Why should precision stamping molds be polished? The main purpose of polishing is twofold. Firstly, it can increase the brightness of the mold and improve the aesthetic appearance of the workpiece. Secondly, it can make the mold easy to demold. Next, EMAR will take you to understand the most common polishing methods for precision stamping.
1. Mechanical polishing: Mechanical polishing is a method of polishing a smooth surface by removing the convex parts after polishing through deformation processes such as cutting precision stamping molds and plastic deformation of material surfaces. For precision stamping workpieces with high surface quality requirements, ultra precision polishing can be used. Ultra precision polishing uses specially designed grinding tools, which are pressed tightly against the surface of the workpiece to be processed in a polishing solution containing abrasives, and perform high-speed rotational motion.
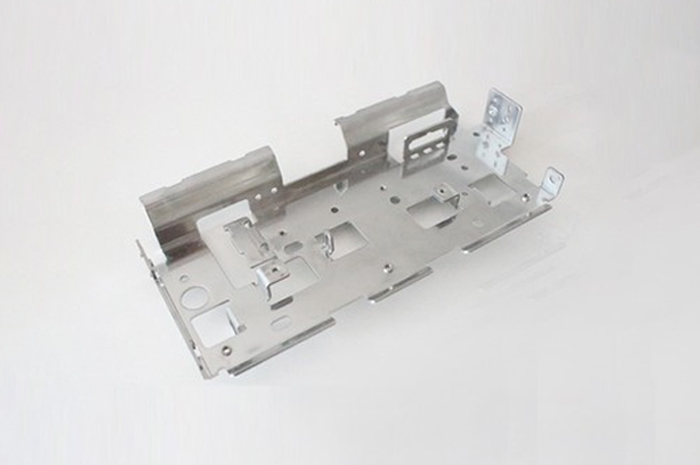
2. Electrolytic polishing: Precision stamping molds can be smoothed by removing small protrusions on the material surface through electrolytic polishing. Compared with chemical polishing, it can eliminate the influence of cathodic reactions and achieve better results.
3. Ultrasonic polishing: Place the material to be polished into a grinding suspension and place it together in an ultrasonic field. Then, through the oscillation of ultrasonic waves, the abrasive is ground and polished on the surface of precision stamped workpieces. Ultrasonic processing has low macroscopic force and will not cause deformation of the workpiece, but it will make the production and installation of precision stamped workpieces more difficult. Ultrasonic processing can be combined with chemical or electrolytic methods. On the basis of solution corrosion and electrolysis, ultrasonic vibration is applied to stir the solution, causing the dissolved products on the surface of the workpiece to detach and the corrosion or electrolyte near the surface to be uniform; The cavitation effect of ultrasound in liquid can also suppress the corrosion process, which is beneficial for the surface brightening of precision stamped workpieces.