Flange processing typically requires the use of a range of specialized equipment to ensure high quality, accuracy, and efficiency. The following are some common flange processing equipment:
Forging machinery: used for forging metal billets, it can be a hammer forging machine, a press, or other professional forging equipment. These devices are used to preliminarily form contours for flanges. CNC machine tool: used for fine cutting and shape machining on flanges. CNC milling machines, CNC lathes, and other machine tools can perform precise machining according to design requirements. Heat treatment furnace: used for heat treatment of flanges to improve their mechanical properties. Including quenching, tempering and other processes. Welding equipment: used for welding the connecting parts of flanges. This may include methods such as manual welding, automated welding, or laser welding. Surface treatment equipment: used to treat the surface of flanges, such as polishing, sandblasting, coating, etc., to increase their corrosion resistance or improve their appearance. Measurement and testing equipment: including coordinate measuring machines, gauges, microscopes, etc., used to test the size, shape, and surface quality of flanges. Laser cutting machine: used to cut the shape of flanges according to design requirements. Cold stamping press: used for stamping, forming and other operations on flanges. Hydraulic press: used to apply pressure on flanges to achieve specific shape forming. CNC laser cutting machine: used for high-precision cutting, especially suitable for complex contour flanges.
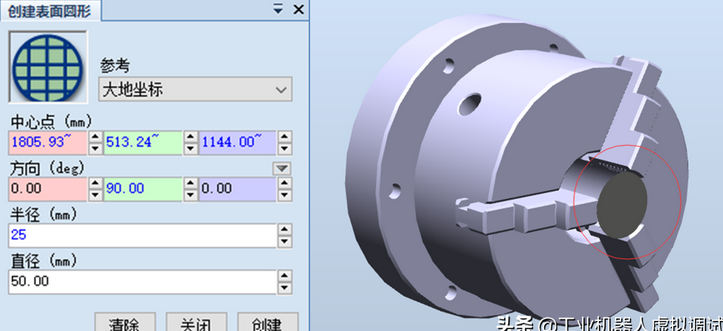
This is just a common equipment list, and specific equipment requirements may vary depending on the type, size, and purpose of the flange. In actual production, it is usually necessary to choose appropriate equipment based on specific production processes and product requirements.