Introduction to the process of Sheet Metal Processing in Shenyang: Material selection: The materials commonly used in sheet metal processing include cold-rolled plate (SPCC), hot-rolled plate (SHCC), galvanized plate (SECC, SGCC), copper (CU), brass, purple copper, beryllium copper, aluminum plate (6061, 5052, 1010, 1060, 6063, hard aluminum, etc.), stainless steel (mirror, brushed surface, matte surface). Depending on the product effect, different materials are selected, and the product's purpose and cost generally need to be considered.
1. Cold rolled SPCC is primarily used for electroplating and baking paint parts, with low cost, easy molding, and a material thickness of 3.2mm.
2. Hot rolled plate SHCC, material T3.0mm, also uses electroplating and baking paint parts, with low cost but difficult to form, mainly using flat parts.
3. Galvanized sheet SECC, SGCC. SECC electrolytic plates are divided into N material and P material. N material is primarily not treated for appearance and has a high cost, while P material is used for spraying parts.
4. Copper; The primary use of conductive materials is nickel plating, chrome plating, or no treatment on the surface, which incurs high costs.
5. Aluminum plate; Generally, surface chromate (J11-A) is used for oxidation (conductive oxidation, chemical oxidation), with high cost. Silver plating and nickel plating are available.
6. Aluminum profiles; Materials with disordered cross-sectional structures are widely used in various plug-in boxes. The exterior treatment is the same as aluminum plate.
7. Stainless steel; First and foremost, it is not used for any external treatment and has a high cost.
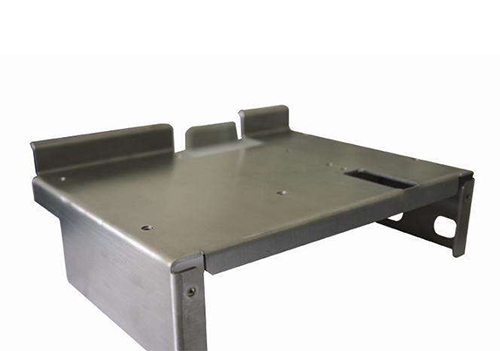
Drawing review: To write the process flow of a part, it is necessary to first understand the various skill requirements for the part drawing; The review of drawings is a crucial step in the development of the part manufacturing process.
1. Check if the drawing is complete. 2. Connect the drawing and view, indicate whether the markings are clear and complete, and indicate the units of dimensions. 3. Installation contact, installation requirements include key dimensions. 4. Differences between the old and new layouts. 5. Translation of foreign language images. 6. Conversion of table codes. 7. Reflection and placement of graphic problems. 8. Materials. 9. Quality requirements and process requirements. 10. The official release of drawings must be stamped with a quality control seal.
The content of the article is sourced from the internet. If you have any questions, please contact me to delete it!