The CNC Machining center is mainly composed of mechanical equipment and numerical control system, with its own tool library and automatic tool changing function. After one clamping of the workpiece, it can continuously perform multiple machining processes such as drilling, boring, milling, reaming, and tapping, greatly reducing the clamping time of the workpiece and the auxiliary process time such as measurement and machine tool adjustment. The CNC machining center has a series of performance requirements during operation, which ensure high precision and repeatability of part processing, as well as stable operation of the equipment. Firstly, the cutting speed and feed rate of CNC machining centers are key performance indicators. The selection of spindle speed and feed rate directly affects machining efficiency and quality. For different materials and processing requirements, it is necessary to set the spindle speed and feed rate reasonably to achieve good cutting results. Secondly, machining accuracy is another important performance requirement for CNC machining centers. This includes aspects such as geometric shape accuracy, positional accuracy, and surface roughness of the workpiece. CNC machining centers need to ensure the dimensional and shape accuracy of workpieces during the machining process to meet design requirements. Meanwhile, surface roughness is also an important indicator for measuring machining quality. CNC machining centers need to control the surface roughness of workpieces through reasonable cutting parameters and tool selection. In addition, the rigidity and stability of CNC machining centers are also very important performance requirements. Rigidity determines the ability of a machine tool to resist deformation during the machining process, while stability affects the ability of the machine tool to maintain accuracy over long periods of operation. To ensure high-precision machining, CNC machining centers need to have good rigidity and stability. Automation and intelligence are also performance requirements for modern CNC machining centers. By adopting advanced numerical control systems and sensor technology, CNC machining centers can achieve functions such as automatic tool changing, automatic measurement, and automatic compensation, improving machining efficiency and accuracy. At the same time, intelligent technology can also help operators better monitor and manage the operating status of machine tools, timely discover and solve problems.
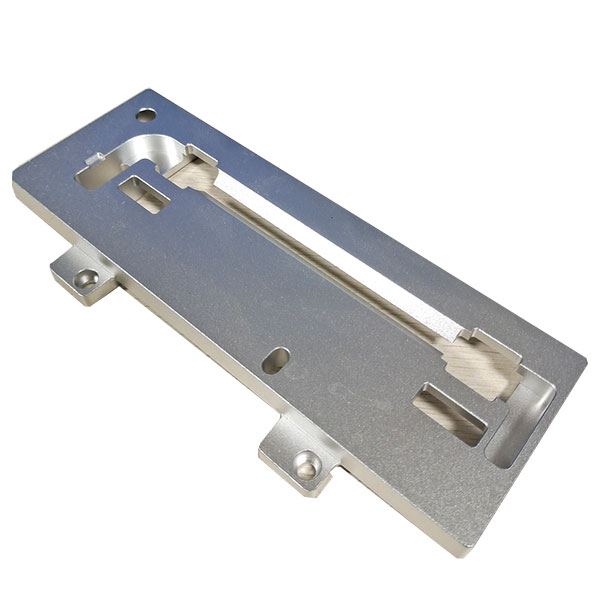