Almost all stamping factories know that stainless steel sheets are difficult to deep draw and have quality problems such as wrinkling or cracking during deep drawing. So how can stainless steel stamping parts overcome these problems during deep drawing processing?
The above issues are determined by the function of stainless steel itself, primarily influenced by the following five factors: first, the function of the raw materials; The second is the structure and stamping speed of the mold; The third is the mold material; The fourth is stamping smoothing agent; The fifth is the organization of the process road. Let's explain in detail below.
1. It is necessary for the quality of raw materials and boards to comply with the national standard for conventional raw materials. It is necessary to anneal hard materials before stamping to improve processing functionality.
2. In order to improve the difficulty of deep drawing, the mold structure and stamping speed can tilt the edge pressing surface of the billet holder, allowing the billet to fully touch the surface of the billet and the mold under the action of the edge pressing ring; Make the material in the corners of the mold subject to greater edge pressure, thereby increasing the difficulty of deep drawing. It is necessary to use anti stick mold materials. The primary anti sticking mold materials currently available are:
(1) Hard alloy: tungsten carbide steel bonded hard alloy, non stick mold, high mold life. Zui has good anti adhesive properties, but the mold material and heat treatment are relatively high, making it suitable for large-scale production.
(2) Copper based alloys: cast aluminum bronze and hard aluminum bronze, non stick to molds, with a general service life. The heat treatment is simple and suitable for small and medium-sized production.
(3) 3054 alloy cast iron, non stick to molds, with a general service life. Requires surface quenching, suitable for medium to small batch production. In practical production, stamping factories can select suitable materials based on their own heat treatment equipment, output value, cutting ability, stamping requirements, etc.
4. When drawing, it is necessary to smooth the oil appropriately to reduce the friction coefficient between the material and the mold, thereby reducing the drawing force. Compared with no smoothness, the pulling force can be reduced by about 30%. Moreover, it can improve the deformation degree of the material, reduce the ultimate drawing coefficient, decrease the number of drawing cycles, and more importantly, ensure the surface quality of the workpiece without forming surface scratches.
This article is from EMAR Mold Co., Ltd. For more EMAR related information, please click on www.sjt-ic.com,
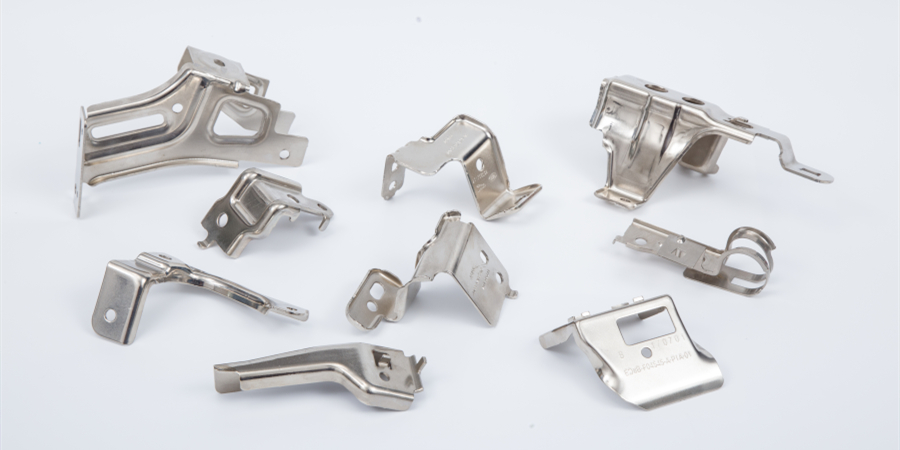