Before 1990, China's Metal Stamping industry was still very weak, and most metal stamping factories were old-fashioned punching machines (those driven by side pulleys). At that time, I once visited a hardware stamping factory, and the transfer of parts was still carried by carrying poles and baskets. With the further development of reform and opening up, more and more foreign-funded enterprises have entered China, and various industries have a large demand for metal stamping parts. At that time, domestic metal stamping parts factories were far from meeting the demand in terms of both output and quality. As a result, many foreign-funded metal stamping factories have set up factories in China.
At that time, the better hardware stamping factories in China were mainly Singaporean and Japanese companies, and Taiwan's hardware stamping factories were considered the second tier. But now it's different. After nearly 20 years of development, our domestic metal stamping factories have taken the lead in continuous stamping, while stamping companies in Singapore and Japan only have brand premiums left.
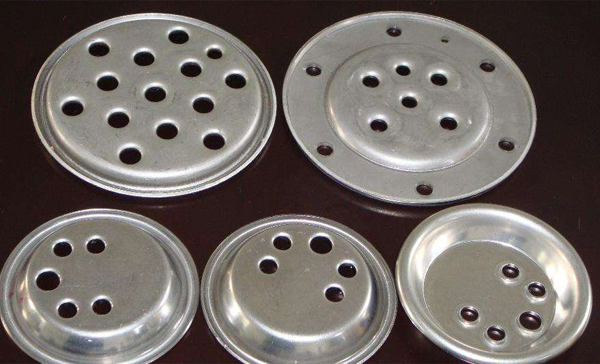
From the history of the development of the domestic stamping industry, it can be summarized into three stages:
The first stage was from 1990 to 2000, a period of rapid development, which can be referred to as the "capability" stage. During this period, there was a shortage of production capacity, with severe demand outweighing supply. Foreign funded enterprises had an absolute advantage in mold making ability and technological level. The sales in the stamping industry are relatively easy to do. Customers bring drawings, and as long as the enterprise has the ability to do it, they are usually assigned. At this time, our domestic hardware stamping parts factories were in the learning and starting stage. Some private enterprises started their own businesses, starting with a punch press (molds can be opened by external companies), developing to two, three, one hundred..., and then developing their own mold technology centers. Many large metal stamping factories were established during this period.
The second stage is from 2000 to 2007, the stage of full competition, which can be referred to as the "price" stage. At this point, more and more hardware stamping parts factories are able to produce them, and the quality has greatly improved. Price competition is extremely fierce. If the customer provides drawings for a quotation and quotes 1 yuan while other companies quote 80 cents, there is a high possibility of losing this order. So the pressure became greater and the profit became lower, and the industry of moving iron was formed like this.
The third stage, after 2007, can be referred to as the "value" stage. Why did we start from 2007? Because Apple's iPhone gradually entered people's lives this year.

The emergence of iPhone has to some extent overturned people's values towards products. Prior to this, Nokia was the absolute king in the mobile phone industry, and prices were getting cheaper and cheaper, with many even offering phones as a free gift when connected to the network. After the iPhone arrived, with a price of over 4000 yuan, everyone still rushed to buy it, staying up late and queuing up to buy it. This is a manifestation of value. In terms of functionality and aesthetics, the iPhone is much stronger, and holding an iPhone makes it look particularly high-end.
At this point, after the customer inquires about the price, they will come to you to discuss why you quoted 1 yuan while others quoted 80 cents, what are the differences between your hardware stamping parts factory's technology and others', how do the differences between hardware stamping parts factories arise, and what benefits can you bring to this product if you are more expensive than others. If there are very sufficient reasons, customers are also likely to purchase at a high price.