1. CNC Machining has high precision and stable quality
The machining process of CNC machining center machine tools is operated according to the pre input program of the computer. As long as the information instructions are correct, the accuracy of the CNC lathe can be guaranteed, thereby avoiding product quality differences caused by different operator skill levels. The machining of parts in CNC machining centers has high repeatability and precision, ensuring uniformity and stability when machining the same part. Moreover, it is known that CNC part machining is not affected by human factors.
2. Strong CNC machining capability and flexibility
The key to the operation of a CNC machining center lies in the machining program. When machining different parts, it is only necessary to create or modify the machining program from scratch to quickly meet the machining requirements, without the need to adjust the machine tool. This greatly shortens the skill preparation time for replacing hardware on the machine tool. CNC is suitable for the production of multiple varieties, single pieces, or small batches of parts. For parts with messy shapes, it is almost impossible for ordinary machine tools to complete them, while NC machine tools only need to develop corresponding programs and can also process some precision and messy parts.
3. Reduce labor intensity and improve working conditions
The machining process of a CNC machining center is spontaneously completed by the machining program. Generally speaking, the operator does not need to perform panel operations, workpiece loading and unloading, tool preparation, center measurement of key processes, or machine tool operation. There is no need for deep repetitive manual work, which reduces the physical labor of employees and correspondingly improves working conditions.
4. CNC machining centers have high production efficiency and low cost
The movement speed of the moving parts in the CNC machining center is fast, and the replacement of workpieces basically does not require the adjustment of the machine tool from scratch. Moreover, the machining accuracy is relatively stable, and only initial product inspection and critical scale sampling inspection between processes can be carried out. This greatly reduces the auxiliary production time such as stopping inspection, improves machining productivity, and reduces machining costs. Moreover, the larger the production batch, the lower the machining cost.
5. High economic benefits
The advantage of NCC machining center parts processing skills is that when changing the machining target, only the machining program needs to be written from scratch, without the need to create or replace new machine tools. For parts with messy shapes and high precision, using CNC lathes can reduce the types and number of ordinary lathes, effectively save equipment costs, and facilitate better reproduction for enterprises. When producing single pieces or small batches, using CNC parts for machining can adjust, process, and reduce inspection time, directly saving production costs. The quality of CNC machining is stable, which can reduce and avoid the generation of waste, lower production costs, and achieve good economic benefits.
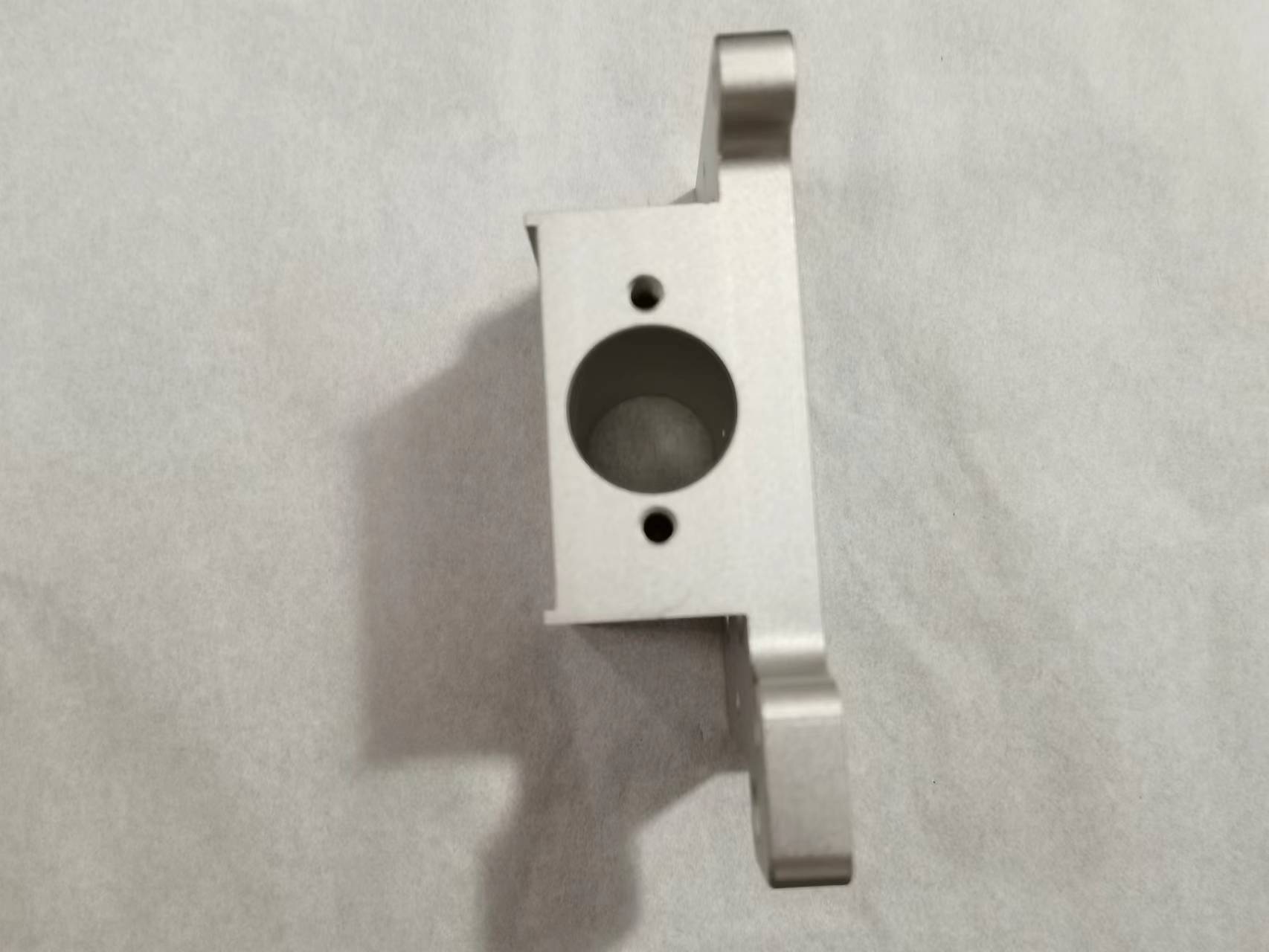