What are the specific problems that Metal Stamping factories encounter when processing metal stamping parts, big and small? Let me briefly explain:
1. Poor phenomena such as adhesion or scratches on the surface of metal stamping parts or molds due to friction between the material and the convex or concave molds;
2. The occurrence of burrs during the processing of metal stamping factories is mainly caused by the gap between the cutting die and the cutting die, and the burrs generated when the gap between the cutting edges is large or small;
3. There are foreign objects in the unwinding line, including iron filings, rubber, dust, and other impurities that cause bumps and depressions; Due to uneven stress, poor matching of stretching ribs, or poor control of the pressure slider, the R corner or embossed area of the workpiece may experience twisting and bending;
5. Wrinkles: Wrinkles on the edges or R area caused by poor adjustment of the press slide, low accuracy of the press, inappropriate adjustment of air cushion pressure, or large punch or R area;
6. Line offset: During the processing and forming of the workpiece, the part that first comes into contact with the metal stamping mold is squeezed into a line or the like.
Hardware stamping factories can analyze these issues to find prevention methods and solutions. It can greatly reduce losses.
This article is from EMAR Mold Co., Ltd. For more EMAR related information, please click on www.sjt-ic.com,
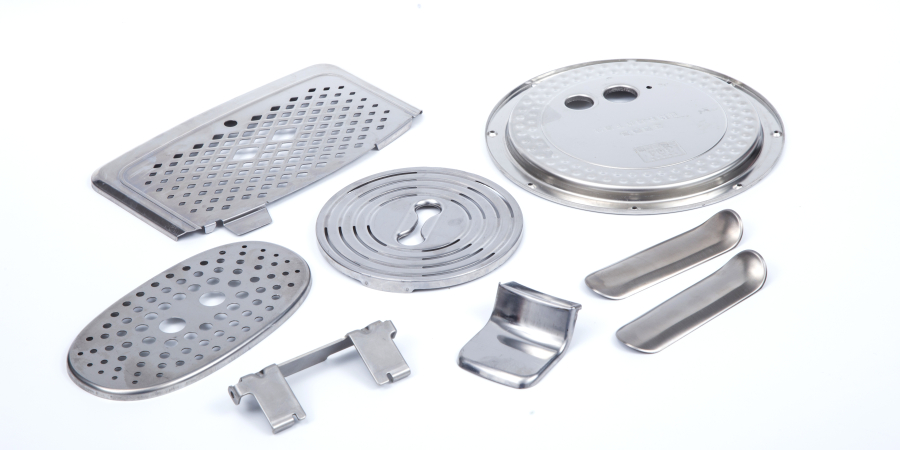