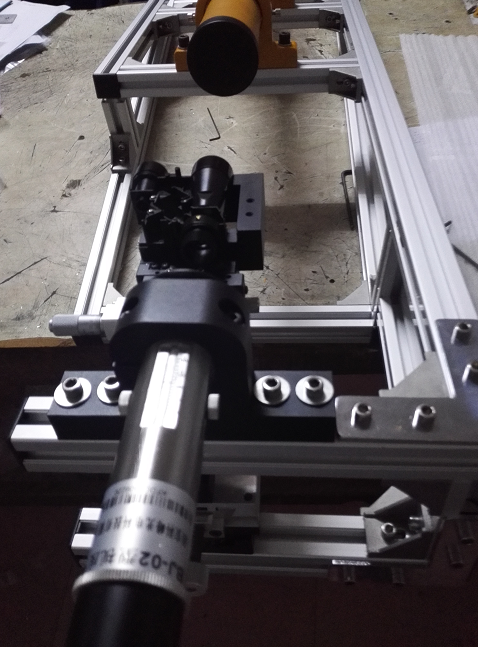